Soldering is a common and effective way of joining metal components together. Read the steps below to learn about the two main types of soldering, and how you can do it at home.
Step
Method 1 of 3: Soldering Basics
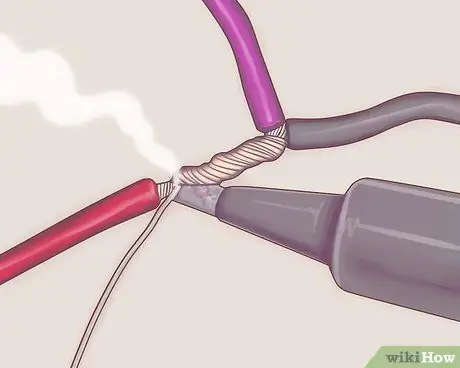
Step 1. Learn what soldering is
In general, soldering is the process of melting metal and bonding it to other metal components.
-
Soldering is different from welding. In welding, the components are melted together; In soldering, a softer metal with a lower melting point is used to hold it together.
Since soldering doesn't actually melt components, it's useful for more sensitive applications, such as electronics or plumbing work
-
The purpose of soldering is to join two components together. Solder can be thought of as a kind of “metal glue.” Solder can be used to fill gaps or glue pieces together, but it can't be used for more complicated purposes.
Since solder is metallic, it contains electricity, making it popular for attaching electrical components
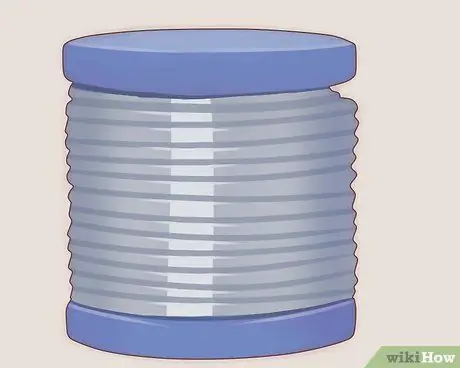
Step 2. Use solder to stick things together
Solder itself is the name of the actual material used in the soldering process. Historically, many solders contained lead or cadmium, but these two substances are now deprecated for health reasons.
- Solder is usually composed of two or more metals which are combined into a mixture. Silver, antimony, copper, lead, and zinc are common ingredients.
- Solder is soft and flexible. Solder is usually in the form of coils or coils that can be stretched and bent.
- Solder has a low melting point, and cools very quickly after it's melted. (176-260 degrees Celsius)
-
Solder may contain natural caulking or chemical acids. Metal solder encircles the core, like a tube.
The use of the solder core is as a liquefying agent, or purifier. This liquid prevents oxidation of the solder as it cools, resulting in a strong and pure finish
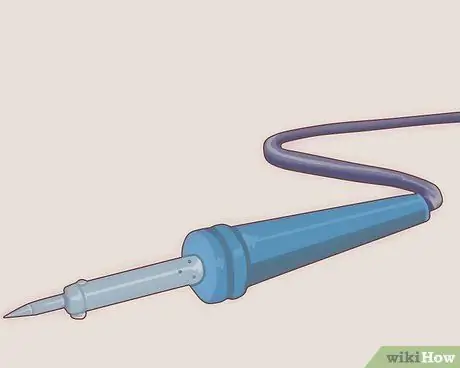
Step 3. Use a soldering iron to heat the solder
This tool has a variety of configurations, but is actually a straight tool with a heated tip to melt solder.
- Most of these tools will heat up at 426 to 482 degrees Celsius, so be careful when using them.
-
Soldering irons often stick to the coating or solder after use, which can oxidize and reduce the effectiveness of the iron for later use. To clean it, use a damp sponge before you turn it on, and wipe the tip of the iron against the sponge once the iron has warmed up.
