A wind turbine is a simple mechanical device similar to a windmill. The blades will catch the airflow by using the motion to apply mechanical energy to the control lever. This lever will then turn on the components of the generator, resulting in clean renewable energy for your home and lowering electricity bills. In addition, turbines are easy to make with a variety of simple materials that can be purchased at your local hardware store.
Step
Part 1 of 5: Planning a Wind Turbine
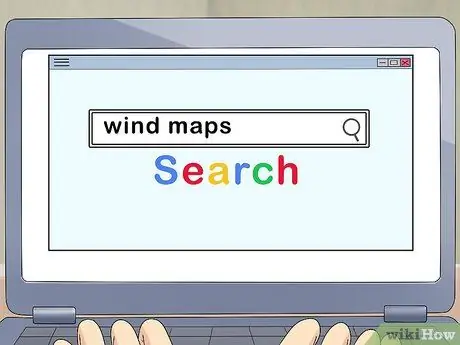
Step 1. Determine the average wind speed at the location you want to build
To generate economic power, efficient wind turbines require wind speeds of at least 11 to 16 kilometers per hour. Most wind turbines will run optimally at wind speeds of 19 to 32 kilometers per hour. To find the average wind speed in your area, check online wind maps.
- You can also buy wind measuring equipment called an anemometer. Use this tool to measure the wind speed at the desired turbine location. Do it every day for a few moments.
- If the wind speed in your area is fairly consistent, measure it for a month, although changing seasons can have a big impact. Then, calculate the average speed value to see if the turbine location would be appropriate.
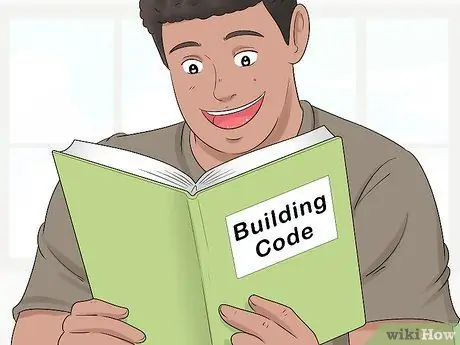
Step 2. Study the building permit related to wind turbines
These permits vary by area, so check with your local government to make sure you're not violating them. Some permits require a minimum distance between turbines, in addition to how far the turbines are from the property line. The turbine may also be height-limited. Take all of these things into account when building.
Discuss your plans with neighbors before spending too much time finalizing and building them. This way, you can listen to their worries about turbines and resolve any misunderstandings that might arise due to noise, radio channel interference, and TV channel reception
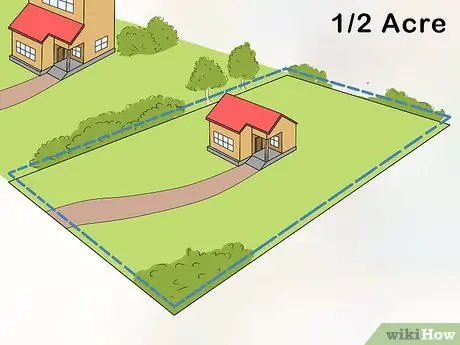
Step 3. Perform a space evaluation for your wind turbine
While this doesn't require a lot of space, to avoid potential conflicts with neighbors, make sure you set aside at least 0.2 acres of space for turbines producing up to 3 kilowatts of power, and 0.4 acres for turbines producing up to 10 kilowatts of power. You'll also need to have enough vertical rungs to build the turbines tall enough to keep the surrounding buildings and trees from blocking the wind.
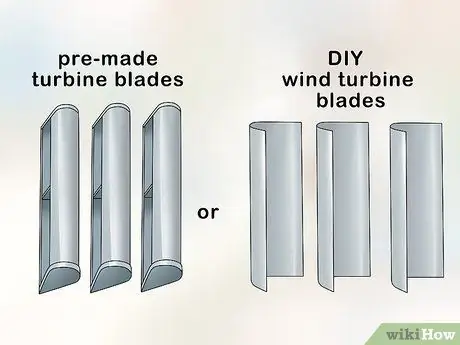
Step 4. Choose between DIY or Do It Yourself wind turbine blades
The type of blades you use and their settings will affect the turbine design. Windmills on old farms were simply blades attached to a rotating axis, but wind turbines represented large motors and had large blades shaped like drops of water. These blades must be properly measured and installed for the turbine to work efficiently.
