If your screwdriver keeps slipping out of the screw head, the friction or torque of the screwdriver will need to be increased. There are several simple ways to improve screw grip using household materials. For a screw that is completely stuck, you will need a special tool to remove it. However, most of the methods below don't cost a lot of money and are widely available in stores.
Step
Method 1 of 4: Using a Screwdriver
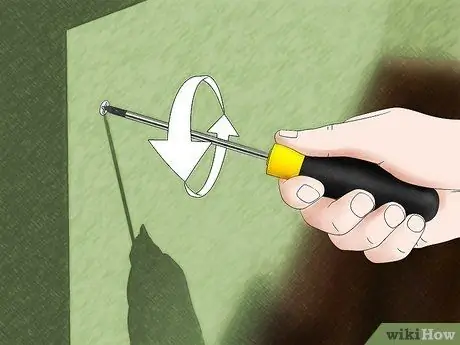
Step 1. Maximize grip strength
If you can still grip the screw head with the screwdriver, try removing the screw by hand one last time. Follow these guidelines to increase your chances:
- If the screw gets stuck in the metal, spray some penetrating oil (such as WD40) and let it sit for at least 15 minutes.
- Use the largest manual screwdriver that fits the screw head.
- If possible, grip the screwdriver handle with a wrench for added support.
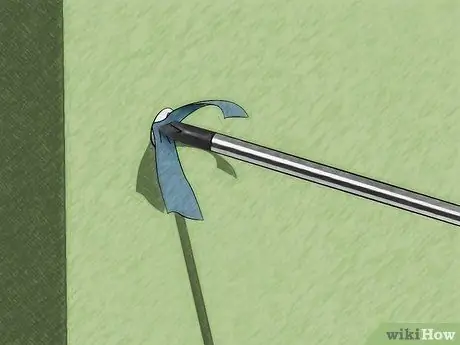
Step 2. Add ingredients to strengthen the grip
If the screwdriver keeps slipping out of the threaded screw, cover the screw head with a piece of material to increase grip. Press the screw holes covered in the material with a screwdriver and try again. Here are some materials you can use:
- Wide rubber, cut to fit the screw size
- Steel wool.
- The green abrasive side of the kitchen sponge.
- Great tape. Attach the non-adhesive side of the tape to the screw head
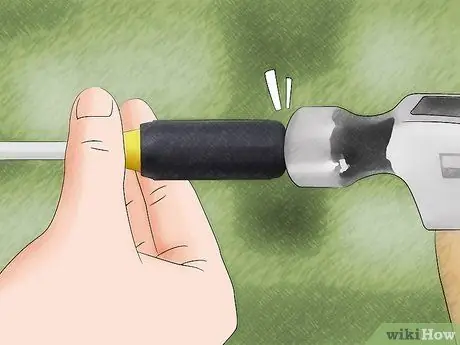
Step 3. Tap the base of the screwdriver onto the screw using a hammer
Tap the screwdriver gently so that the screw head does not break. Skip this step if the screwed object is fragile enough.
- This option is great when your Phillips screw heads are threaded.
- You can also hammer a #1 square drill bit into the screw head with a hammer. Hit until the drill bit penetrates into the screw head of the fluted Phillips screw.
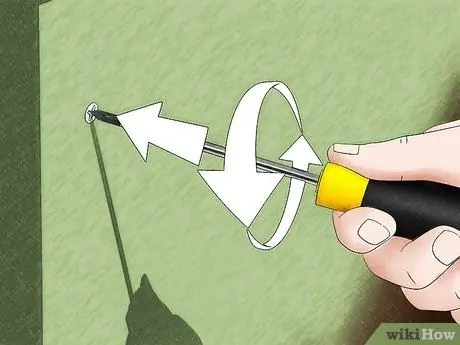
Step 4. Press down while turning the screwdriver
Hold the tip of the screwdriver in your palm, and place your arm directly behind it. Press the forearm all the way down towards the screw while turning the screwdriver.