A fresh coat of solder on the tip of this tool can actually provide more effective results. This process is called “tinning,” and is done by applying a small amount of fresh solder to melt evenly on the tip of the tool before use
- Better models of soldering irons have heat controllers that can be adjusted for different projects and solder types.
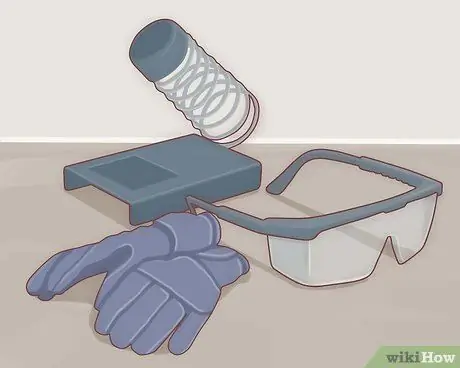
Step 4. Use other tools to help with soldering
Soldering isn't really that dangerous or difficult if you're careful. In order to solder efficiently and effectively, there are some tools that you must have at your disposal.
- Clamps or clamps to keep components in place while you solder them
- Thick gloves, to protect hands from the tip of the soldering iron
- Safety glasses, to avoid solder splashes in your eyes
- Solder mat to place the soldering iron on when idle
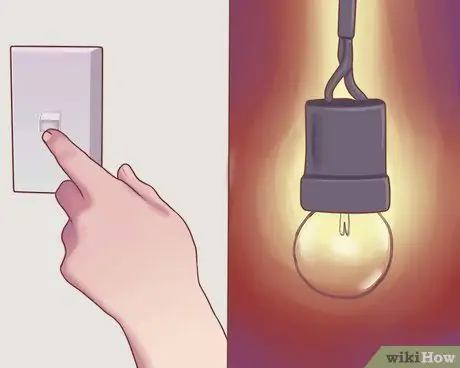
Step 5. Turn on the light
Make sure you can see everything clearly so your work will be accurate.
If you need to solder in a dark area, bring a bright light source (such as a multipurpose lamp)
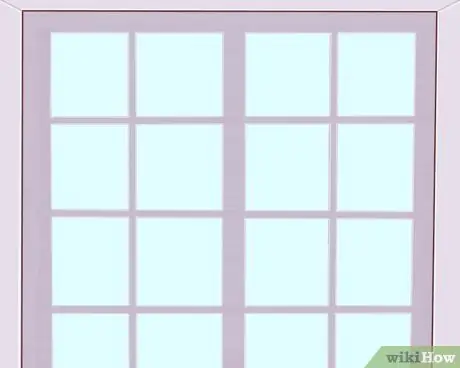
Step 6. Provide adequate ventilation
Even without the mixture, solder and its liquid can produce noxious fumes. Avoid inhaling rosin or metal fumes by opening windows, turning on fans, and doing whatever is necessary to keep the air fresh.
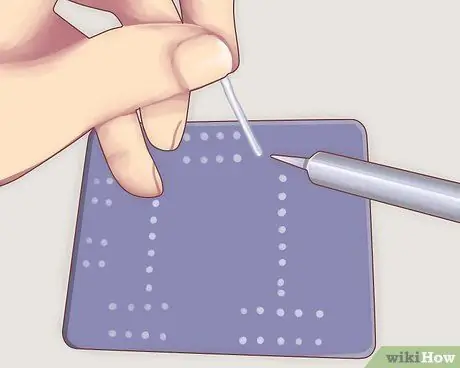
Step 7. Do not solder too long
Soldering is a quick process, and usually only takes a few minutes, but if you have to spend more than 15 or 20 minutes on a project, take a break and get some fresh air.
