There is more to be done in concrete than simply pouring the concrete and then waiting for it to harden. Here's what you need to know to shape and smooth new concrete for an attractive and durable surface. Unless otherwise stated, do this quickly so you can finish everything before the concrete dries, especially on hot days.
Step
Part 1 of 3: Starting Leveling
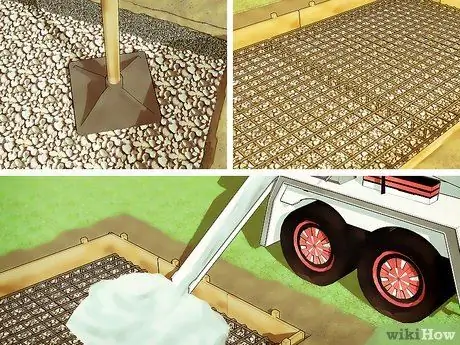
Step 1. Pour the concrete
If you're not used to pouring concrete, follow the instructions to make sure you're doing it right. Get ready to take the next step as soon as you pour it.
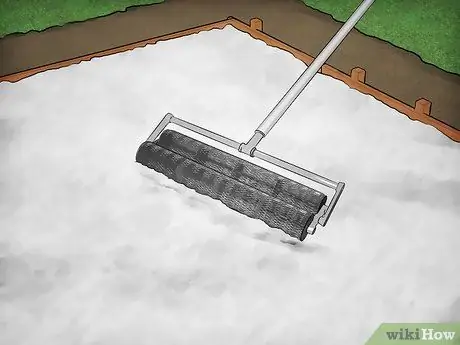
Step 2. Compress concrete only when needed
Many modern concrete mixes do not need to be compacted or "compacted" before coating. Compacting this type of concrete can weaken the slab. For more details, ask the experts about this.
If you decide to compact the concrete, simply press the concrete using a variety of compacting tools (manuals, rolls, etc.)
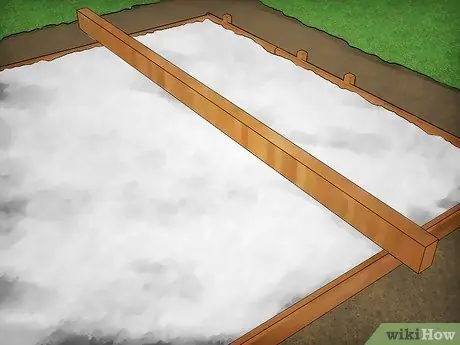
Step 3. Lay a 2x4 log across the concrete
Find the straightest 2x4 wood available and place it on the barrier that holds the concrete, or concrete "mold" in place. This wood must be at least 30 cm longer than the mold in all directions. This object is called a screed board.
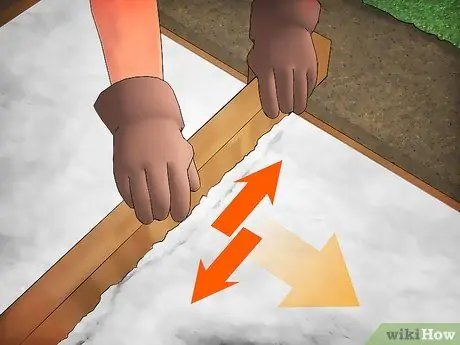
Step 4. Use the 2x4 lumber to level the concrete
Using the technique described below, move the 2x4 lumber down to remove excess concrete.
- Use a sawing motion to pull and push the wood across the concrete as you move it along the concrete mold. This sawing motion helps prevent tearing when leveling the surface.
- Tilt the leading edge slightly away from the direction of movement to create a thin cut edge where the screed board meets the concrete.
- Always keep at least 2.5 cm of concrete protrusion in front of the edge. This is to fill holes in the concrete surface.
- Pour and level gently for larger concrete projects.
- At the end of the slab, push the excess concrete into the side of the mold for easy removal with the tool later.
