One way for businesses to remain competitive is to improve their business processes, both from an operational and financial perspective. To do so requires a way to measure specific process progress. "What can't be measured can't be managed." A business can't manage a process if it doesn't have an appropriate measurement method. Therefore, metrics (measurable process details) are used to collect data before and after implementing changes. Analysis these metrics provide data that communicates the amount of improvement that occurs as a result of process changes. To get started, you'll first need to select a metric that fits the process you're measuring.
Step
Part 1 of 3: Setting Up the Process Improvement System
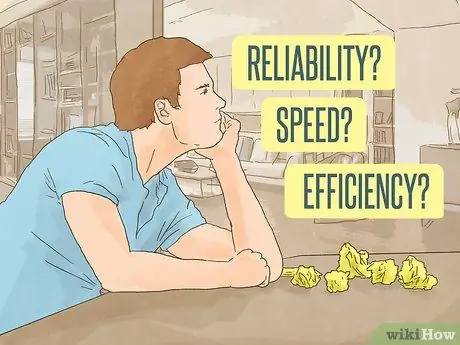
Step 1. Determine what needs to be measured
That is, what do you mean by “improvement”. Do you want a process that is more reliable, faster, efficient, or better at something else? This will clarify your project. Make sure your process produces measurable output.
For example, a company that wants to increase the speed of product delivery will measure the delivery time. A data digitization company may wish to measure the percentage of character errors in a batch, or process output
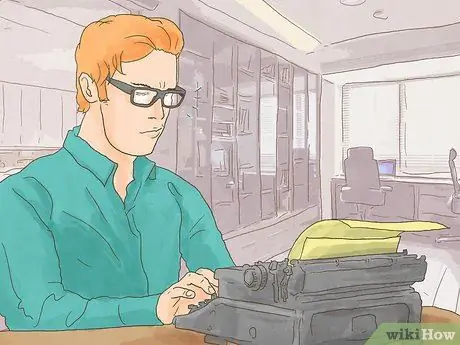
Step 2. Make sure your project vocabulary is consistent
Use commonly understood terms to ensure accuracy and consistency of measurements. This ensures the reliability of the information shared with other parties from different locations and facilities. This will prevent misunderstandings and clarify the definitions of all the variables being measured.
For example, the company measures time in days. Other branches of the same company may have different interpretations of the word “one day”. Perhaps, they think of it as an 8 hour working day, and not 24 hours. Things like this can lead to misunderstandings between the company's branches
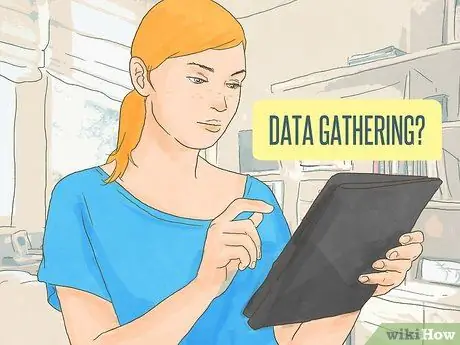
Step 3. Decide how the data will be collected
Data should be collected in the same way across the enterprise. For example, if one department uses a random sample to collect data, all departments should follow suit. Otherwise, the data will not be comparable. In addition, the units of measurement must also be the same. Make sure the units of measurement used are all the same when measuring the output.
For example, delivery speed might be measured in minutes or hours. Converting from one unit to another is just a waste of time
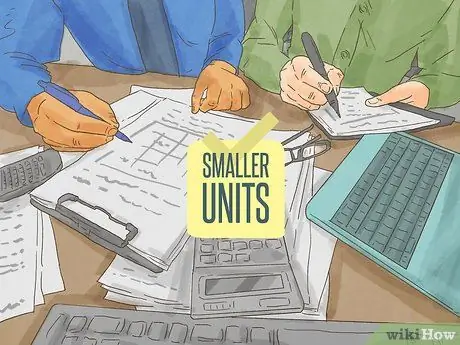
Step 4. Determine the standard of calculation precision
That is, do not let one department round the number until there is no comma and another department round up to two digits after the comma. The difference in the level of detail in the numbers will mess up the results. Don't forget, smaller units tend to give more accurate results.