Method 2 of 3: Soldering Electronics
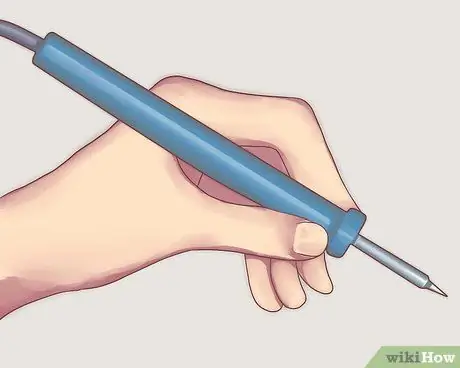
Step 1. Choose your soldering iron
Most electronic components are soldered in order to secure the components to the printed circuit board (PCB). Therefore, use an iron with a smaller tip. Consider using the minus end for everyday work, or the cone end for detailed soldering.
- Soldering irons don't have removable/replaceable tips, so buy the one that fits your needs. Fortunately, prices start from around Rp. 180,000, -, and a good quality iron can be obtained for about twice that.
- A typical soldering iron for electronics work will have a voltage of 40 watts with a temperature (or temperature setting) as high as 482 degrees Celsius. This will ensure that the iron is able to melt the electronic solder easily without damaging the existing component wires.
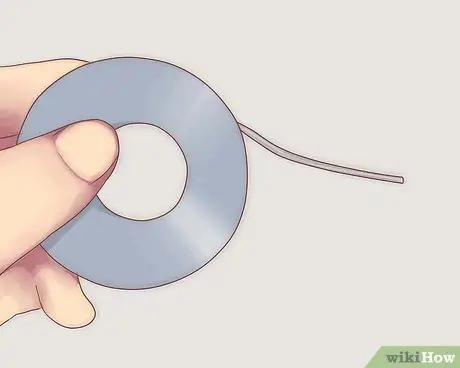
Step 2. Choose your soldering iron
Both solid wire solder or Rosin are available at local stores and online. Make sure the solder you choose will adhere to the material you are trying to solder. Solid wire solder may require a separate liquid to break off the oxide layer and allow the solder to adhere.
-
60/40 lead charcoal solder was once a standard tool for electronic work, however, due to the toxic levels it produces, it is now forgotten. Usually, silver and tin solders are used in today's times. Silver will slightly increase the melting point to 221 degrees Celsius and is more expensive, but helps the solder to stick more tightly.
The number in the solder description represents the percentage of elements in the solder mixture. ((60Sn/40Pb = 60% tin and 40% charcoal)
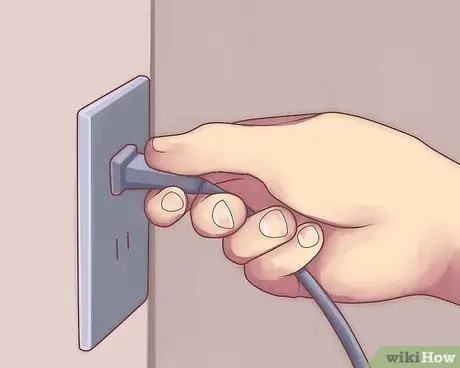
Step 3. Prepare the iron
Plug it in and let it heat up on the mat for a few minutes. Make sure you clean it with a sponge if the iron has been used before (the cleaning method is described above). Coat with tin (which is also described above) after cleaning. When you're ready, set up your components, clamps, and solder.
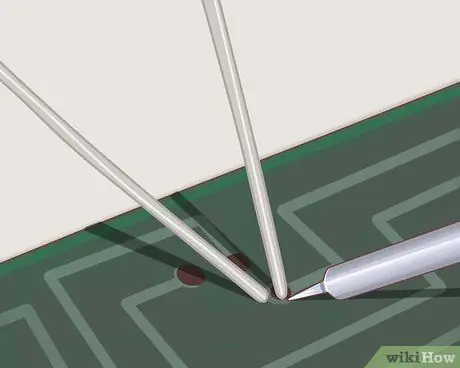
Step 4. Put it in place
Place a component at the point you want to solder. If this component is to be soldered onto the PCB, make sure the component wires are positioned properly through the holes.
