One of the things that makes a person uneasy is not having a knife! Perhaps at one time you were in a situation that required you to make your own knife. This can happen, and if you have experienced it, this article is sure to come in handy!
Step
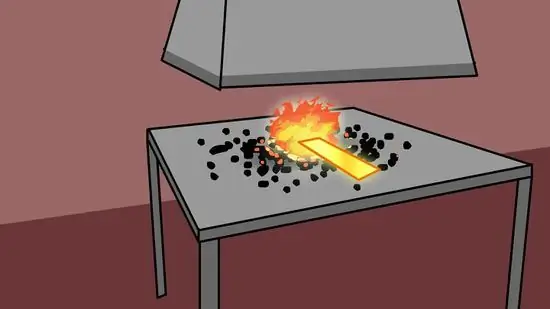
Step 1. Heat the metal in a forging or metal heating furnace
The exact temperature will vary, but air-blown charcoal fire will suffice.
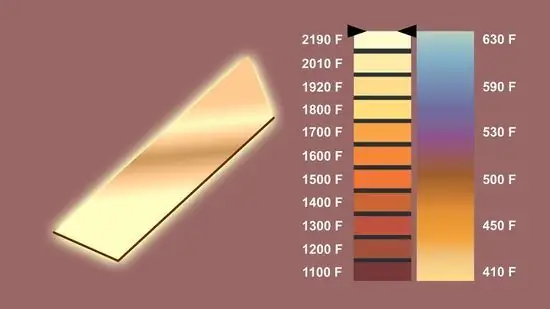
Step 2. Check the color of the metal when heated
Steel should reach a temperature of 1,150 to 1,200 °C, which is when it becomes yellow or straw-like in color.
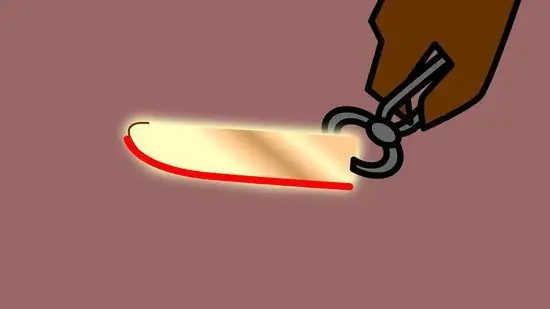
Step 3. Forge the knife until the straight part of the blade becomes the sharp edge
The curved part of the blade will become the back of the knife when it's finished.
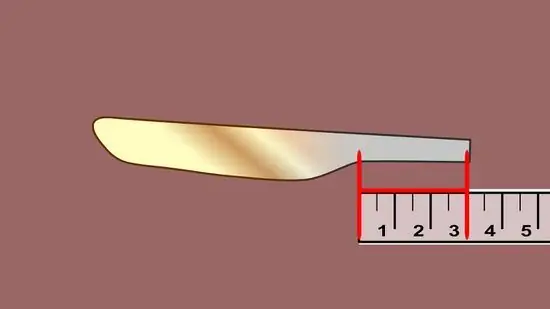
Step 4. Save the metal for the pliers (the part used as the handle)
Leave about 5 cm or so on one end of the metal.
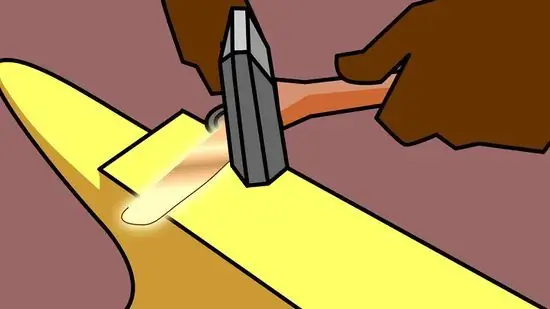
Step 5. Shape the blade of your knife
Apply small, repeated strokes with a 1.5 kg hammer (the exact weight depends on your size and strength) along the blade so that the steel becomes longer and sharper. Do this on both sides so the blade doesn't twist.