- If you choose to make your own, use wood or a cross section of PVC pipe. Instructions can be found online through a general Internet search. Use the key phrase “homemade wind turbine blades” or “DIY wind turbine blades” (in English).
- Whether you want to build or buy, make sure there are 3 blades for the turbine. Using an even number, say 2 or 4, makes the turbine more likely to vibrate as it spins. Adding more blades will increase the power, but the turbine will also spin more slowly.
- These blades can also be made from home products, such as modified shovels. If you plan to go this route, choose a sturdy shovel. You can replace the wooden handle with something stronger, like a metal stick.
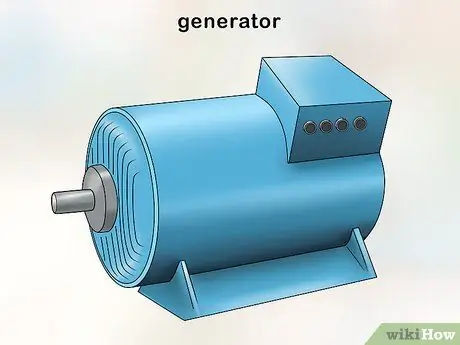
Step 5. Choose a generator
The wind turbine must be connected to a generator to generate electricity. Most generators contain direct current (DC), which means that you have to plug them into a power trigger in order for the generator to produce an alternating current (AC) capable of powering household appliances.
- You can use an AC motor as a generator, although it may not contain enough magnetic power to generate a strong electric current.
- Generators rely heavily on motion, in this case the motion of your blades, and magnetic forces to generate electricity. Ready-made generators are the easiest option for beginners, but you can find tutorials on making your own on the Internet. Type the key phrase “making a wind turbine generator” or “making a wind turbine generator” (in English).
- If you decide to buy a DC generator, look for one with high voltage and low rotational speed (a few hundred instead of a few thousand revolutions per minute). You must produce at least 12 volts consistently.
- The generator must also be connected to the long life battery tank and the power controller in between and the inverter. This is important so that the inverter and the battery are protected from short circuits. In addition, this method will also provide power to the inverter when the wind is not blowing much.
- Automotive alternators are not recommended for use as generators. This alternator must rotate much faster than a wind turbine to maintain power.
Part 2 of 5: Installing the Vertical Axis Shaft and Radius
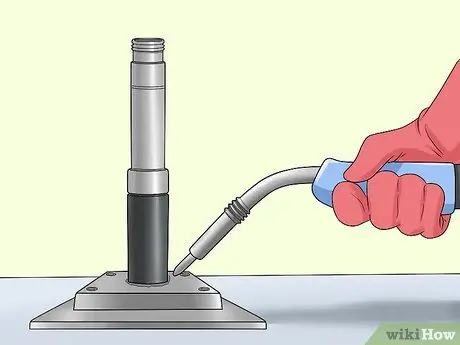
Step 1. Install your shaft
You may have to weld it, but most wind turbine equipment is sold with the shaft installed. If you want to build a turbine from separately purchased parts or components that are idle and must be welded, make sure you wear the proper personal safety equipment, such as welding goggles, welding gloves, welding jacket and work boots.
By putting the shaft components together first, you can build a turbine part by part. This method may be more efficient than trying to build a full turbine right away if you are doing this project alone
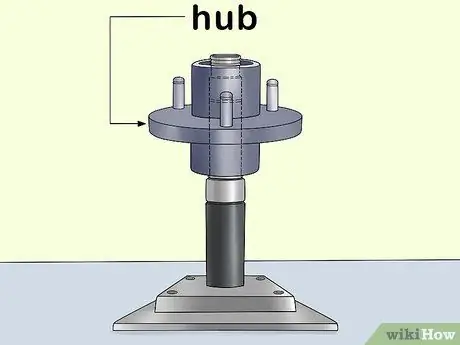
Step 2. Slide the hub into place on the axle
To prevent collision and erosion of these two components, place the bearing between them. Attach it to the end of the shaft protruding from the disk, then slide it into the disk until it is pinched against the thicker part of the shaft. After that, slide the hub on the bearing so that the pile parts are facing up.
- There should be a gap of about 10.2 cm between the shaft and the bearing. In areas of high wind speed, the turbine may bend so that the blades damage the shaft.
