Aluminum is quite difficult to put together without a special soldering tool. You will need to find a special solder or special alloy to use on aluminum, or to join aluminum to a specific metal that you use in your project. Once you've obtained this solder online or from a specialty supply store, the challenge that remains is how you can work quickly to bond the aluminum as soon as the oxidation layer has peeled off the surface.
Step
Part 1 of 2: Getting Started

Step 1. Identify the suspected presence of a mixture if possible
Pure aluminum can be soldered, although it is difficult. Many aluminum objects are actually aluminum alloys. Most can be soldered in a similar way, but some are very difficult to work with and may require the assistance of a professional welder. If aluminum alloys are marked with letters or numbers, see if there are any special requirements. Unfortunately, unmarked aluminum alloys are difficult to identify, and the help of a professional is urgently needed if this is part of your business. You can do it yourself and test your luck.
If you are bonding aluminum to another metal, the resistance of the aluminum is usually the limiting factor, so specific identification of the other alloy may not be necessary. Note that some combinations such as aluminum and iron are very difficult to work with and may require special methods other than soldering
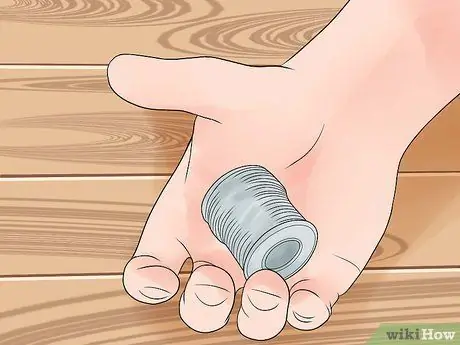
Step 2. Choose a low temperature solder
Aluminum can melt at the low temperature of 660ºC, which, combined with its heat-absorption properties, makes it even more difficult to solder. You'll need a special solder with a significant melting point, which you can get online. Usually, a material made of a mixture of aluminum, silicon, and/or zinc is used for this purpose, but check the label again to make sure the material is suitable for the connection you are going to make, such as aluminum to aluminum or aluminum to copper.
- Technically, metal joints will melt above 450ºC using "copper" instead of solder. In practice, it is usually sold in solder, with a similar process. The use of copper will create a stronger connection, but the soldering process is recommended for use on materials with electrical circuits or other soft materials.
- As much as possible avoid solder containing lead.
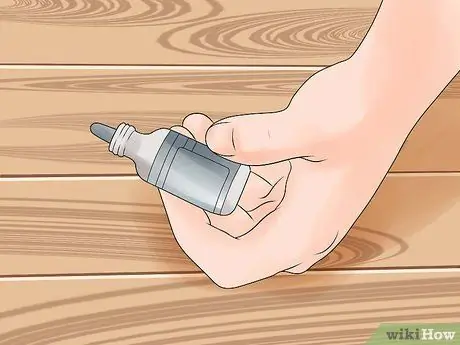
Step 3. Take a flux
As with solder, the flux used must be specific to the aluminum or combination of metals you are joining. The easiest option is to buy flux from the same place where you bought the specific melting point solder, as they will be used together. The best temperature at the flux should be the same as the melting point of your solder. Choose copper flux if the solder you choose melts above 450ºC.
Some copper fluxes are not made for use in thin aluminum sheets or wires. Look for "dipped copper" fluxes for this
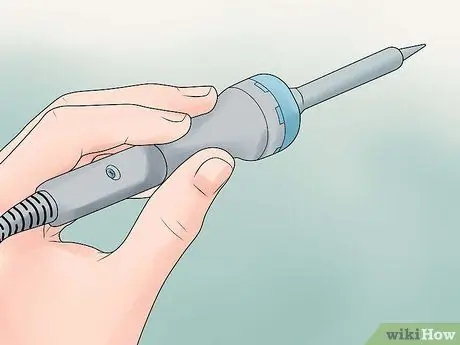
Step 4. Choose a heat source
You can use a soldering iron to hold the aluminum wires together, but for other materials you will need to use a torch. Usually, a low temperature torch can be used, with the flame tip reaching 315-425ºC.