Part 2 of 3: Overlaying, Stage One
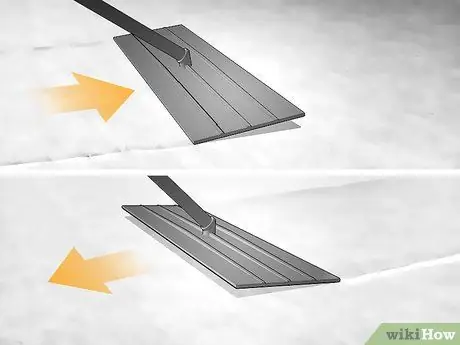
Step 1. Immediately level and prepare further using a bull float
The press board is a long-handled device used to flatten wrinkles and small holes, and to further adhere the particle mix to the concrete, allowing a smoother "cream" consistency to surface for better results.
- Move the pressure board back and forth across the plate, perpendicular to the direction you are moving the level board. (In other words, move the pressure board between the two 2x4 wood-based molds.)
- Lift the leading edge slightly to create a smaller cutting edge of the joint, lifting the tool in front of you when pushing and away from you while pulling. Do not exaggerate; the edge of the tool must remain parallel to the concrete.
- Complete this process before the "water seepage" leaks onto the concrete surface.
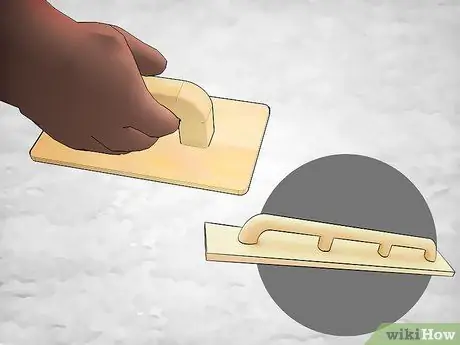
Step 2. Use an alternative tool (optional)
Darby's brand tools are short tools that work the same as a pressure board for smaller projects. "Power float" or "Helicopter" is a machine tool used on large projects.
- Move Darby back and forth in an overlapping arc motion until the entire surface is covered twice.
- The electric power float must be carefully lifted by two people onto the plate, but only one person will operate it. It takes a little practice to work well, so stay near the center of the slab as you learn to avoid damaging the edges of the concrete.
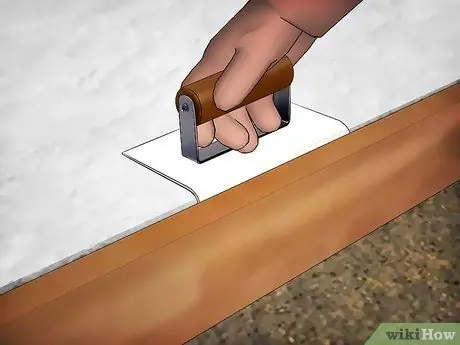
Step 3. Smooth out the corners using the smaller tool
Use the edging tool designed to create even edges and corners next to the shape, instead of the larger, less accurate pressure board or Darby. This will make the edges more durable and improve the appearance of the concrete.
- Use a back and forth motion in an area of 0, 3-0, 6 meters before moving on to the next area. Just like the previous tool, lift the leading edge of the tool.
- Do not press too deep into the concrete; this can create a trail that is difficult to cover.
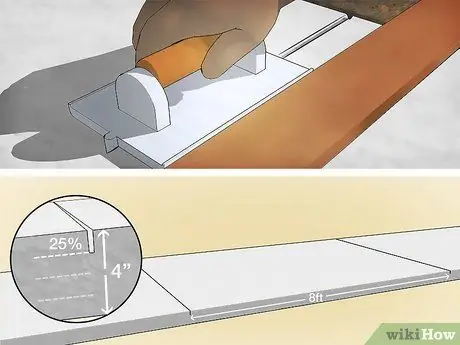
Step 4. Cut grooves in the concrete
These are called control joints which direct the inevitable cracks in the concrete in such a way that they have minimal effect on the appearance and functionality of the concrete. These joints shall be cut 25% of the length through the depth of the concrete.
- The distance between the joints should not exceed 24 times the plate thickness. Calculate its size by doubling the thickness of the plate in cm and using its measurement in meters. For example, a 10 cm thick slab must have joints not exceeding 2.4 meters apart.
- Every corner in the slab and every corner that touches the building or footing must have a control joint extending from there, as this is a common crack point.
- Use a flat rake or snap line to finely mark the joints before cutting. Keep the tool straight as you cut.