- If you don't have the equipment and are building a hub from the ground up, consider using a 4 on 4 trailer hub. You can buy it at most stores that sell trailer equipment, such as your nearest auto parts store.
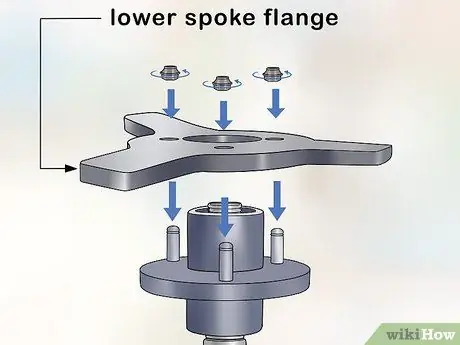
Step 3. Attach the lower finger flange to the hub
The flange should have holes for the hub post to pass through, as well as protruding parts for mounting. Align the flanges with the hub posts and attach them together. After the flanges are evenly placed, secure them with nuts. Install the nuts by hand first then use a wrench.
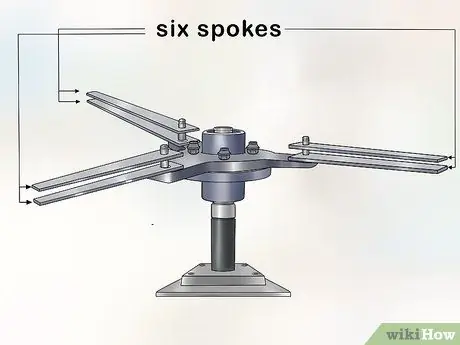
Step 4. Connect all the spokes
You will have two radii per turbine blade, making a total of six for a three-bladed turbine. You'll need bolts to connect the spokes to the bottom flange tabs, as well as a spacer spacer to separate them from the top. Then:
- Slide the bolt through the hole in one of the flange tabs, attach the spokes, use the spacer, attach the second spoke to the bolt, then clamp all the spokes and spacers with the top flange. Both the top and bottom flanges must be the same shape, as well as the number of mounting tabs.
- Tighten the bolt on the top flange by hand, then tighten the other bolt. Repeat this process for all the spokes.
- Once all the fingers are caught between the top and bottom flanges, use a wrench to tighten the bolts. Then, make sure the top and bottom flanges and spokes are sturdy and easy to rotate with the hub on the bearing.
- Since the turbine will be exposed to the consistent power of the wind and other environmental factors, make sure the bolts connect the spokes firmly. To do this, use a bonding compound, which can be purchased at most hardware stores.
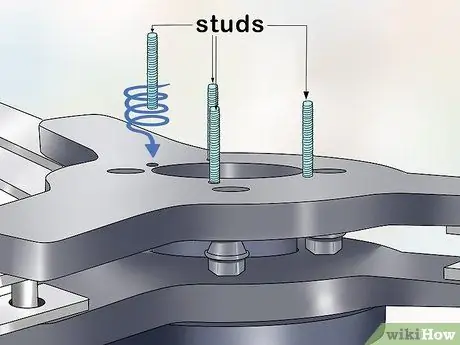
Step 5. Attach the four posts to the top flange
These poles must be threaded and 6 cm long and 0.635 cm thick. You may need to use a metal saw to cut the threaded posts of the correct thickness to the correct length. Then, attach these posts by hand to the top of the top flange, so that each bolt is evenly distributed around the shaft of the turbine shaft.
- Mount these poles far enough apart so that they are all upright and sturdy. The mast should protrude from the flange an equal distance.
- When using a metal saw, be careful not to damage the thread of the post. A damaged thread may prevent you from being able to tighten it properly.
- Make sure that all the posts are securely in place, like the bolts you used for the turbine spokes. Use a bonding compound to secure these posts.