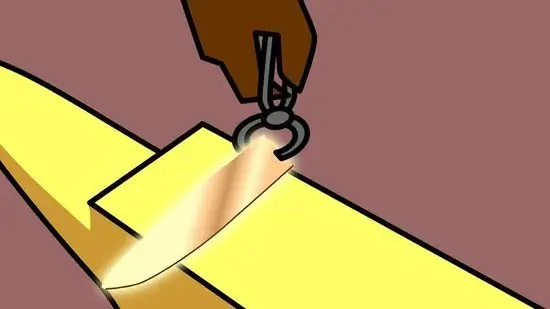
Step 6. Hit the straight side of the blade to sharpen it
Keep in mind that this may cause the blade to bend toward the back of the blade.
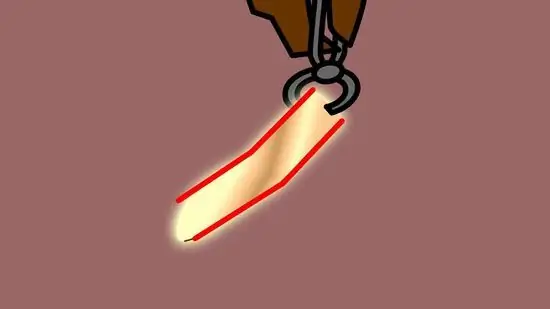
Step 7. Take care that the knife does not bulge or warp on its own
This can cause inclusions that make the blade mushy.
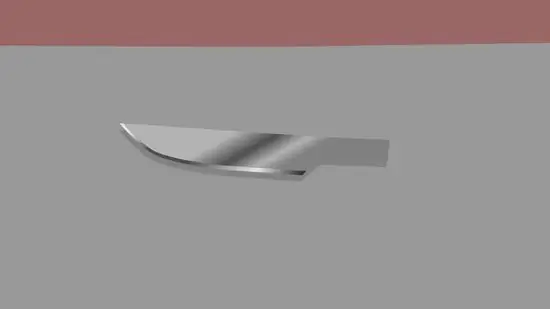
Step 8. Annealing (steel is heated then slowly cooled)
While the blade is still rough, you can anneal it by heating the blade until it is red and non-magnetic 3 times, then let it cool until the red color disappears. After the third heating, leave the blades in the oven and let them cool overnight. This very slow cooling process makes the blade softer and easier to file.
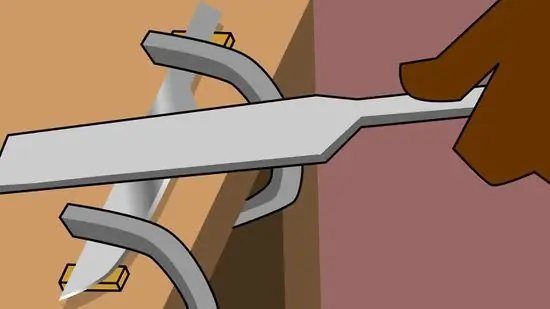
Step 9. File the blade and smooth the surface that is still protruding
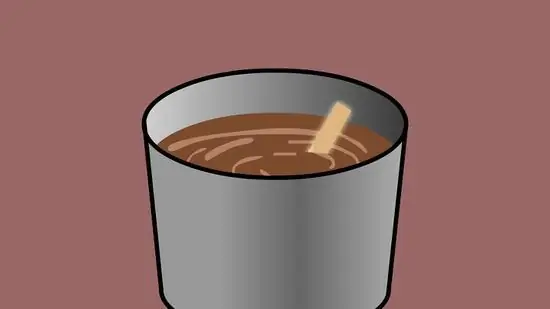
Step 10. Reheat the blade to a nonmagnetic state and dip it in oil to harden it (some steels must be hardened with oil, water and air)
Only dip the sharp part of the blade to make it tough and durable, while the back of the knife remains flexible. Overall, this will increase the durability of the knife. If you dip the knife vertically, the corners on the sides of the blade will lift and create bubbles around the metal, causing the blade to warp so you have to reforge it.
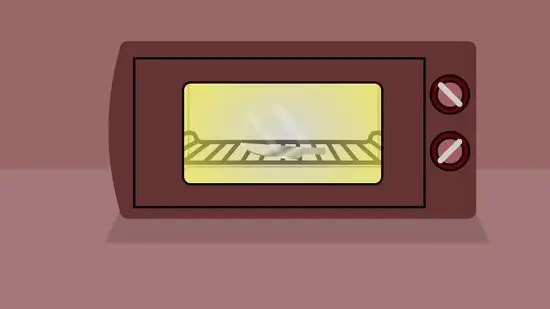
Step 11. Put the blade in the oven for an hour or two at 120-180 °C to soften it (tempering)
You can also leave it in a hot place covered in coal, such as in a makeshift brick box.