If using a torch is not possible in your workplace, try a 150-watt soldering iron
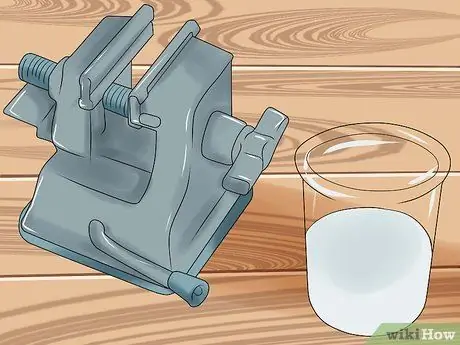
Step 5. Collect optional materials
You need clamps when joining more than one sheet of metal, not when you are making minor fixes on one object. An acid solution, or a special agent for cleaning oxidation after soldering, can also be used. Some resin based fluxes must be cleaned with acetone.
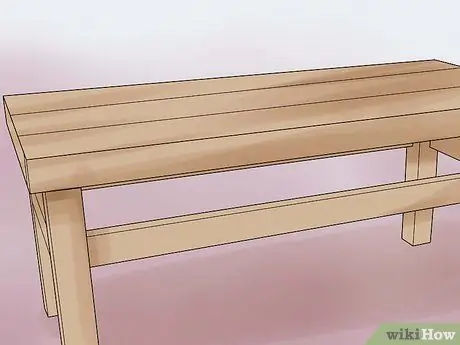
Step 6. Set up a safe work area
Protect yourself from toxins by wearing an air mask and working in a room with good air circulation. A face mask or dust goggles is highly recommended, as are thick leather gloves and non-synthetic clothing. Place a fire extinguisher near you and work on a non-combustible surface.
Part 2 of 2: Bonding Aluminum
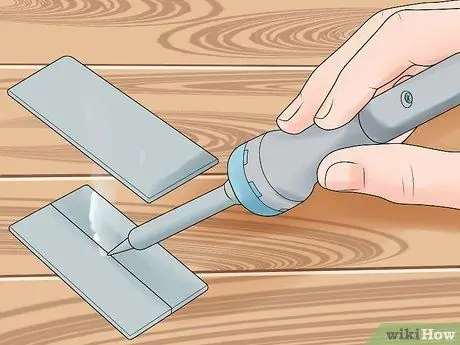
Step 1. Perform pre-soldering on any parts that are difficult to join (optional)
Large joints or difficult combinations such as aluminum and iron will be easier to put together when they are preheated. Follow the instructions below and apply to each piece you want to join, then repeat with the rest of the material to be joined.
Skip this step if you are using solder to repair a crack or hole in an object
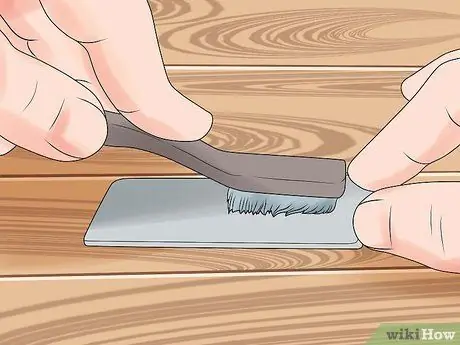
Step 2. Clean the aluminum with an anti-rust brush
Aluminum forms aluminum oxide rapidly when exposed to air, and this thin layer of oxidation does not stick together. Scrub thoroughly with a stainless steel brush, but read the instructions below first. Be prepared to clean, flux, and solder quickly so the oxide doesn't have time to build up again.
Old aluminum with heavy oxidation or a rusted surface may need to be sanded or honed, or wiped with isopropyl alcohol and acetone
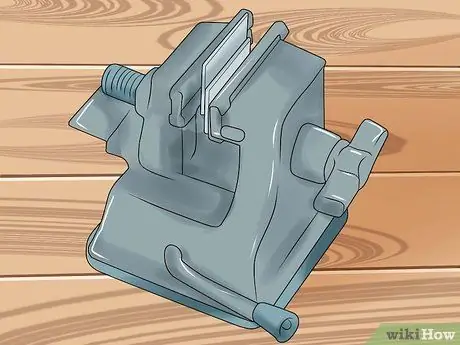
Step 3. Clamp the metal bases together
If you are joining two pieces of object instead of one, pinch the two pieces of metal together in the position you want. There must be some distance between them for solder to be used, but keep this distance no more than 1/25 (1mm) or less.
- If the pieces don't connect well, you'll need to sand or sharpen the piece first.
- Since the aluminum is not allowed to oxidize again, you may need to loosely clamp the two pieces of metal together, clean them while they are clamping, and then tighten the clasps.