Part 3 of 5: Installing the Vertical Axis Magnet
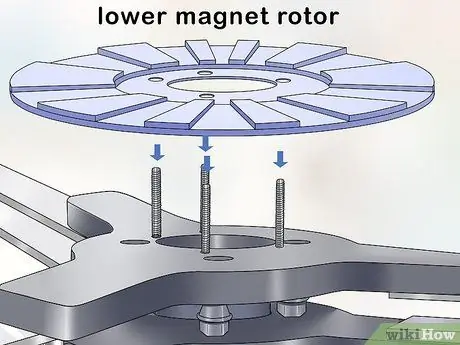
Step 1. Attach the bottom magnetic rotor to the poles
You can make top and bottom magnetic rotors with 5 x 2.5 x 1.25-inch plates, epoxy, and neodymium magnets. Or, you can buy ready-made as part of the turbine generator kit from the manufacturer. Mount the bottom plate of the magnetic rotor on the four posts that have been screwed on to the flange. Make sure the magnet is facing up.
- Whether making your own or using a ready-made magnetic rotor, be careful. The magnetic field is very strong and can cause injury if you are careless.
- Neodymium magnets are very brittle. You'll need 24 of them, 12 for the top magnetic rotor and 12 for the bottom magnet rotor, but buy a few spares in case one breaks. These magnets can be purchased online.
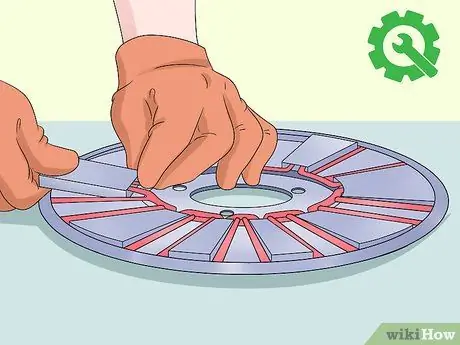
Step 2. Make a magnetic rotor if needed
If you are using a fixture that contains a magnetic rotor disc, you only need to attach the disc to the posts as described. For housing magnet rotors, make sure they are evenly distributed around the periphery of the rotor. To prevent improper placement of the magnets that could potentially destroy the rotor, draw a magnet placement template on cardboard or paper.
- This template will occupy the center of the rotor that is not magnetized. The lines from the center to the edges of the template indicate the location of the magnets on the rotor. You can use tape to attach the template. Look for examples online.
- You must mark the poles of all magnets before starting to place them. You can do this with a marker. If the magnets stick together and you can't analyze the poles, try testing it by attaching a weak magnet to a popsicle stick.
- Pass the "U" pole of the tester in front of the neodymium magnet. If you feel a push, it means the magnets are on the same side of the poles. If you feel a pull, the poles of the magnet you are testing are opposite.
- Use pea-sized epoxy when attaching magnets. Attach to the bottom of each magnet before placing.
- Be careful and make sure your fingers are not between the magnet and the rotor. Then, move the magnet to the corner of the rotor disc slowly. The magnet will stick. After that, slide the magnet into the correct position following your template.
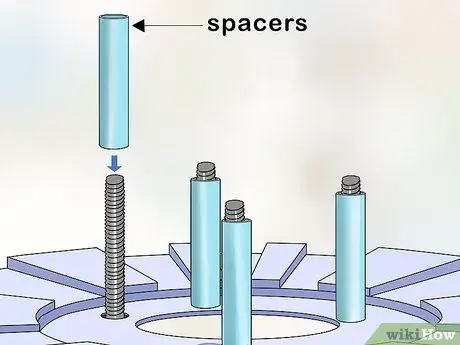
Step 3. Install the spacers on the turbine poles
You can use a 3,175cm (3,175cm) diameter piece of metal tubing to create space. Cut as accurately as possible. Slip it over the pole protruding from the magnetic rotor.
- Spacers of uneven length can bend the top magnetic disc. This can be dangerous and negatively affect turbine efficiency.
- There should be more than 2.5 cm of space remaining above the spacers on the posts. This way, the nuts can be tightened on the magnetic rotor and all the parts in between.
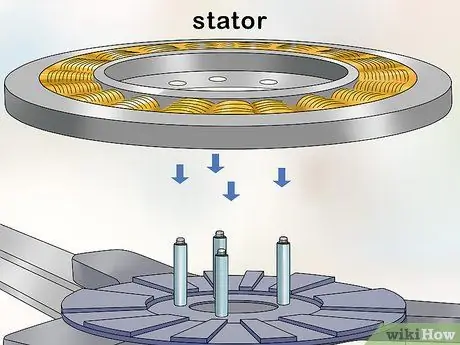
Step 4. Place the stator on top of the lower magnetic rotor
The stator is a set of copper wires that is vital to all types of generators. You can buy it as part of a wind turbine kit or make your own. The poles surrounding the axis of the shaft must protrude upwards past the center of the stator.