For most components, use small clamps or clamps to hold the component in place
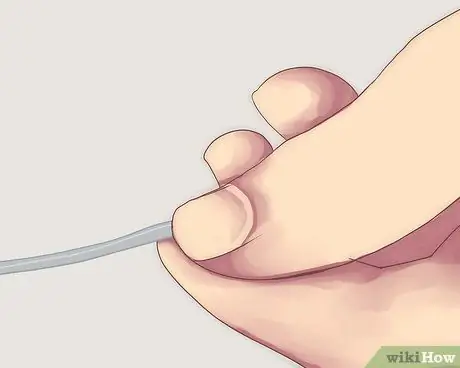
Step 5. Select the soldering wire
Take a certain amount of solder in your non-dominant hand. Use enough length to make sure your hands are far enough from the tip of the soldering iron.
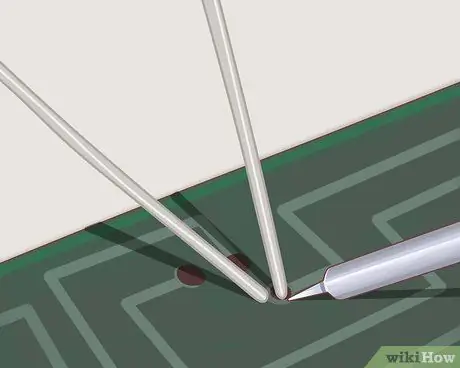
Step 6. Heat the components
Touch the tip of the iron to the component you want to solder. Do it only for about a second. This will heat the metal so it can respond to the solder more flexibly.
- Immediately touch the solder wire to the soldering point, and use the iron. The solder will melt immediately. Soldering to a PCB board won't take more than 3-4 seconds of liquid solder.
- If you need more solder to strengthen the bond, add the pieces slowly with your hands.
- Your solder should come together loosely, forming concave sides as it spreads around the component wires. Solder should not form a ball or thicken.
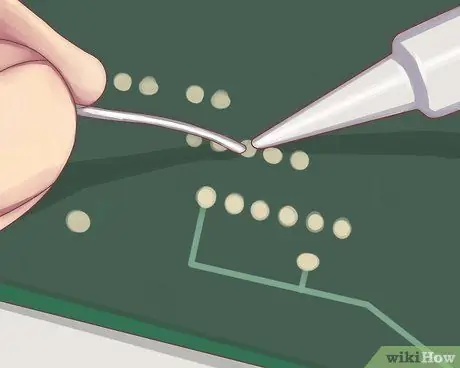
Step 7. Finish soldering
Pull on the solder wire, wait a second, then pull the iron away from the soldering point to let it cool. Again, this process will only take 5 to 10 seconds.
Do not blow on the solder or help cool it. This can cause the solder to become thick and add impurities
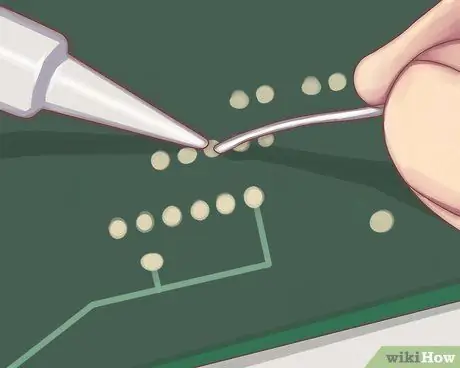
Step 8. Repeat until done
Repeat each of the steps above for each point you want to solder.
