There are many different types of plastics and types of glue available. Choosing the wrong combination can result in a weak bond, and in rare cases can damage the object you are repairing. Read on to learn how to choose the right glue, then follow these steps so that the plastic can optimally bond permanently to other objects. If you're gluing plastic tubing, skip straight to that section. There are a few pointers for choosing the right adhesive out there.
Step
Method 1 of 3: Choosing Glue
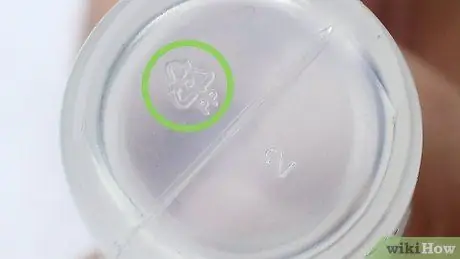
Step 1. Look for a recycling symbol
Each type of plastic requires a different glue. The easiest way to identify the type of plastic is to look for the recycling symbol on the plastic itself, label, or packaging. This symbol is a triangle consisting of three arrows, and contains numbers, letters or both inside or below the triangle.
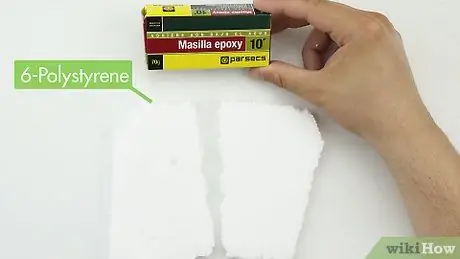
Step 2. Find out how to glue the plastic marked with the number 6
Recycling symbol containing a number
Step 6. or PS indicates the type of plastic "polystyrene". This type adheres best using poly cement (also called plastic cement), or a special brand of plastic glue such as Loctite Epoxy Plastic Binder or Super Glue Plastic Fusion. Other adhesives that can be used include cyanocrylate (also called "instant glue" or "cyano") or epoxies.
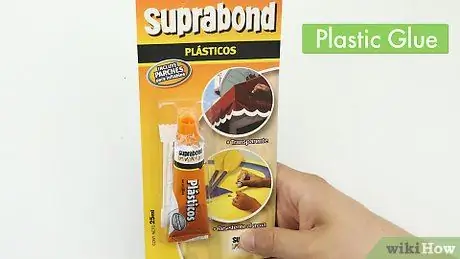
Step 3. Choose a special glue for plastics marked 2, 4, or 5
If the plastic is labeled
Step 2
Step 4
Step 5., HDPE, LDPE, PP, or UMHW, the type of plastic is "polyethylene" or "polypropylene". These plastics are much more difficult to glue, and you should look for certain products that list this type of plastic on the label, such as Loctite Plastics Bonding System or Scotch Weld DP 8010.
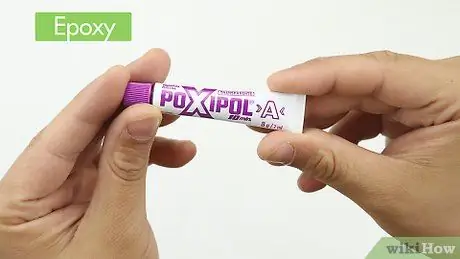
Step 4. Make the right choice for the plastics marked 7 or 9
Mixed category marked
Step 7. or type ABS marked
Step 9. can indicate the type of plastic gum, with many possible letters indicating the subtype. You're best off gluing it with epoxy or cyanocrylate.
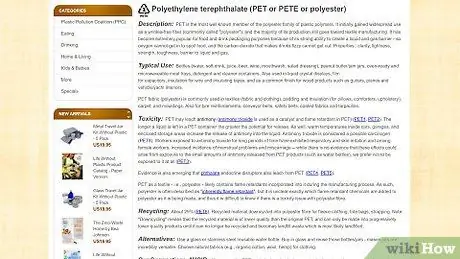
Step 5. Try to identify the type of plastic in other ways
If there's no recycling system, you'll have to guess what type of plastic it is before choosing the glue. Here's a guide to help you complete this task:
- Lego toys are made of a type of plastic called "ABS", and are best glued using epoxy cement. ABS solvent cement can also be used, but it can change the shape of the surface of the object.