- The stator needs three groups of 24 copper wires, each wrapped 320 times. Making it may be difficult and time consuming.
- If you decide you want to make your own, search online for the key phrases “how to make a wind turbine stator” or “how to make a wind turbine stator” (in English) to help you.
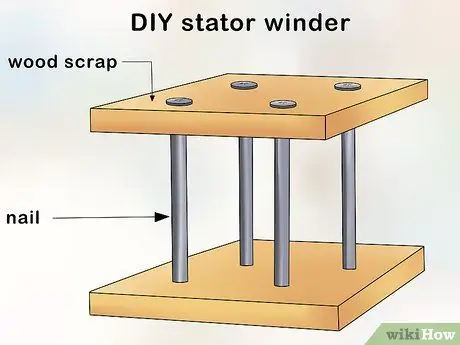
Step 5. Make the stator winders for the housing stator
You can use scrap wood and nails. Connect two pieces of plywood with four nails so that there is a 2.5 cm gap between them. Nails should be spaced in a grid pattern that corresponds to the dimensions of the magnet. This will make it easier for you to wind the copper wires used to make the stator.
- When making your own stator, make sure you mark the start and end. Each layer must be wrapped in the same direction. Consider applying colored electrical tape to each end of these rolls.
- To prevent the roll from coming off when you're done, tape it with electrical tape and secure it with two-part epoxy. Allow the epoxy and stator to dry on the wax paper according to the directions on the epoxy label.
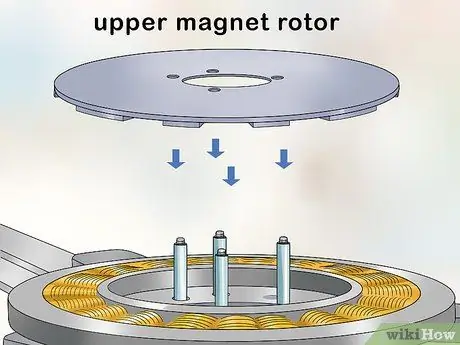
Step 6. Install the top magnetic rotor
Make sure you are very careful; This is one of the most dangerous parts of a wind turbine. Stack four boards on the stator on either side of the center axis. The baseboard should be thicker and the topboard should be thinner. You can use a 5 x 10 cm board for the top board.
- Hold the top magnetic rotor so that your fingers are in the gap between the stacked boards. Lower slowly towards the lower rotor. Try aligning the top rotor with the turbine studs while doing this.
- A magnetic field will stick to the top disc and pull it toward the board you've placed it on. Then, lower the top magnetic rotor onto the posts by tucking the boards one at a time. First, lift one top board, then the other.
- Repeat this process on the lower board to maneuver so that the upper magnetic rotor is in the correct position. Then, use the nuts on the posts to tighten the rotor in position. When finished, the top rotor should rest against the spacers, with only a small portion of the mast protruding from the top.
- You may have to flick the board to free it from the top magnetic rotor. The magnetic force here will be very strong.
Part 4 of 5: Completing the Turbine
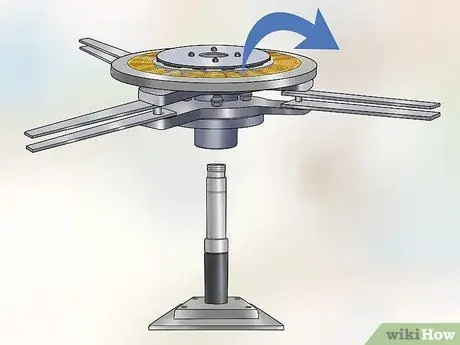
Step 1. Remove the frame from its axis
Next, you must connect this shaft to the Tower. Doing this when the turbine frame is in place is difficult. You also have to bend it, pointing the hub up for the turbine to finish.