- You can also use the grooving tool. If the concrete is starting to dry and crack, use a dry-cut saw that can cut to the desired depth. For extra large projects, use a long-handled marking tool.
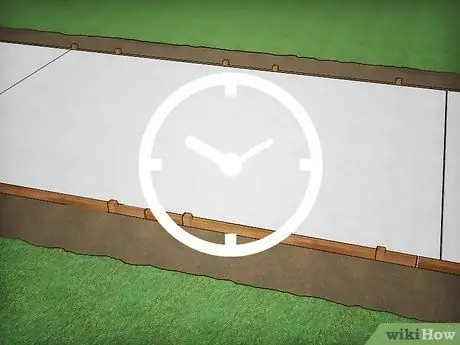
Step 5. Wait until the concrete is partially dry
It takes experience to learn the correct timing for concrete, as the speed at which concrete dries depends on many factors, such as mix characteristics, local temperature and humidity. Here are the basic details:
- As the concrete hardens, excess "water seepage" will rise to the surface. Wait until this water evaporates and the wet glow of the concrete has begun to disappear.
- If the concrete is still moderately wet and forming wrinkles when you proceed to the next step, wait a little longer.
- If the concrete is too hard and dry to cover, add water to the surface of the concrete. This is a last resort as it will weaken the plate and form a crust.
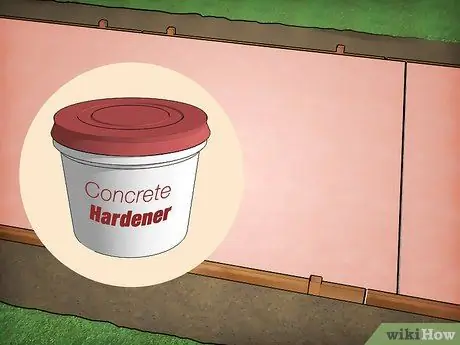
Step 6. Apply color hardener (optional)
If you are tinting concrete using a powder that adds color to the topcoat, apply the amount specified on the label while the wet light on the concrete is still very visible. It still needs to dry a bit before you move on to the next stage.
Use only on horizontal surfaces and with proper safety equipment to avoid inhalation
Part 3 of 3: Overlaying, Stage Two
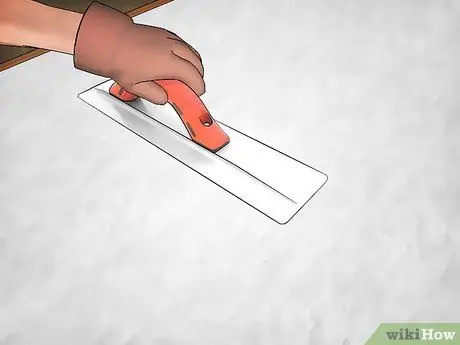
Step 1. Smooth and compact the surface once again with a hand float
This is the final smoothing step, creating a more consistent "cream" to the surface for a more even and longer-lasting coating. Different suppressants will have different effects:
- Magnesium float (Magnesium float) is very popular among professionals, because it is lightweight and excellent at opening the pores of the concrete for evaporation.
- Aluminum float (Aluminum float) is very similar to magnesium, but slightly heavier and stronger (and a little more difficult to handle).
- Wood presses (Wooden float, redwood or hardwood) are inexpensive but wear out quickly. This board creates a rough, fuzzy surface which is useful for very stiff concrete, or if you are using a colored hardener (which must be mixed with a abrasive).
- Laminated-canvas resin float presses do the same thing as wood, but are much more durable (and expensive).
- Just as before, lift the leading edge and make shallow flat motions across the surface.
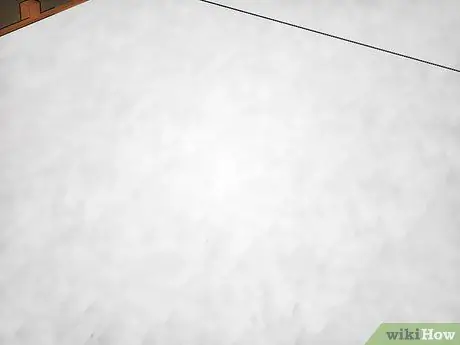
Step 2. Consider using a trowel
Many people skip the trowel if they want to use a steel broom, because the trowel yields little profit. Using trowels without a steel broom will result in a very slippery surface (unsafe for surfaces to be exposed to wet) and can cause fine cracks, called "crazing".