For example, all departments must agree on how to round numbers
Part 2 of 3: Determining Appropriate Metrics for the Project
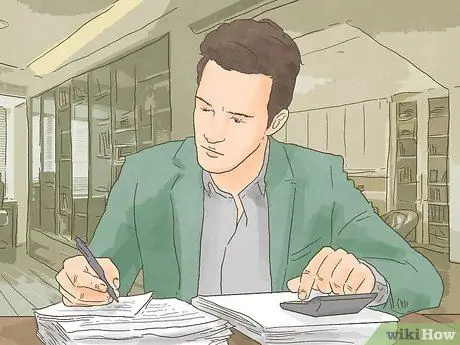
Step 1. Choose a primary metric
Key metrics define the outputs or goals of process improvement. For example, an automobile manufacturer might measure the number of cars produced per hour. Before the process improvement is carried out, the measurement basis is taken first. At the end of the project, the process is re-measured. Then, the calculation of the number of improvements in the process is carried out.
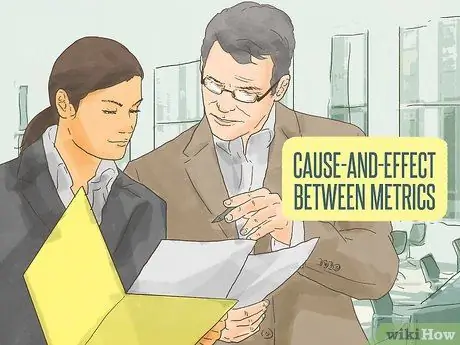
Step 2. Connect key metrics with business metrics
Business metrics measure how operational process improvements achieve one of the company's goals. For example, if the primary metric is to accelerate product production, the business metric can increase profits or decrease fixed costs. There is a cause-and-effect relationship between key metrics and business metrics. This discrepancy explains the reason why improvements in key metrics also improve company performance.
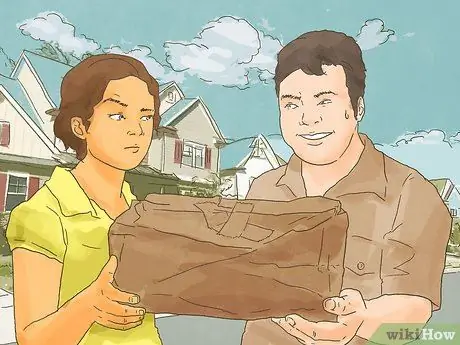
Step 3. Consider possible unexpected outcomes
Unexpected loads may arise as a result of process improvement projects. If the primary metric measures what should be improved, there will be other consequential metrics for measuring what should not change. Consequential metric data should be obtained before, during, and after the project. Of the many possible consequential metrics in a project, only a few have a major impact on output quality and should be taken into account.
For example, a company looking to increase delivery speed should not experience increased costs due to poor handling and product damage. In this case, the proportion of product defects is a consequential metric
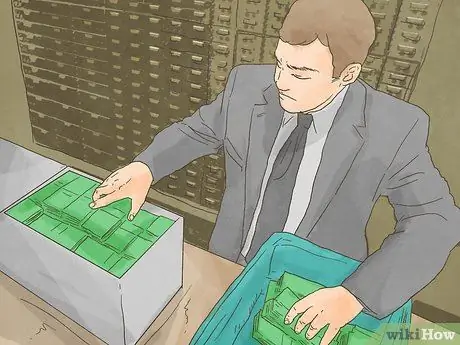
Step 4. Define financial metrics
Saving money isn't necessarily the company's primary metric. However, companies need to monitor the financial results of process improvements. This should not be confused with the accounting costs of the project. Financial metrics should be a tool to analyze the financial benefits of the projects undertaken. Many companies continue to monitor financial metrics for up to a year after the project is complete.
For example, an increase in manufacturing time can be expected to increase the company's revenue. The company will monitor revenue, together with other factors such as profit, from the time of implementation of the change, and to measure how the impact of the process change will be
Part 3 of 3: Collecting Data
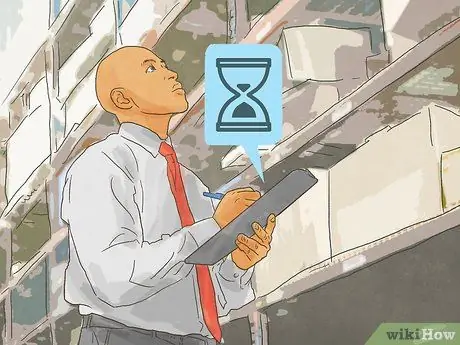
Step 1. Measure the time
Process time measures the length of the steps in the process of making a product or service last. Other time metrics measure the length of time a project adds value, or the length of time it takes to respond to a customer request. The calculation of the metric can be a percentage of delivery time.