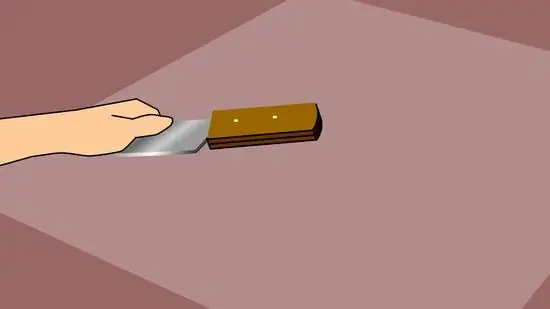
Step 12. Attach the handle
You can punch holes in the knife pliers, then stick them with wood and secure them with rivets. Or, you can also make sharp pliers and insert them into a wooden handle, then sand them into the desired shape.
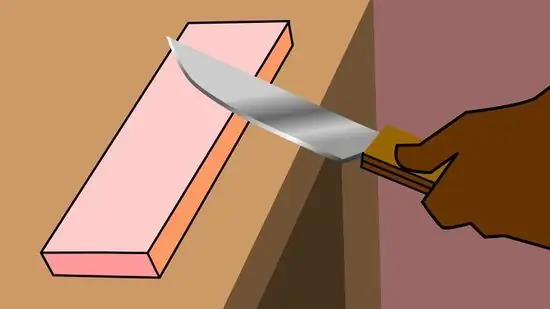
Step 13. Sharpen the knife with fine sandpaper, then continue with the whetstone
As a final step, use a leather strop that has been smeared with polishing paste to remove the burr (the rough part of the blade after sharpening) and make the knife razor sharp.
Tips
- The anvil (forging anvil) must be placed precisely at the level of the blacksmith's knuckle. If the height is not adjusted properly, you can suffer from back pain and not be able to forge the knife properly.
- Increase your flight hours. Your knife making skills will improve even more if you keep taking the time to do it.
- Don't expect your first knife to be good unless you're already an expert at blacksmithing. It will take you months or years to do well. As learning materials, make simple tools such as hammers, punching tools, nails, and so on. It can also reduce embarrassment when you're in training and can only produce a spoon, not a knife.
- Forge the metal evenly on both sides to make it uniform.
- Only forge the metal of the blade when it is hot red or hotter, but don't overheat the metal to spark sparks. Some metals will begin to lose their chemical bonds and become brittle when cooled, such as iron and cast iron.
- Do not be too hard when hammering the metal, even if the surface is flat, the knife can be deformed.
- If you want to make the knife in an easier way, use thin metal no more than a brass key thickness. Do cold forge / cold forge (forge metal without using heat) and shape according to taste. File the sharp edges, then sharpen the blade with a whetstone or fine sandpaper.
- Choose a durable metal. Steel is the best metal for making any tool or product, but it is expensive and difficult to work with. Do not use soft metals such as zinc, lead, and so on. If you only have the metal in small pieces, melt it all together, but be careful about the melting and boiling points of each metal. Also be careful when mixing it.
- Do not use hazardous materials (even acids only) on clean, formed and plated metal. Melting lead ingots can cause serious health problems in the long run. If you don't know what type of material it is, try melting a small pinch of it at different temperatures of the metal. Wear a mask and protective eyewear when testing unknown materials.
- For your convenience, make a clay mold and melt the metal in the mold before you use the anvil. Metal that has been molded will be easier to shape and sharpen.
- Do not touch hot metal. Wait for the metal to return to its original color when it cools down.
Warning
- When quenching (quick cooling in step 9) on the sharp edge of the knife, there is a possibility that the blade will warp.
- Metalworking is a very dangerous thing. Act smart, focused, and careful when in the forging room. When handling uncooled metal, use pliers, not bare hands.
- Your knife can be very sharp. Don't test it on the thumb!
- Do not place the tool near or in the forging furnace for more than 10 seconds, and do not touch it with your hands. Let the equipment cool down first.