- Imitation glass, cheap toys, CD cases, and similar fragile items and often clear plastic are usually of the "polystyrene" type and can be glued using a number of adhesives. For best results, use poly cement or glue that says it will bond to plastic.
- The hard, dense plastic glue found in bottles, buckets, crates, and food containers uses a special product that claims to bond "polyethylene" and "polypropylene". This type of plastic is impossible to glue in most normal ways, so don't assume a product labeled "for plastics" can be used, unless it specifically mentions "polyethylene" and "polypropylene".

Step 6. Do further research on gluing plastic to other materials
If you are gluing plastic to wood, metal, glass, or even another type of plastic, do more research. If you can't find the answer online or ask an experienced repairman, go to a hardware store and look at each brand of adhesive you've decided to use following the steps above. The packaging will tell you what materials can be glued to the plastic.
- Visit This to That for more advice on which glue to use for each ingredient combination. The suggestions are helpful for common plastic types, especially polystyrene.
- If you're not sure which one to use, test an adhesive with scrap material made of the same type of plastic, or at an inconspicuous corner of the object to be glued.
Method 2 of 3: Gluing Plastic
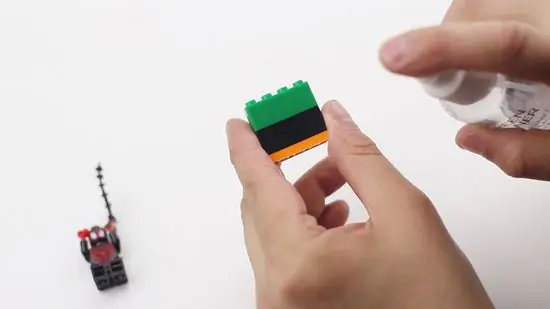
Step 1. Remove grease from plastic
Wash with soap, use a special plastic cleaner, or soak the plastic in isopropyl alcohol to clean it. Dry thoroughly.
Avoid touching the parts with bare hands afterwards, to minimize oil residue
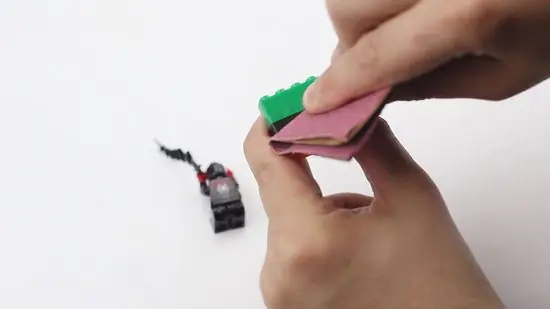
Step 2. Sand the surface to be glued
Lightly sand the plastic with 120-200 sandpaper to create a rough surface so that the glue can be attached. Steel wool or an emery cloth can also work, but remember that they only need to be scrubbed for a while.
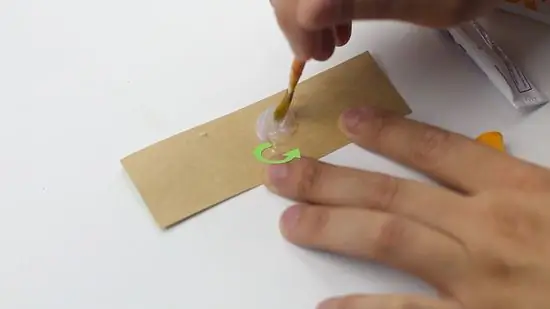
Step 3. Mix the two components of the glue together if necessary
The two-part "epoxy" must mix the two ingredients to activate the adhesive. Read the instructions on the container carefully, because there are many types of epoxy, and each requires two ingredients in a certain ratio. Some epoxies can be used for several hours after mixing, while others should be applied within a few minutes.
