Wood that is not given special treatment tends to rot, bend, or crack/break easily. To extend the life of the wood, you can treat it with a product that makes it water resistant. Considerations to make wood waterproof, usually done on wood that is constantly exposed to the weather, such as furniture for the veranda or back porch of the house. Considerations to make wood waterproof is also common in wood for interior materials and kitchen surfaces.
Step
Method 1 of 3: Making Wood Waterproof with Oil
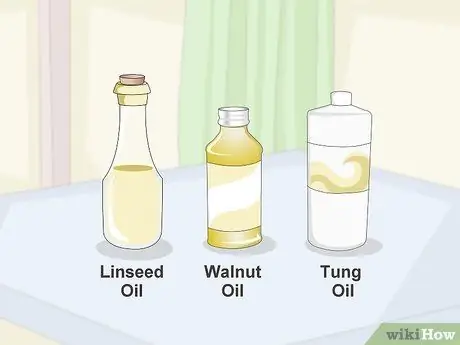
Step 1. Decide what type of oil to use
Three types of oil commonly used to make wood waterproof are linseed oil, walnut oil, and tung oil. Tung oil is typically found as a mixture in most commercial products. Crude tung oil is often more expensive than other types of oil, so it is usually used in smaller wood projects. Walnut oil is the same product you'll find at the grocery store olive oil. Associated with allergies to grains, walnut oil cannot be used commercially.
- Flaxseed oil can be purchased at most DIY repair shops (Do It Yourself), but many of these products are sold raw or boiled. Boiled linseed oil contains toxic metal desiccants. You can still use this product on outdoor patio fixtures, but you shouldn't use it on anything that will come into contact with food.
- Flaxseed oil can also be purchased without metal drying agents. Look for raw linseed oil if you need a safe coating for certain wooden fixtures, such as your kitchen countertops.
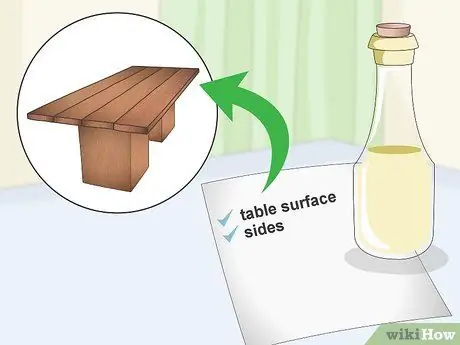
Step 2. Purchase the oil (of your choice)
Do a preliminary inspection of your project and determine which areas of the wood surface need special oil treatment. For larger projects such as a porch deck, consider using an exterior paint and deck sealant (a filling/adhesive or gap filling material commonly used for decks). Oil is good for smaller wooden furniture, such as a cutting board (chopping board), table, kitchen counter, or baseball bat (or baseball).
- Make a list of the wood surfaces you want to coat (with oil). Making this list will help you figure out how much oil to buy. Special treatment of wood with oil is good because the oil sticks well for several years.
- Buy the best oil according to your needs. Buy a large container of oil. Better to have too much than too little.
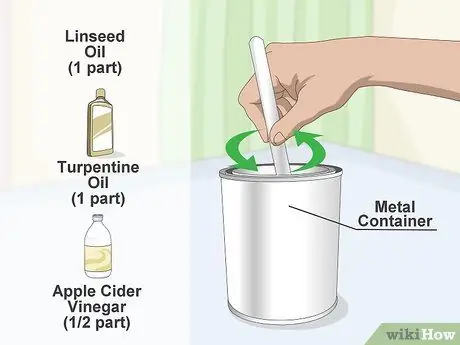
Step 3. Create a mixture
You can make a stronger coating and sealant by mixing turpentine and apple cider vinegar. Mix one part oil (tung, flaxseed, or walnut), one part turpentine oil, and part apple cider vinegar. This mixture will maintain the oil supply and will make the finish last longer.
