Uranium is used as a power source in nuclear reactors and was used to make the first atomic bomb, which was dropped on Hiroshima in 1945. Uranium is mined as an ore called pitchblende, and is composed of several isotopes of atomic weight and several different levels of radioactivity. For use in fission reactions, the number of isotopes 235U must be increased to a level that is ready for fission in the reactor or bomb. This process is called uranium enrichment, and there are several ways to do it.
Step
Method 1 of 7: Basic Enrichment Process
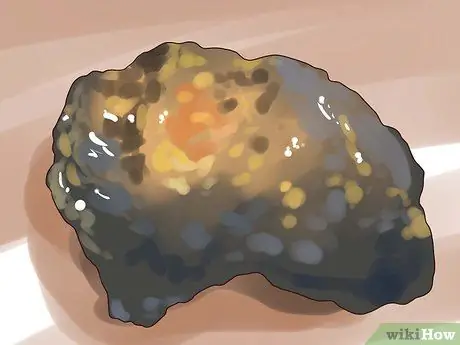
Step 1. Decide what the uranium will be used for
Most mined uranium contains only about 0.7 percent 235U, with most of the remainder being the isotope 238more stable U. The type of fission reaction you want to make with uranium determines how much of an increase 235U must do so that uranium can be used effectively.
- The uranium used in most nuclear power engines needs to be enriched to a level of 3-5 percent 235U. (Some nuclear reactors, such as the CANDU reactor in Canada and the Magnox reactor in the United Kingdom, are designed to use unenriched uranium.)
- In contrast, the uranium used for atomic bombs and warheads needs to be enriched to 90 percent 235U.
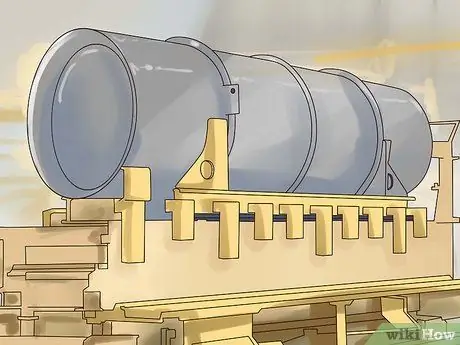
Step 2. Turn uranium ore into gas
Most of the currently available uranium enrichment methods require uranium ore to be converted into a low-temperature gas. Fluorine gas is usually pumped into the ore conversion machine; uranium oxide gas reacts with fluorine to produce uranium hexafluoride (UF6). The gas is then processed to separate and collect the isotopes 235U.

Step 3. Enrich uranium
Later sections of this article describe the various processes available to enrich uranium. Of all the processes, gas diffusion and gas centrifugation are the two most common, but laser isotope separation is expected to replace the two.
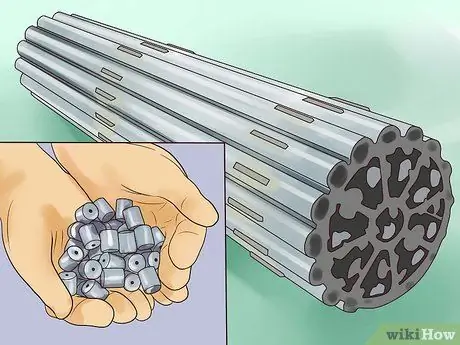
Step 4. Change UF gas6 to uranium dioxide (UO2).
Once enriched, the uranium needs to be converted to a stable solid form for use as desired.
Uranium dioxide used as fuel for nuclear reactors is made into ceramic core grains which are wrapped in metal tubes so that they become rods up to 4 m high
Method 2 of 7: Gas Diffusion Process
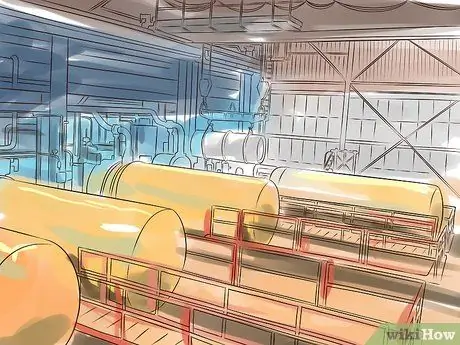
Step 1. Pump UF gas gas6 through the pipe.