If the tool you are using slips, stop using it. If you force it, the screw will only get thinner and harder to remove. You have to make sure the screws are turned in the right direction. Usually (but not always), the screw is turned counterclockwise. Press down as hard as you can while unscrewing the screw to prevent it from slipping
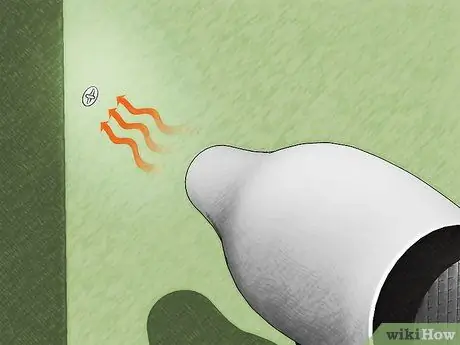
Step 5. Heat the screw area
If you can heat the screw without damaging the object it is screwed into, the screw grooves can be loosened. Use a heat gun or propane torch on the screw and keep the gun/torch moving to prevent overheating. Once the screw is hot enough to hiss dripping water, allow it to cool, then try removing the screw again.
This method is most effective if the screws have been secured with adhesive
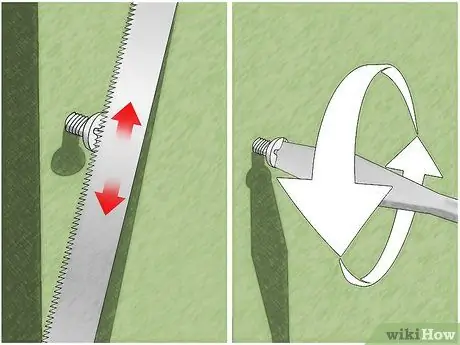
Step 6. Make a recess in the head of the flat-head screwdriver with a Dremel or saw
If your screwdriver still doesn't grip the screw properly, cut a recess in the screw head. Insert a flat-head screwdriver into the newly created recess, and try turning the screw. You can combine this method with the methods above.
Method 2 of 4: Using Impact Driver
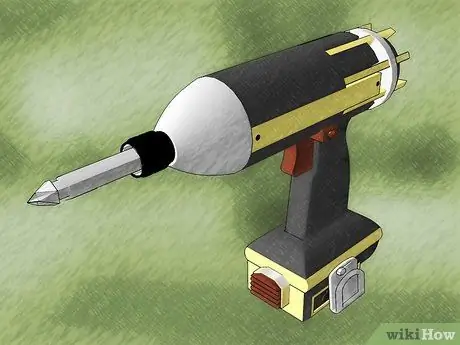
Step 1. Prepare the impact driver
An impact driver is a manual tool that pushes the screwdriver bit further into the screw using a weight and spring. These are great for sturdy builds, but can damage fragile electronics or other equipment. If you are worried that your item will be damaged, don't go for cheap models with stiff springs as these usually use a hammer to hit hard.
It is recommended that you do not use an impact wrench as excess force can damage the object the screw is attached to
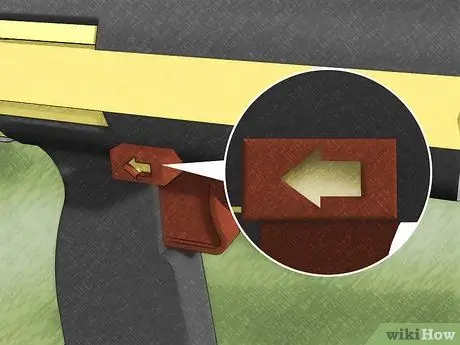
Step 2. Adjust the impact driver to loosen the screws
Some models have a switch, while in others, you adjust the direction of rotation by twisting the handle.