Tin the tip of the iron back after a few uses, and again before you put it away. This helps extend the life of the iron
Method 3 of 3: Soldering the Pipe
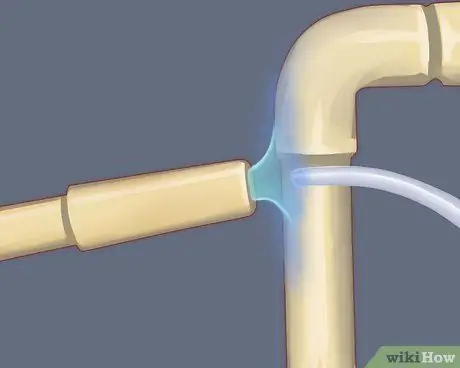
Step 1. Get ready
Soldering copper pipes is not difficult, but requires a lot more effort and a different kind of equipment than soldering electronics. People usually do pipe soldering to seal joints between pipe parts, such as elbow bends.
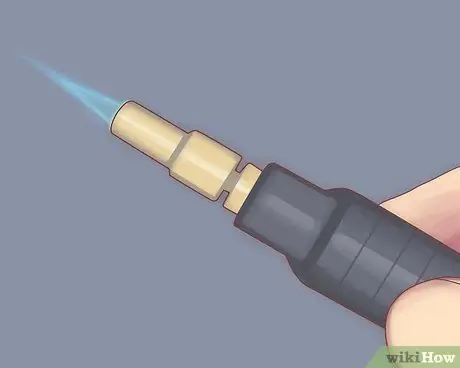
Step 2. Use a welding torch
Use a propane torch instead of a soldering iron to solder the copper pipe. You can buy it at a home supply store.
A special soldering iron can also be used, but a propane torch is just as effective for most pipe soldering, and much less expensive
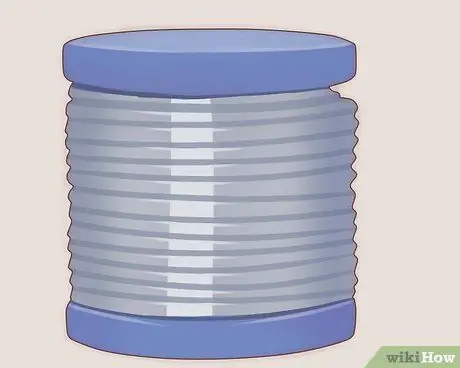
Step 3. Get the solder right
Manufacturers usually make a special solder for soldering pipes. This solder wire is thicker, usually having a diameter of about 0.3 cm. Ordinary pipe solder contains an acidic liquid, but solid wire solder can also be used. Solid cable soldering may require a separate liquid.
Avoid using lead solder to solder your pipes. Read the solder label to determine the composition of the mixture. Pipe solder is usually composed of tin and may contain antimony, copper, and/or silver
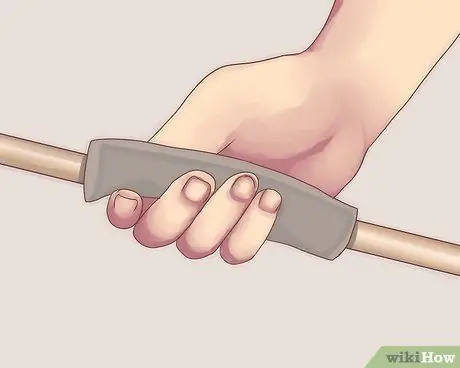
Step 4. Prepare the abrasive
To ensure that the soldering iron works, clean the pipe beforehand using sandpaper, emery cloth, or fine steel wool.
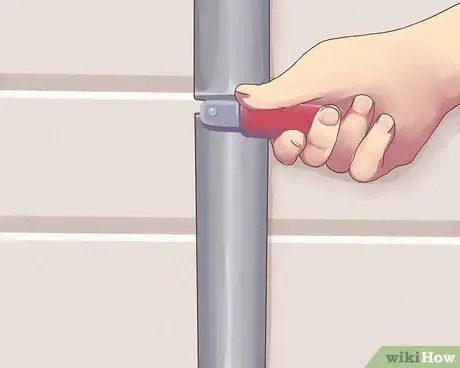
Step 5. Turn off the water
Turn off the water before you start work. This is necessary to prevent the risk of flooding or wetting the room.