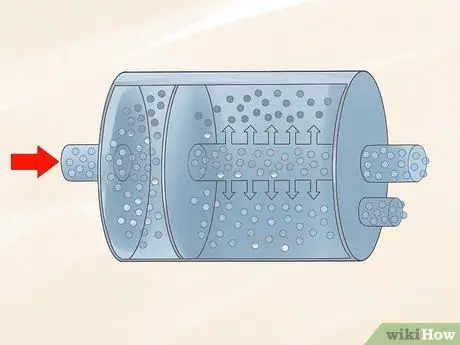
Step 2. Pump the gas through a filter or porous membrane
Due to the isotope 235U is lighter than the isotope 238U, UF6 lighter isotopes will diffuse through the membrane more rapidly than heavier isotopes.
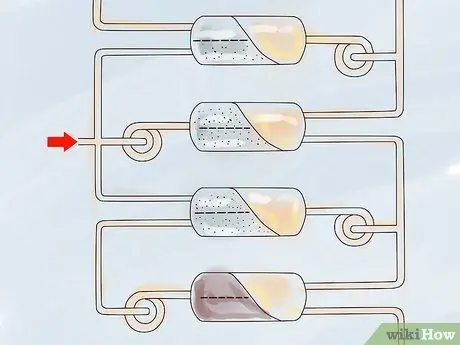
Step 3. Repeat the diffusion process until there is enough 235U collected.
Repeated diffusion is called stratified. It can take as much as 1,400 sieving through a porous membrane to get enough 235U to enrich uranium well.
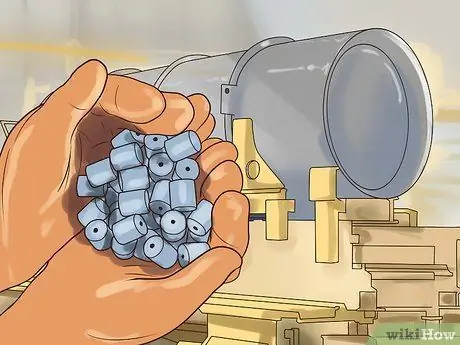
Step 4. UF gas condensation6 into liquid form.
Once the gas has been sufficiently enriched, the gas is condensed into a liquid, then stored in a container, where it cools and solidifies to be transported and made into fuel grains.
Due to the large amount of filtering required, this process is energy intensive so it is stopped. In the United States, only one gas diffusion enrichment plant remains, located in Paducah, Kentucky
Method 3 of 7: Gas Centrifuge Process
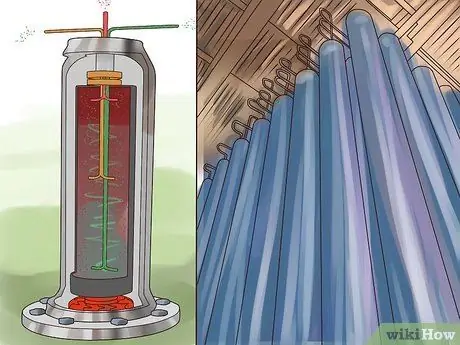
Step 1. Install a number of high-speed rotating cylinders
This cylinder is a centrifuge. The centrifuge is installed in series or parallel.
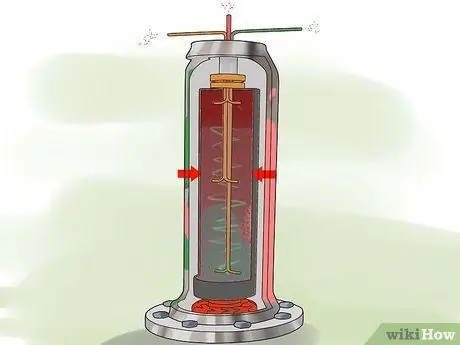
Step 2. Flow UF. gas6 into the spinner.
The centrifuge uses centripetal acceleration to deliver a gas containing 238heavier U to the cylinder wall and gas containing 235lighter U to the center of the cylinder.