See the Selecting Glue section to learn which type of glue to use. You can skip this section if you are not using double-sided adhesive
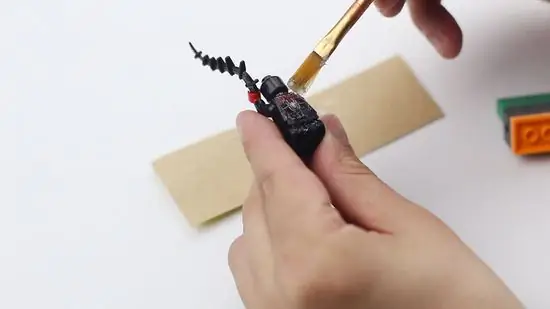
Step 4. Apply glue to both surfaces
Use a small brush to apply a flat layer of adhesive to both surfaces to be bonded. For small pieces, such as broken pieces of plastic, use the tip of the needle instead.
If you are using solvent cement (not a poly cement or plastic cement), pinch the two pieces together first, then use an applicator bottle to place a thin line of solvent cement along the edge between the pieces to be smeared between them. If you are using it on plastic pipes, see Gluing Plastic Pipes instead
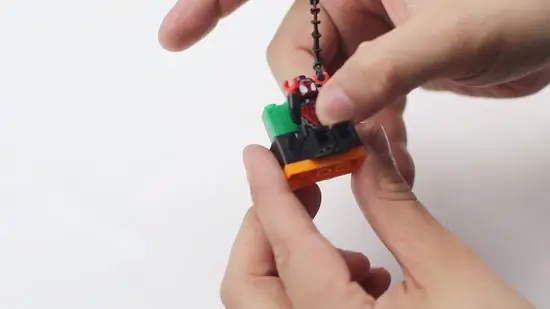
Step 5. Press the two pieces gently together
Press the two pieces together to place them in position and remove any air bubbles. Do not push very hard so that the adhesive does not seep out of the joint. If this happens, remove the excess unless you are using acrylic cement which must be allowed to evaporate.
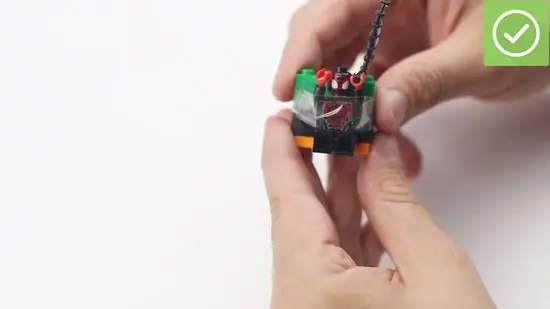
Step 6. Keep the two pieces from shifting
Use clamps, vise, tape, or a rubber band to hold it in place. Read the instructions on the adhesive case to find out how long to hold it in place. Depending on the type and brand of adhesive, the bond may take anywhere from a few minutes to 24 hours to set.
Many plastic adhesives continue to "groom," or develop a stronger bond for days or even weeks after application. Avoid applying pressure and heat to the glued piece for at least 24 hours after applying, even if the bond looks strong
Method 3 of 3: Gluing Plastic Pipes
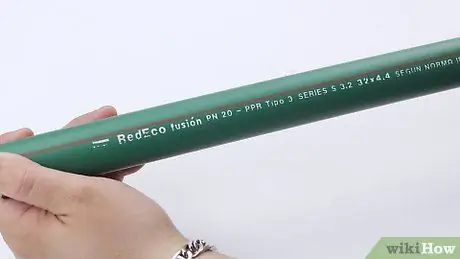
Step 1. Get to know your pipe
There are three types of plastic tubing, and each only works with certain glues. The easiest way to identify it is to look for the world recycling symbol, which is a triangle formed from three arrows with numbers or letters to indicate the type of plastic. Learn how to use this and other methods before choosing glue.