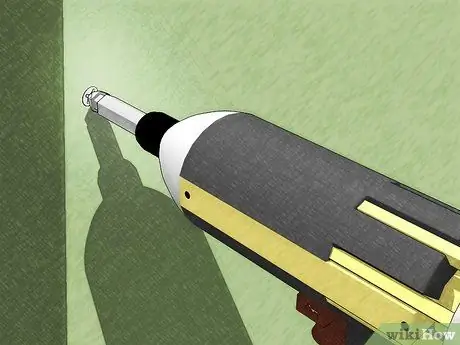
Step 3. Hold the driver firmly
Install a snugly sized drill bit on the end of your driver. Place it on the screw and hold the driver at a 90º angle. Hold the driver at its center point and keep your hands away from the end of the driver.
The bits that come with the impact driver are usually very hard which makes this process easier
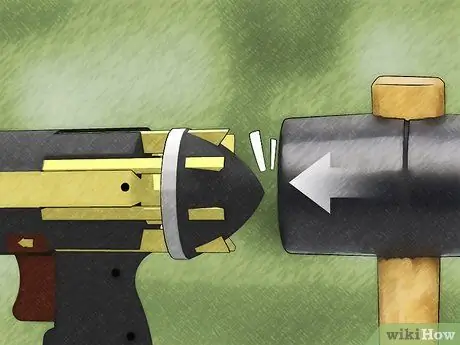
Step 4. Hit the ends with a hammer
Tap the tip of the driver sharply with a heavy hammer. Use a rubber mallet so as not to scratch the driver.
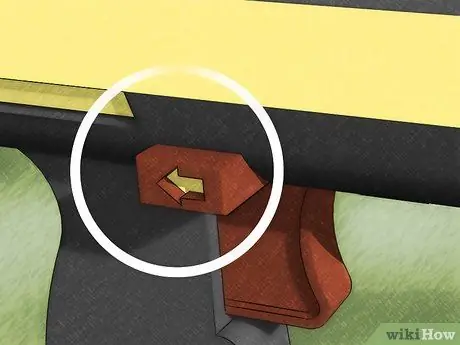
Step 5. Check the driver direction
Some impact drivers change position after each stroke. Set it back to “loosen” if necessary.
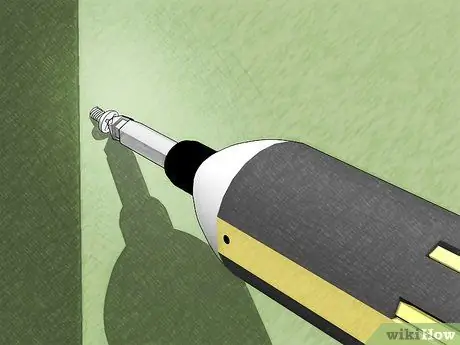
Step 6. Repeat until the screws are loose
Once the screw is loose, use a regular screwdriver to remove the screw from the hole.
Method 3 of 4: Using the Screw Pickup Tool
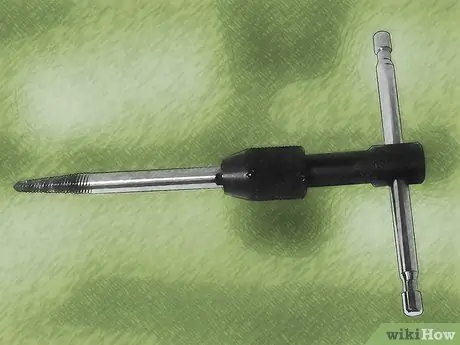
Step 1. Prepare the screw removal tool
If the screw heads are worn but are still firmly attached, purchase a screw extractor. Basically, this tool is a screwdriver bit made of extra-hard metal, and the tip has a reverse groove. This is one of the most consistent ways to remove a screw, although it should still be done with care. If this tool breaks the screw, you will need professional help to remove the screw. To reduce the chance of the screw breaking, choose a pick-up tool that is no more than 75% of the screw shaft diameter (not the head).