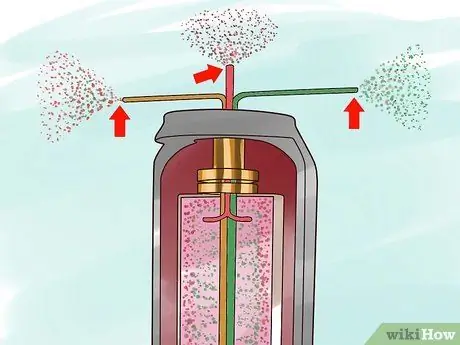
Step 3. Extraction of the two separated gases
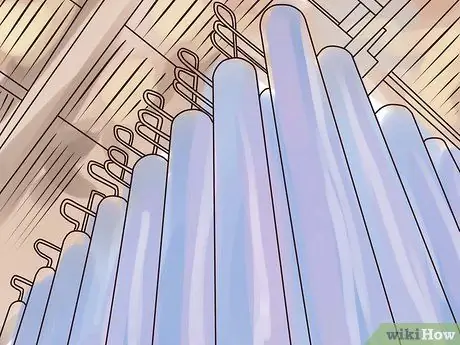
Step 4. Reprocess the two separated gases in two separate centrifuges
Rich gas 235U was sent to a centrifuge where 235U is still more extracted, while the gas containing 235The reduced U is fed into another centrifuge to extract 235The remaining U. This allows centrifuging to extract much more 235U than can be extracted by the gas diffusion process.
The gas centrifuge process was first developed in the 1940s, but was not put into significant use until the 1960s, when its ability to carry out lower energy uranium enrichment processes became important. Currently, the gas centrifuge process plant in the United States is in Eunice, New Mexico. In contrast, Russia currently has four factories of this type, Japan and China have two each, while the United Kingdom, the Netherlands and Germany have one each
Method 4 of 7: Aerodynamic Separation Process
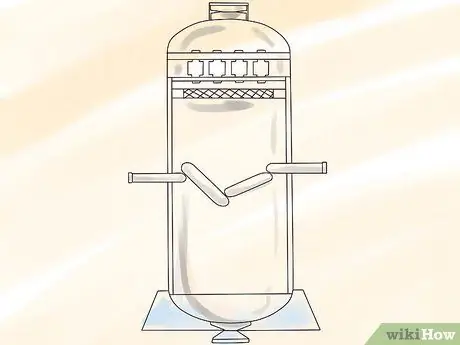
Step 1. Create a series of narrow, stationary cylinders
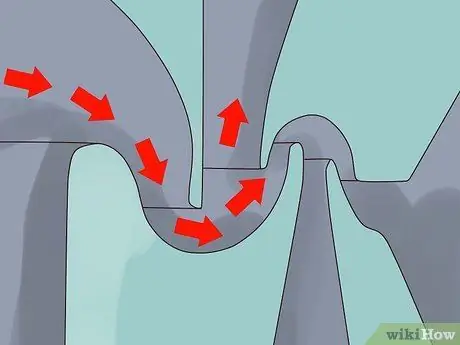
Step 2. Inject UF gas gas6 into the cylinder at high speed.
Gas is fired into the cylinder in a way that causes the gas to rotate like a cyclone, thus producing a type of separation 235U and 238The same U as in the rotating centrifuge process.
One method developed in South Africa is to inject gas into cylinders side by side. The method is currently being tested with lighter isotopes such as those found in silicon
Method 5 of 7: Liquid Thermal Diffusion Process
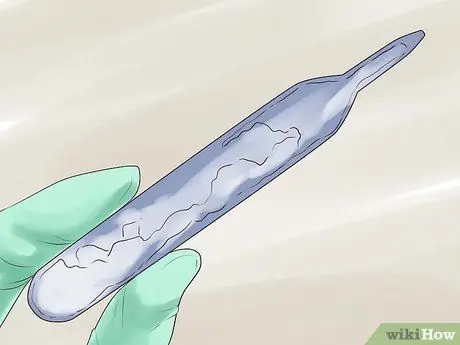
Step 1. Liquefy UF gas gas6 under pressure.