- Stir the ingredients in a metal container, such as an empty coffee jar. Stir the liquid until everything is mixed.
- There's really no need to make your own mix, but many wood enthusiasts recommend this type of original mix.
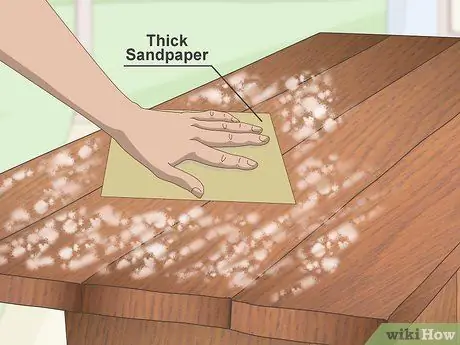
Step 4. Prepare the wood before you apply the oil
Any imperfections on the surface will look more noticeable after the oil is applied. Oil or a mixture of oils will bring out all the colors in the wood. Use heavy sandpaper or a metal file to treat any visible imperfections. Scrape with sandpaper or a metal file until the wood looks even.
- Finish by sanding the entire surface using fine sandpaper (220 grit). Sanding aims to prepare the wood surface so that it can absorb oil.
- Wipe or scrub the area with a dry cloth to remove any sanding residue, before applying the oil. The wood must be dry before you coat it with oil.
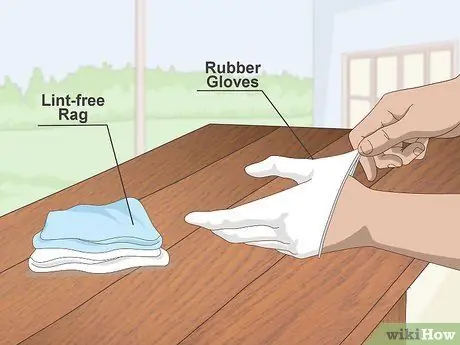
Step 5. Prepare yourself
Fold a lint-free piece of cloth/rag and keep another piece of cloth/rag nearby. Folding the rag is intended to remove rough edges and prevent tearing while spreading the oil. Wear thick rubber gloves when you use turpentine and other products that contain mineral spirits.
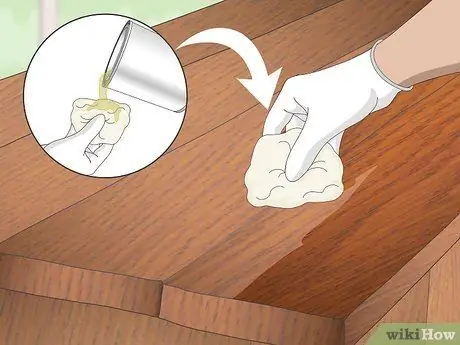
Step 6. Polish the first layer
Pour a little oil on the surface of the cloth / cloth. Do not apply oil directly to the wood. Rub the oil with a cloth in the direction the fibers move from the inside to the outside. Be careful not to touch the oil while the absorption process is taking place. Focus so that the polish is completely even. Apply more oil than you would have to rub too hard to remove the oil from the cloth/rag. Do not allow oil to build up.
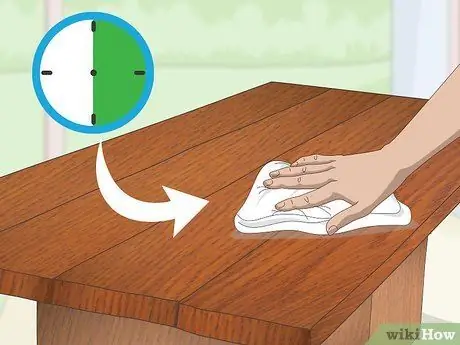
Step 7. Allow the coating to dry
Wait about 30 minutes for all the oil to soak into the wood. Wipe the wood surface with a clean cloth to remove excess oil. Allow the wood to dry for 24 hours, or until dry. It will take more time to make wood waterproof with oil than using a sealant.