-
PVC pipe is commonly used in residential plumbing, although it should not be used for pipelines or other high temperature applications. This pipe is usually white, or gray if used for electrical or industrial purposes. The recycling symbol is
Step 6. or PVC.
- CPVC pipe is a PVC pipe intended to withstand hotter temperatures. These pipes share the same recycling symbol (6 or PVC), but are usually brown or cream colored.
-
ABS is an older and more flexible type of plastic pipe, usually black in color. This pipe is not suitable for drinking water purposes and in some areas it is illegal to use it as a plumbing pipe. The recycling symbol is
Step 9., ABS, or 7 (other).
- PEX pipe is the newest type of plastic pipe, available in many colors. This pipe is non-recyclable, cannot be glued, and must be attached using a mechanical fixing tool.
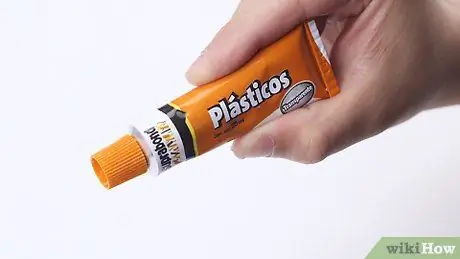
Step 2. Choose an adhesive
The material that binds plastic pipes is called solvent cement. Find the specific solvent cement you need once you identify the type of plastic.
- ABS solvent cement will join two ABS pipes. PVC solvent cement and CPVC solvent cement will also join the two types of pipes.
- Transition solvent cement is used to join ABS pipe to PVC pipe. Its distinctive green color makes it easy to spot.
- If you can't find a more specialized product, general solvent cements can be used for a combination of PVC, CPVC, and ABS. You still have to identify your pipe first to make sure the pipe type is not PEX, which should be installed and not glued.
- Read the label of the solvent cement to make sure it will work for the size of pipe you are using.
- To attach a plastic pipe to a metal pipe, you will need a special adhesive and a specific metal combination, or a mechanical fixing tool. Ask a plumber or hardware store about this.
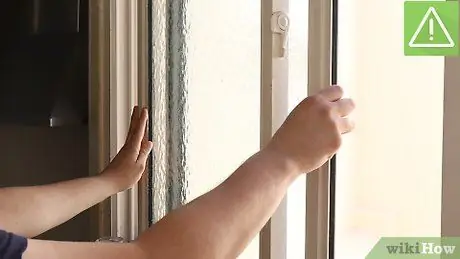
Step 3. Follow safe ventilation practices
Base coat cements and solvents give off harmful fumes when used. Work in a well-ventilated area (windows wide open, outdoors, etc.), or wear a respirator that blocks organic vapors.
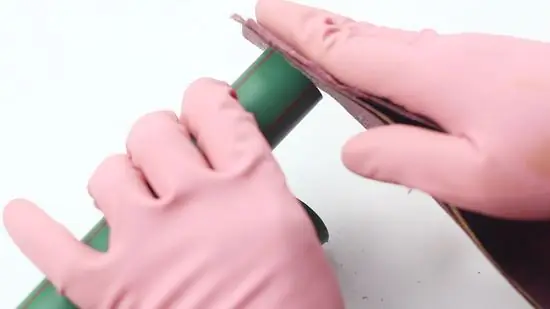
Step 4. Smooth the inside of the pipe if the pipe is sawed
Roll type 80 sandpaper into the tube and sand the inside and outside of the pipe to be attached. The goal is to remove uneven bits and "thorns" created during sawing, which can catch debris and cause blockages.
- Smooth the sandpaper roll over the tube to match its shape before scrubbing.
- If no sandpaper is available, use a grinder or remove any visible burrs with a pocket knife.