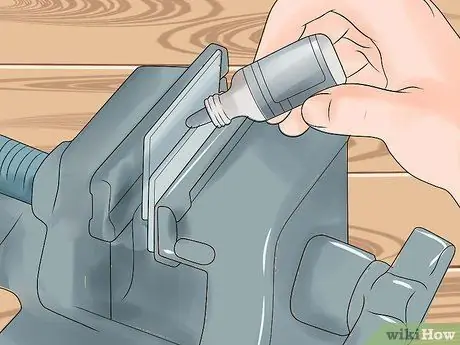
Step 4. Use flux
Immediately after cleaning the metal, apply flux to the area you wish to join using a solder joint or small metal utensil. This will prevent the oxidation process from occurring and place the solder along the desired area.
- If soldering wires, dip the wires in the flux liquid.
- If the flux you have is in powder form, follow the instructions for use on the package.
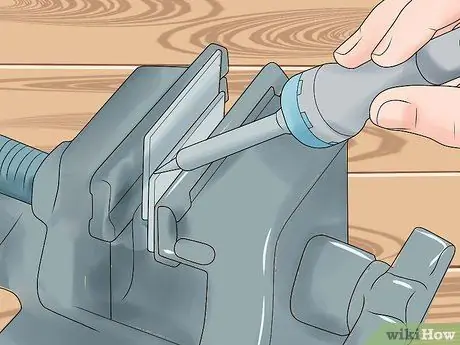
Step 5. Heat the metal
Use your torch or soldering iron to heat the metal object in the joint, starting with the bottom end of the joint. Applying direct flame to the area to be repaired will overheat the solder and flux. If you are using a torch, hold the tip of the torch at least 12 to 18 cm from the main metal. Move the heat source constantly, in small circular motions over the entire joint area.
- The soldering iron may take up to 10 minutes to heat up before it can be used.
- If the flux turns black, let the area cool down first, clean it, and try again.
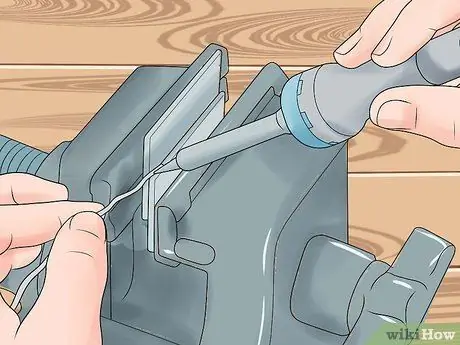
Step 6. Use a soldering iron
Most fluxes will bubble and turn slightly brown when they reach the appropriate temperature. Slide the connecting rod or soldering material onto the joint, proceeding to heat the area indirectly from the reverse side, or the adjacent surface. This will remove any gaps that previously existed, with constant, slow motion necessary to create a rusty finish. Making neat, strong joints should be practiced beforehand if you've never done this activity before.
If the solder does not bond to the aluminum, there may still be aluminum oxide forming on the surface, and must be cleaned immediately before re-soldering. This could also be due to your choosing the wrong type of solder, or the aluminum you are using may actually be an aluminum alloy that is difficult to join
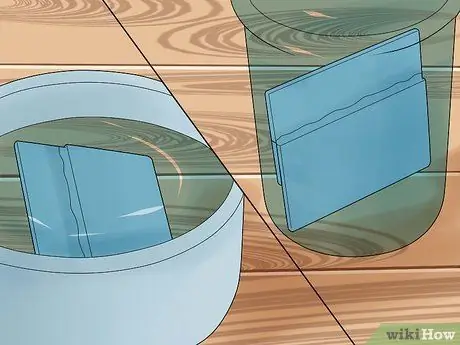
Step 7. Remove excess flux and oxidize
If you are using a liquid flux, the flux can be rinsed off with water once the metal has cooled. If you are using a resin-based flux, use acetone. “After” the flux has been removed, you may want to dip your work in an “acid solution” to remove any residual oxidation that may have been created by the high temperature.
Tips
- Aluminum absorbs heat well, which makes the area to be joined difficult to heat. If you can't solder it, try placing the aluminum in a cable holder or other cooler with a small surface, or using a hotter torch.
- Sometimes you need to heat the soldering tip with a fire to make the solder work more easily on the area to be repaired. Be careful when heating the rods, as overheating the rods will prevent the solder from sticking together.