Strategies to reduce process time are proven to increase business. This can increase production and faster delivery of products or services. If the price and quality of goods or services are the same as competitors, customers will choose to buy goods or services that are more quickly accepted. If the processing time can be reduced, the chances of receiving new orders and business will be greater
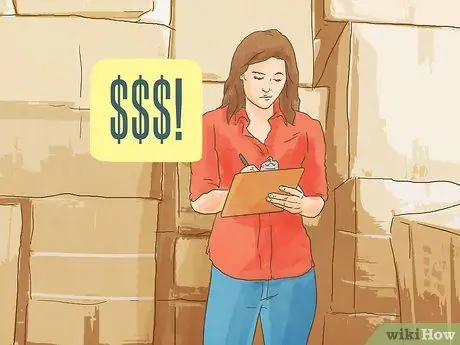
Step 2. Measure costs
The cost metric assesses the total cost of the production process. This metric also measures operating costs relative to production levels. Cost per transaction measures the cost of producing one unit. Cost savings measures the cost reduction per transaction. Labor saving measures the reduction in labor hours required to produce goods or services.
A cost reduction strategy becomes important when business revenues start to decline. For example, Bank of America experienced a decline in lending and trading revenues in 2011. Therefore, they reduced their workforce in order to continue to pay shareholders. Bank managers and consultants decided to use cost metrics to identify jobs that could be written off to save money without hurting the company
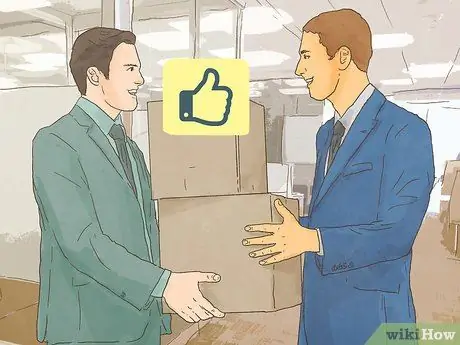
Step 3. Measure quality
Quality metrics measure customer satisfaction. Customer satisfaction data can be obtained through surveys, customer complaints, and other feedback. Quality metrics also assess whether a process adds value to the customer. This metric also looks at the frequency of errors and rework. The percentage of errors will be seen in the level of product defects. The percentage of completion and the level of accuracy measure the frequency of defect-free processes.
- The healthcare industry relies heavily on quality metrics. Quality improvement must be based on data. Analysts look at financial and clinical data to determine variations in health care delivery. The service delivery process is broken down and then looked for wasteful or redundant areas to create a process that delivers high-quality results. Cost reduction does not add value if it cannot improve or maintain a given level of quality.
- The key to improving quality is increasing efficiency without reducing effectiveness. Efficiency refers to the amount of resources required to deliver a product or service. Effectiveness refers to how well the goals of the product or service are achieved.
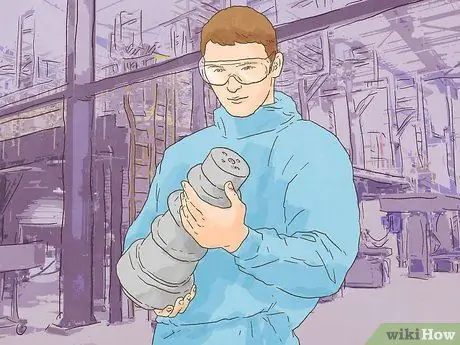
Step 4. Measure the output
Output metrics measure the quantity of a product or service provided over a period of time. Production targets must be aligned with customer demands. Output metrics also look at the backlog and excess inventory (the sum of both should be minimal). Finally, work in progress is measured to determine the number of products or services that are in process.
One strategy to increase output in manufacturing is standardized work. For example, in the automotive industry, car manufacturers have standard methods for installing cars. Manufacturers can set production process standards to increase output. Metrics can help analyze how well a process is improving output. The process is said to be successful if the product is made within a certain time with a new standardized process increasing in number
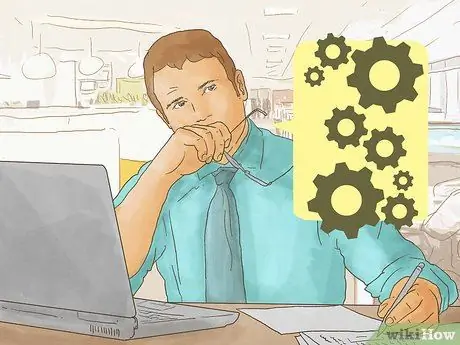
Step 5. Measure the complexity of the process
This metric measures the number of steps in the production process that must be passed. This metric also shows the frequency of process slowdowns due to changes of hands or requests for supervisor approval. The number of steps in the process is counted along with the steps of the value-adding process. These steps make the product or service more valuable. The metric also measures the frequency of product returns for defect repairs.