For Torx screws or socket caps with exposed cylindrical bodies, use a multi-spline extractor tool. This tool is attached to the screw head, and then gripped with splines (teeth) on the inner surface of the screw. Instead of following the guide below, tap on multi-spline extractor. gently until it snaps into place, then turn it with a socket wrench
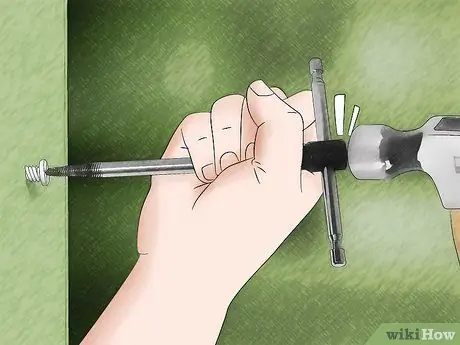
Step 2. Make a hole in the center of the screw head
Place the center punch exactly in the center of the screw head. Hit the base of the center pin with a hammer to make a hole, which the drill will then drill into.
Wear eye protection to protect yourself from flying metal debris. You must always wear safety equipment while working
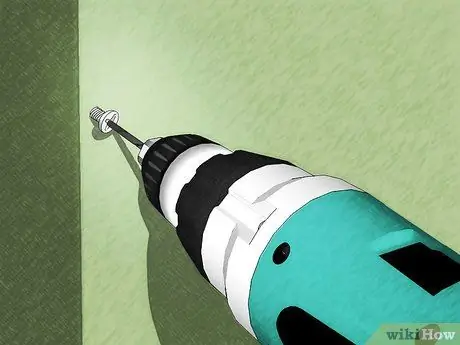
Step 3. Drill a hole in the screw head
Use a drill bit designed for hard metals. The drill bit size should be stamped somewhere on the screw take-up tool. Drill slowly and stabilize with a drill press, if possible. Start by making a hole 3-6 mm deep. Anything more than that can damage the screw. It helps to start with a small drill bit so that the larger bit has a place to grip the screw.
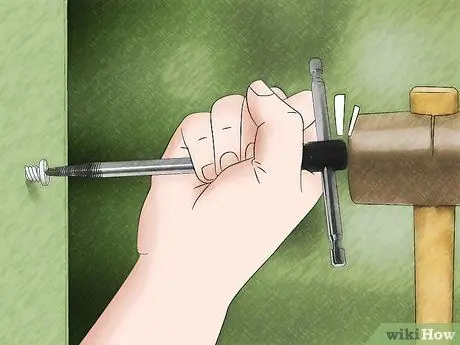
Step 4. Tap the take-up tool with a brass hammer
The extra hard metal in the screw take-up tool has a brittle structure that can be broken by an iron or steel hammer. Tap until the take-up tool grips the wall of the drilled hole firmly.
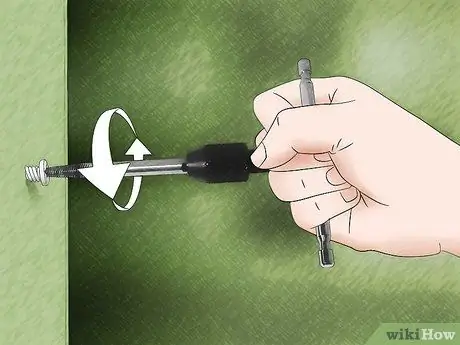
Step 5. Twist the take-up tool carefully
If your torque is too strong or uneven, the screw take-up tool could be damaged making things worse. The safest way to remove the pick-up tool and stuck screws is to tap the handle that fits snugly on the head of your screw-getter. The screw should be loose because it was drilled so it can be removed without much trouble.
Some screw-taking devices come with a nut attached to the screw-taking tool head. Grip the nut with two wrenches so that they are positioned like a line (forming a 180º angle) for a more even torque
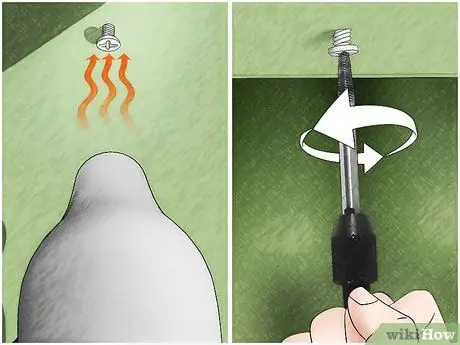
Step 6. Heat the screw if it won't come out
Remove the screw extractor if the stuck screw still remains, or you are concerned that the screw picker will be damaged. Heat the screw with a torch, then add a drop of paraffin or water to lubricate the groove. Once the screws have cooled, try using your screw picker again.