- Use the magnesium trowel the same as the coating tool you previously used. You can make the coating very smooth by going through the slab two or three times, waiting for the concrete to dry a bit between rolling, then lifting the leading edge a little higher.
- Steel trowels can also be used, but the wrong timing can cause the steel to trap water in the concrete and damage it.
- Using a trowel that is too deep or on a concrete mix with trapped air in it can release any trapped air bubbles and prevent the concrete from setting properly.
- Larger trowels (or other long-handled upholstery) are sometimes called "fresnos". This tool is useful for reaching the center of a large plate. Or, use a hand trowel but kneel on the plank when you need to be on the plate so as not to leave deep traces.
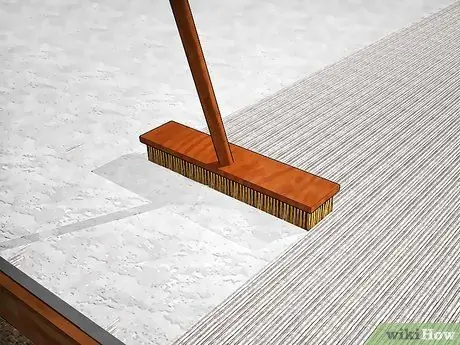
Step 3. Try using a steel broom
Most people use a steel broom to create a non-slip surface. You can do this with or without the previous layer of trowel.
- Use a medium stiff broom or a harder (wide square) broom. The broom's bristles must be stiff enough to leave marks, and the concrete must be soft enough to be malleable but hard enough to hold on to (not sink back completely).
- Dip the broom in a bucket of water, then shake off the excess (not into the concrete).
- Gently pull the steel broom over the concrete by sections. Do it on top of the previous section to make sure all sections are exposed.
- If the surface is to be dried, make grooves in the direction of the liquid flow.
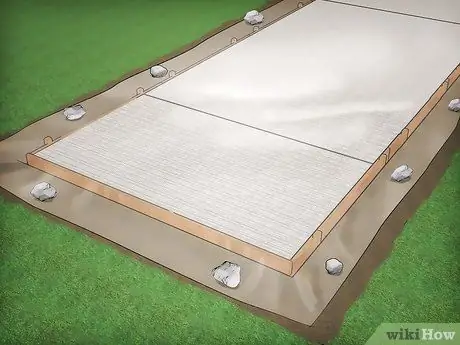
Step 4. Dry the concrete
The final drying process of the concrete takes several weeks, and if it "drys" at the correct rate will minimize the chance of damage to the concrete.
- The simplest way is to wet the concrete surface and cover it with a plastic sheeting. Put weight on the edge of the tarp.
- There are many other ways to keep concrete wet, but these tend to require more water or maintenance than plastic.
- Concrete drying chemicals are often used for professional work. Due to the variety of types, ask someone who knows about concrete mixes for advice on dryers.
- Start drying as soon as possible. After starting, the concrete should not be stepped on for 24 hours, passed by light vehicles such as bicycles for 1 week, and cars for 2 weeks. Complete drying takes at least 30 days, even longer for corners and edges.
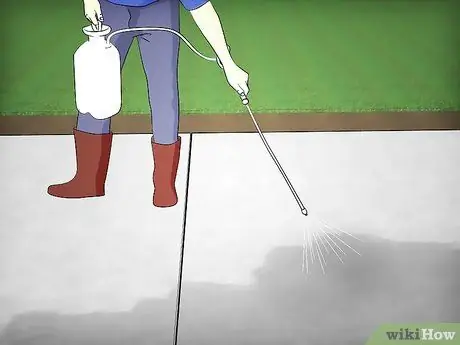
Step 5. Seal the concrete
After the concrete has dried for at least a month, use a concrete sealer to make it resistant to liquid damage and easy to clean..
- Clean the platen well before adding the sealant.
- Apply a thin layer to avoid puddles. If needed, wait a few hours (or as instructed on the label), then apply a second coat perpendicular to the first.
- Allow the sealing material to dry completely before the concrete can be stepped on or overwritten with anything. Wait three days before the vehicle can pass.