Before you turn off the water, prepare a bucket of water. Keep it near you in case your torch burns something
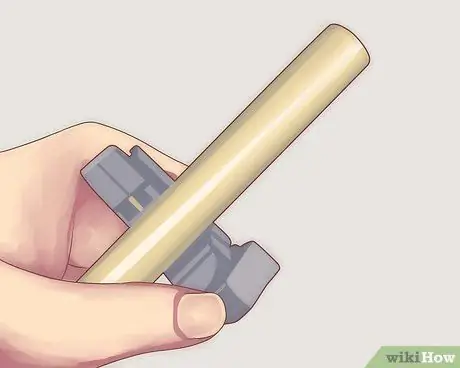
Step 6. Cut your pipe
If you are installing new pipe, use a tubing cutter to cut the pipe to a diameter of 1.25 cm. Tub cutters can be purchased at home supply stores.
- Do it slowly. The tube cutter will be effective in steady slow motion. Do it too quickly and your pipe will be damaged.
- For larger pipes, you will need to use a saw. Trim the edges after you cut.
- Once the pipe is cut, thread it into any joints you need to solder.
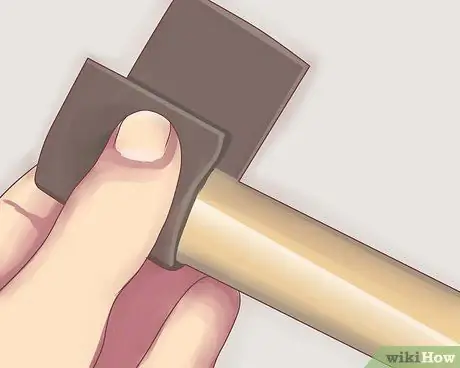
Step 7. Clean the pipe
Using an emery cloth or other abrasive, scrub the area of the pipe where you will solder it, and clean it.
A smooth, clean surface will help the solder join the pipe joints and seal them evenly
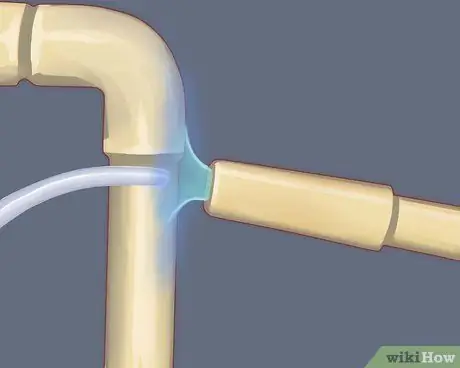
Step 8. Solder the pipe
Light a propane torch and heat the pipe to be soldered.
- Level the heat by moving the flame around the work area.
-
Once the pipe is ready and hot, attach the tip of the solder wire to where you want to solder it. This wire will melt soon.
Hold the solder on the other side of the pipe from your torch. The solder will flow around the pipe joints and fill them
- Allow the connection to cool. It will cool down quickly. Continue to the next section if needed.
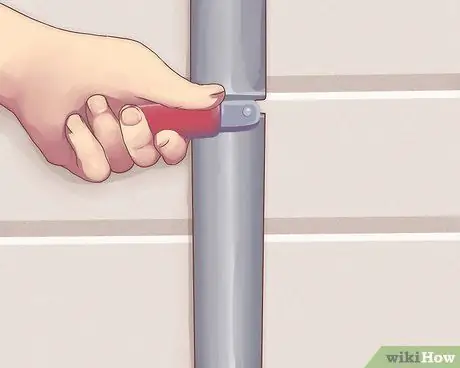
Step 9. Check your work
Once done, wait a few minutes and turn the water back on. Run the water through the pipe you just soldered and check for leaks. If this happens, repeat the above process.
Warning
- Always solder in a well-ventilated area.
- Do not touch the iron between the tip and the handle - you will get a serious burn.
- Always return the soldering iron to its tray after you have completed a section.