Try not to damage the object where the screw is stuck. Even when you're dealing with metal, it's best to use a heat gun or a propane torch. The torch on must be moved constantly so that any screw parts are not heated for more than one second at a time
Method 4 of 4: Additional Methods
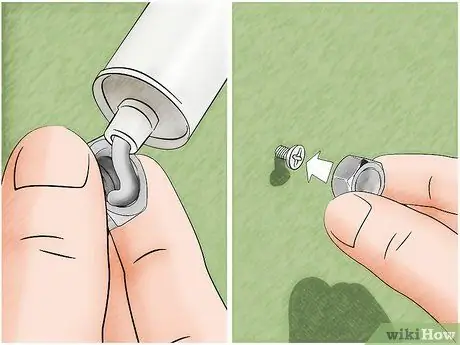
Step 1. Fix the nuts on the screws with epoxy glue
Look for a nut that fits snugly into the screw head. Glue the two together with a metal-adhesive epoxy glue, usually sold as a "weld binder." Wait for the epoxy glue to harden according to the directions on the label, then grip the nut with a wrench and turn it.
If you don't have a nut that fits properly, you can tape a smaller nut over the screw head. However, the focus obtained will not be optimal
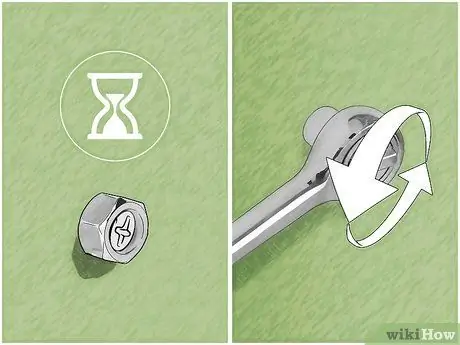
Step 2. Drill the screw heads
Breaking the screw usually reduces the stress on the screw rod making it easier to remove. However, if this method doesn't work, you can't try another method. Choose a drill bit slightly larger than the screw rod so that the screw head breaks completely when drilled. Start by using a center pin to make a hole exactly in the center of the screw, and carefully drill straight into the center of the screw. Once the screw head is completely broken, grip the screw rod with pliers and turn it counterclockwise until it comes off.
If the screw heads are not level, sand or file with a Dremel and a sharpened stone drill bit. Use a center pin and drill once the screw has a workable flat surface
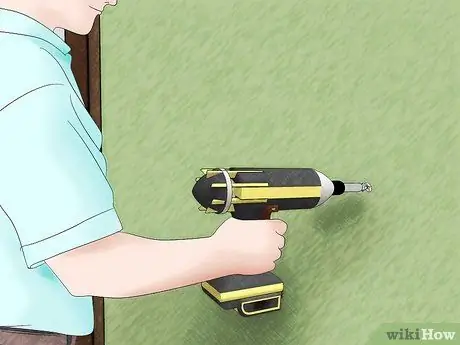
Step 3. Use the services of a professional
If all else fails, contact a carpenter to remove the screws using an electric discharge machining (EDM). This is probably your best option if you accidentally break a screw while using a screw extractor.
Tips
- If you can access the back of the object the screw is on, see if there is a screw rod sticking out there. If there are, grip the ends with pliers or a wrench and twist from the bottom.
- Make sure you turn the screw in the right direction. Your screw groove may be reversed and will need to be turned clockwise.
-
There are several ways to repair screw holes:
- Install the tap in the larger hole. To make the tap stick more firmly, apply Loctite superglue to the hole and attach the heli-coil insert.
- Install the larger screw into the screw hole.
- Use nuts and bolts. If the hole you want to close is metal, you can glue the bolts to the metal to create a fixed, grooved mount.