Rub the surface with “0000” steel wool (very fine)
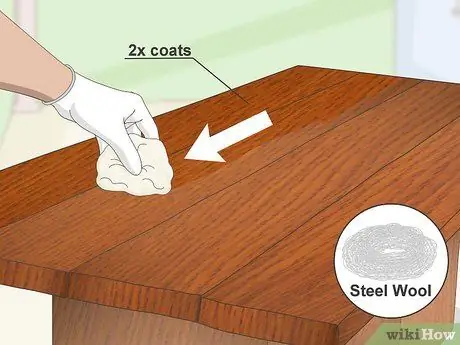
Step 8. Apply two more coats of oil
Again apply a layer of oil to the wood surface. Repeat the same drying time and sand with steel wool. Let the wood sit for a few days to a few weeks before using it. You'll know that the wood has gone through the drying process if you can slide your hand gently across the surface.
Method 2 of 3: Making Wood Waterproof with Sealant
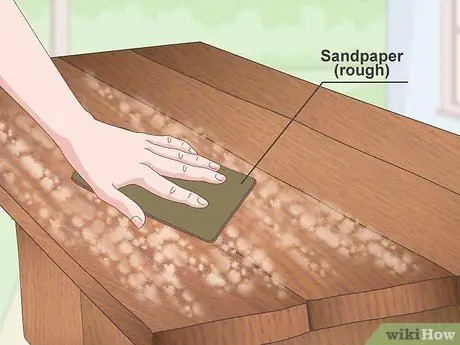
Step 1. Prepare the wooden surface
You will need to remove the old coating before applying the sealant. Use sandpaper before you apply any sealant. It is this cleaning that may be blocking the absorption of the sealant. It is best to use sealants on wood that has been previously coated (paint or other material), as oil-based dyes may not soak into the wood.
Use a coarser sandpaper for any surfaces that require more attention. Next, finish sanding the wood surface with a finer sandpaper to make sure the surface is even

Step 2. Purchase a water-based wood sealer
You can look for these products at home improvement supplies/supply stores (building materials stores). Water Seal and Stain Sealer are popular names for wood sealants. You can also buy colored sealants; before you polish it, sand the surface of the wood first.
- Often sealants are named according to the type of object/surface to be coated. For example, you may find deck sealants, fence sealants, outdoor sealants, floor sealants or furniture sealants.
- Purchase a boat wood sealant, if the wood you are working with needs to withstand moisture, ultraviolet (UV) light and water.
- Check the instructions on the product for specific usage instructions and drying times. Some products can be used with paint sprayers.
- Purchase a paint sprayer or paint brush for sealant application.
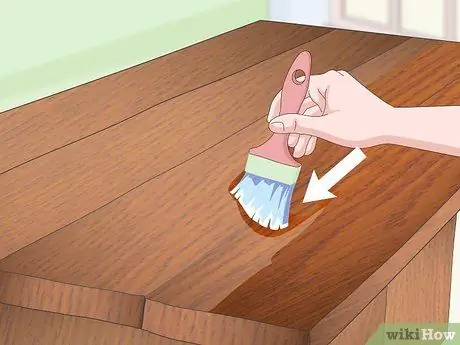
Step 3. Apply the layer evenly
Get a paint brush or paint sprayer and focus on producing an even surface coat. Make sure the temperature and humidity are in a good range suitable for the sealant, otherwise the material will evaporate quickly. Consider working in an area where the humidity is controlled, such as a garage.