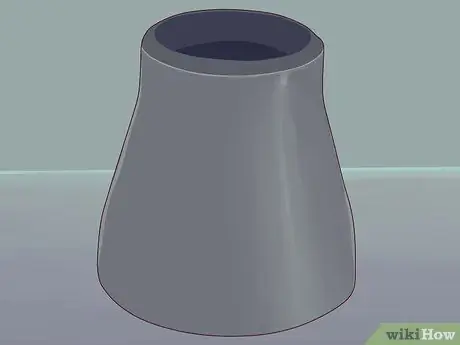
Step 2. Make a pair of concentrate pipes
The pipe must be high enough, because the taller pipe allows more isotope separation 235U and 238U.
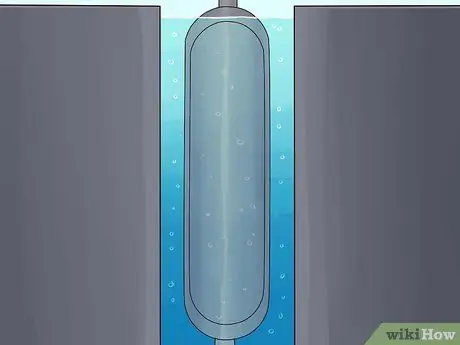
Step 3. Coat the pipe with a layer of water
This will cool the outside of the pipe.
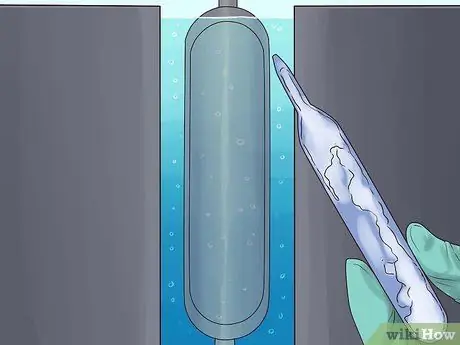
Step 4. Pump UF6 liquid between the pipes.
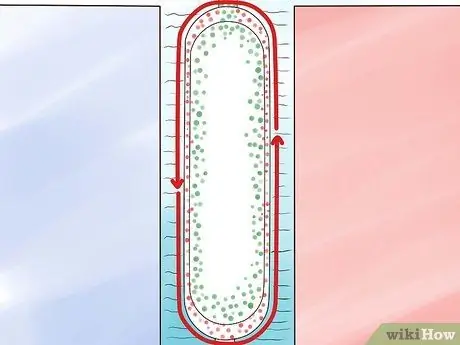
Step 5. Heat the inner tube with steam
Heat will cause convection currents in UF6 which will attract the isotope 235The lighter U towards the hotter inner tube and pushes the isotope 238the heavier U towards the cooler outer pipe.
This process was researched in 1940 as part of the Manhattan Project, but was abandoned at an early stage of development when more efficient gas diffusion processes were developed
Method 6 of 7: Electromagnetic Isotope Separation Process
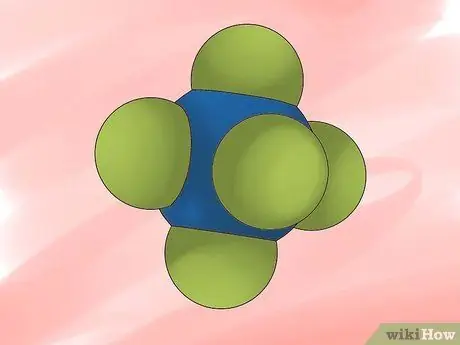
Step 1. Ionization of UF gas gas6.
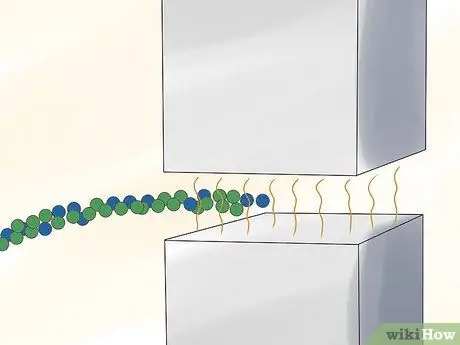
Step 2. Pass the gas through a strong magnetic field
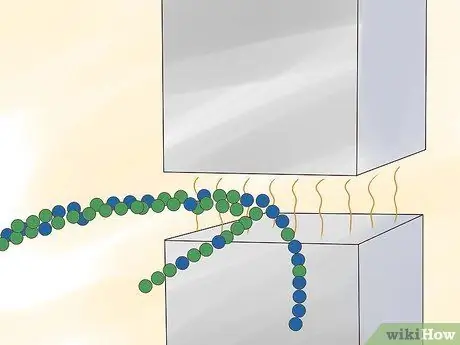
Step 3. Separate the isotopes of ionized uranium based on the traces left as they pass through the magnetic field
Ion 235U leaves a trail with a different arc than the ion 238U. The ions can be isolated to enrich uranium.