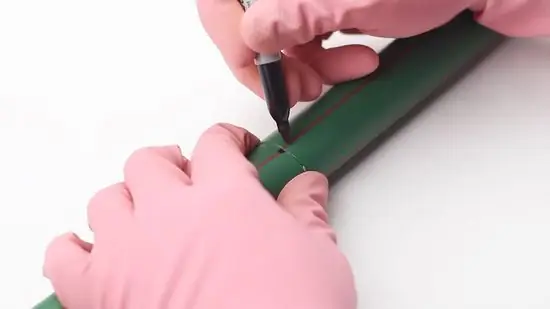
Step 5. Mark the internode rows before gluing the curved pieces
You don't have much time to arrange the pipes once you've applied the solvent cement, so first install both pieces dry. Rotate to the lines you need and use a permanent marker to draw lines between them.
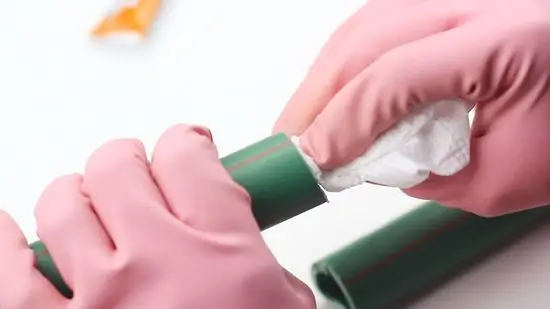
Step 6. Apply primer before gluing
Of the three types of plastic pipe, PVC is the only material that should be primed, but CPVC also adheres better after being primed. Wipe enough PVC primer or CPVC primer on the outside of the pipe and inside the pipe fitting to be attached. Let dry for 10 seconds before continuing.
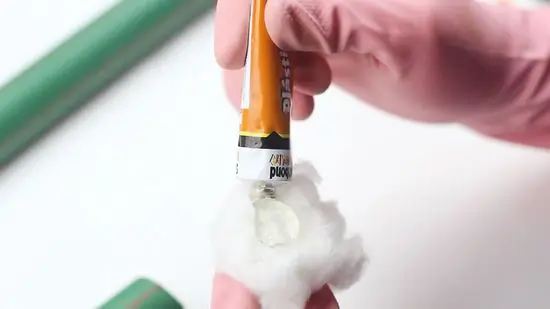
Step 7. Work quickly and regularly to apply solvent cement
Put on gloves, use a brush or cotton ball to clean a flat layer of solvent cement on the outside of the pipe segment and the inside of the pipe fitting. Just apply a thin, flat layer to the mounting cavity, otherwise excess can be pushed into the water pipe and create a blockage.

Step 8. Immediately connect the pipes a quarter turn of the desired row, then twist and hold
After applying the solvent cement, glue the pipes a quarter turn from the line markings you made, then twist the tubes until the markings align. If you don't have to make any line markings, just stick it and give it a quarter turn. Hold for about fifteen seconds for the cement to grip.
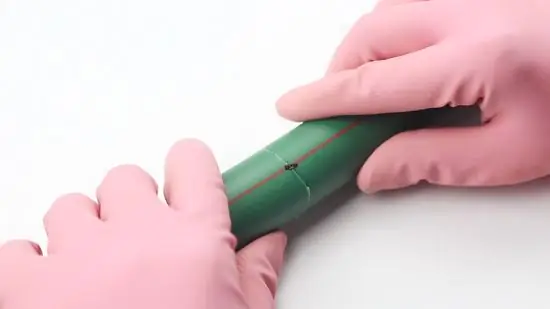
Step 9. Correct the incorrect length by sawing the space for the new segment
Adhesion may shrink slightly as the solvent cement dries. If the last cut is too short, cut the saw apart and then lengthen it by gluing the new fixing over it. If it's too long, remove one section of the pipe completely by sawing it, then connect the two remaining ends with a new fitting.
Tips
- Silicone putty is useless on plastic, except to enhance the appearance. This putty is not a structurally strong solution.
- If you drip acrylic cement on a surface you don't want to glue, don't wipe. Let the acrylic cement evaporate.