Make sure the wood surface is cleaned before applying the sealant
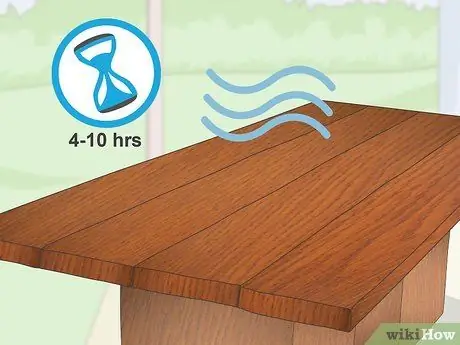
Step 4. Allow the product to dry
Check the instructions on the product packaging for the correct drying time. The sealant drying time will be much shorter than the oil drying time. Many types of sealants require a drying time of between 4 and 10 hours.
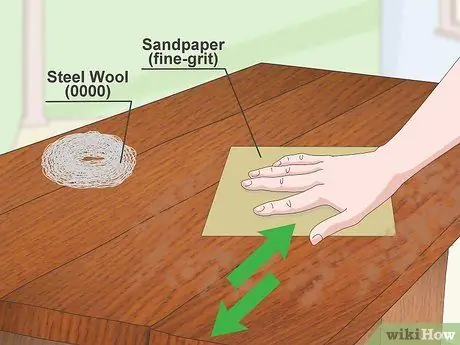
Step 5. Clean the first layer
Use fine sandpaper to improve the adhesion of the second coat, but only if recommended by the product instructions for use. Do this step as soon as the coating dries completely.
You can also use “0000” (very fine) steel wool to clean the sealant
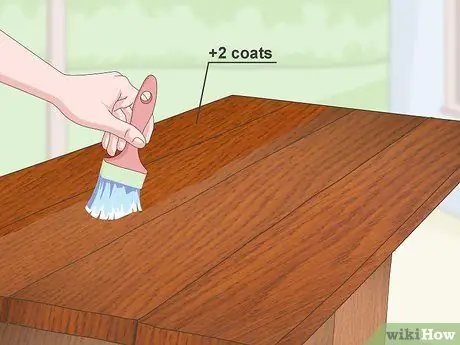
Step 6. Apply the second and third coats
Softwoods may need two to three layers, while hardwoods will only need one layer. Softwood is cheaper wood that has not previously been treated with special care. Popular softwoods are cedar, pine, redwood, and spruce and yew (both types of spruce). Meanwhile, hardwood is thicker and is usually used for higher quality furniture or decking. Popular hardwoods include balsa, beech, hickory, mahogany, maple, oak, and walnut.
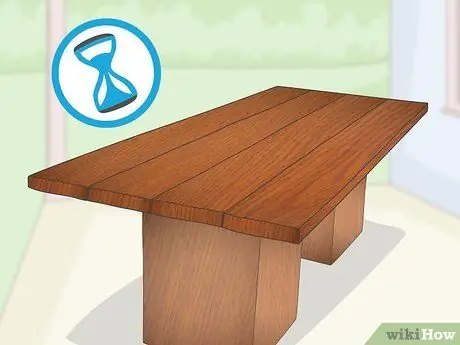
Step 7. Give the wood time for the curing process
Allow the wood to dry for a few days before using the wood or placing the wood furniture. If water is splashed on the surface of the wood, it will darken the wood instead of forming a grain and flowing over the surface.
Apply sealant every few years to keep the wood in good condition
Method 3 of 3: Making Wood Waterproof with Dyes
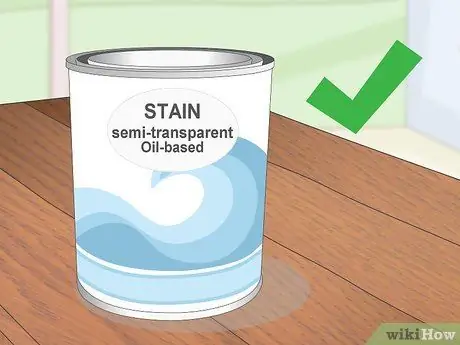
Step 1. Choose an oil-based dye that is semi-transparent
(Note: the dye referred to here is a wood stain, which does not completely cover it but gives a transparent effect so that the wood fibers are still visible). If you plan to handle wood for outdoor purposes, get a wood dye type for exterior qualities. The lighter the dye, the more oil it contains. Light stains are great for interior projects or for types of wood that aren't exposed too much outside.