This method was used to process uranium for the atomic bomb dropped on Hiroshima in 1945 and is also the enrichment method used by Iraq in its nuclear weapons program in 1992. This method requires 10 times more energy than gaseous diffusion, making it impractical for the program. large-scale enrichment
Method 7 of 7: Laser Isotope Separation Process
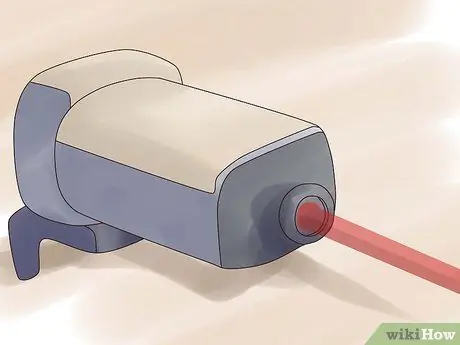
Step 1. Set the laser to a specific color
The laser beam needs to be completely of one particular wavelength (monochromatic). This wavelength will only target atoms 235U, and let the atom 238U are not affected.
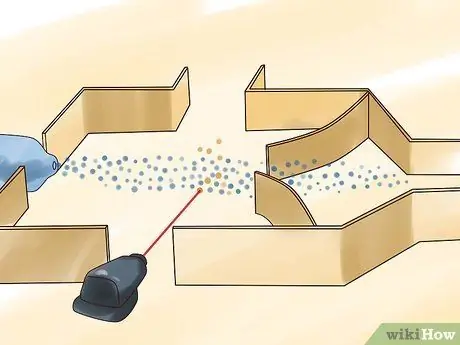
Step 2. Shine a laser beam onto the uranium
Unlike other uranium enrichment processes, you don't have to use uranium hexafluoride gas, although most laser processes do. You can also use uranium and iron alloys as the uranium source, which is used in the Atomic Vapor Laser Isotope Separation (AVLIS) process.
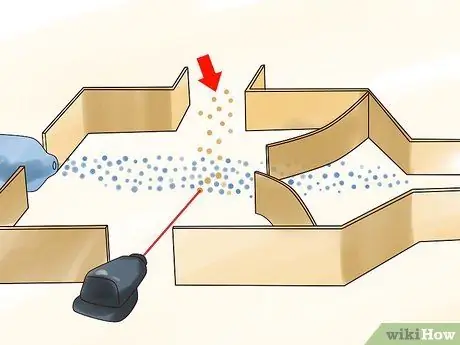
Step 3. Extraction of uranium atoms with excited electrons
It will be atom 235U.
Tips
Some countries reprocess spent nuclear fuel to recover the uranium and plutonium in it that was formed during the fission process. Reprocessed uranium must be removed from the isotope 232U and 236U is formed during fission, and if enriched, must be enriched to a higher grade than “fresh” uranium because 236U absorbs neutrons thereby inhibiting the fission process. Therefore, reprocessed uranium must be stored separately from uranium that was newly enriched for the first time.
Warning
- Uranium emits only weak radioactivity; however, when processed into UF. gas6, it becomes a toxic chemical substance which reacts with water to form corrosive hydrofluoric acid. (This acid is commonly called “etching acid” because it is used to etch glass.) Therefore, uranium enrichment plants require the same protective measures as chemical plants working with fluorine, which include keeping UF gas at bay.6 stay under low pressure most of the time and use an extra level of containment in areas where high pressure is required.
- Reprocessed uranium must be stored in thick enclosures, because 232The U in it decomposes into elements that emit strong gamma radiation.
- Enriched uranium can usually only be reprocessed once.