These products can be found at any hardware store or repair shop
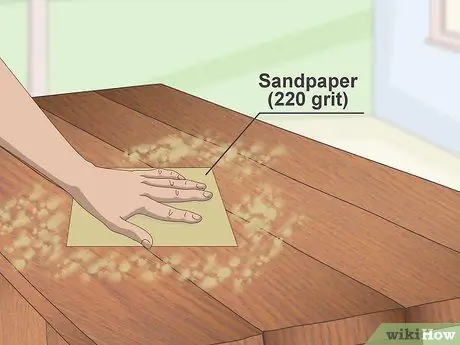
Step 2. Prepare the wood
Any imperfections will stand out more after the dye is added. The dye will bring out all the colors in the wood. Use heavy sandpaper or a metal file for any visible imperfections on the wood surface. Scrape the surface with sandpaper or a metal file until the wood looks even.
- Finish by sanding the entire surface of the wood using fine sandpaper (220 grit). Sanding allows the dye to be applied evenly.
- Wipe or rub each scraped area with a dry cloth to remove any dirt, before you apply the dye. The wood must be dry before dyeing it.
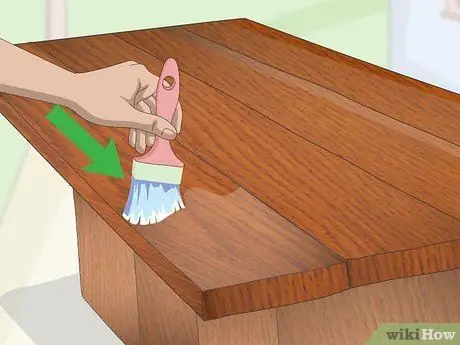
Step 3. Polish the first layer
Apply the dye with a paint brush evenly. Cover the entire surface and then let it dry. Dry the wood for four hours to a day before you apply the next coat.

Step 4. Wipe off any excess dye
Smooth the dry surface with fine sandpaper. Wipe with a tack cloth (low lint cloth that tends to have high strength) to prepare the surface to receive a second coat of polish. It is very important to make the wood surface dry and clean before additional coating can be applied.
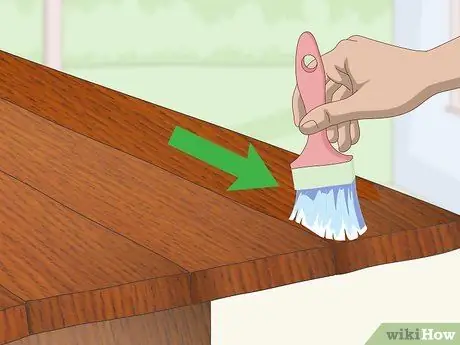
Step 5. Polish the second layer
This second coat will take a little longer to dry. Make sure you allow plenty of time to dry so that the waterproof coating oil is absorbed. Check the dye five hours after applying the second coat.
You'll notice that the stain has dried when the wood is no longer sticky to the touch
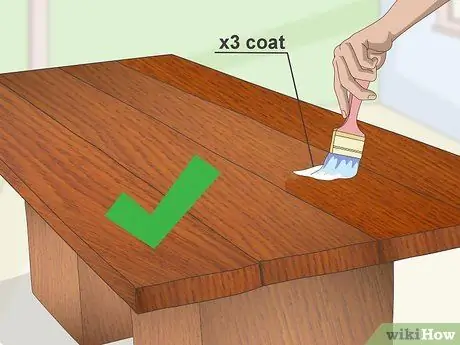
Step 6. Polish the third and final layer
Follow the same procedure as when you applied the last coat of dye. Be patient and make sure to apply the last coat evenly throughout the process. Leave it for three days to a week before using it.