Pull all frame parts (including hubs, spokes, magnetic rotor, stator, and other connected parts) off the shaft in an upward motion. Then, place the frame on the work area with the hub side facing up
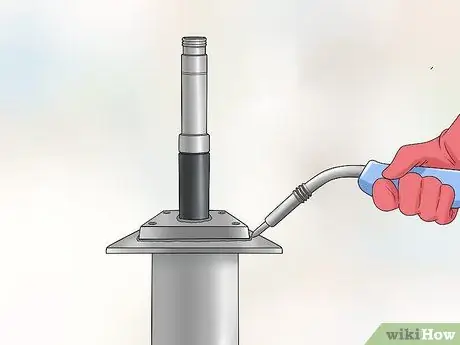
Step 2. Weld the axle flange to your tower
If you purchased a turbine kit, these parts may be readily available, but otherwise you'll need to attach a metal plate to the thick, sturdy metal tubing for the tower part. Make sure this pipe can withstand the wind power generated by the turbine.
The tower must be installed in a strong location. You may have to pour concrete on the tower's foundation to make it more stable
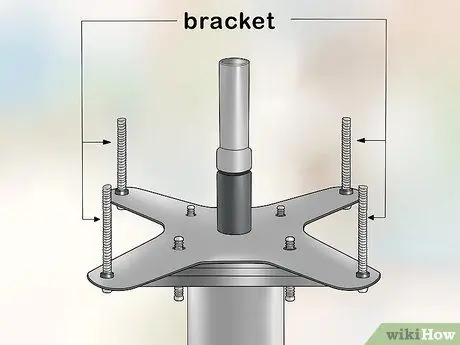
Step 3. Install the shaft and spoke limiters
This barrier, or cage, should surround the shaft like a collar. Then, use the bolts to attach it to the tower. Then, cut the threaded pole with a diameter of 0.375 cm into four sections 11.25 cm long. Use bonding compound first, then nuts and washers to attach it to the cage. Face up.
Nuts should be placed on posts with a diameter of 0.375 cm, about from the top. This nut will allow you to adjust the position of the stator while the mast maintains it
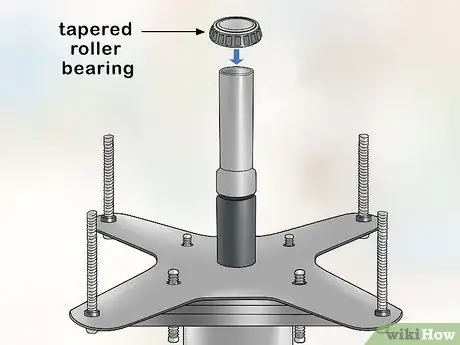
Step 4. Place the roller on the shaft
Before doing so, you should apply a small amount of oil to the bearings. After that, slide the threaded bearing into the shaft so that it rests against the bottom.
The oiling process is easiest to do with your fingers. Have a paper towel or work cloth handy for easy cleaning of the net after the bearing has been greased and placed
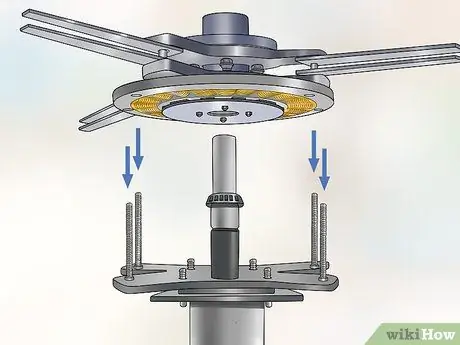
Step 5. Install the turbine main frame
Lift the main frame so that the hub is facing forward and attach it to the axle with the threaded bearing position underneath. The mounting holes in the stator must be parallel to the threaded posts screwed into the cage.
- Once the frame is in the correct place, attach another threaded bearing to the top of the hub. Oil with common bearing oil.
- On it, attach the hexagon nut. This nut must be tightened with a finger.
- If the nut is difficult to turn, remove it until the space is level with the hole in the shaft. Slide a pin in this hole and use pliers to bend it so that the nut can be tightened.
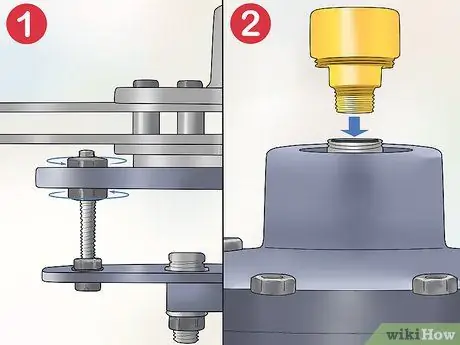
Step 6. Tighten the stator as well and finish the turbine using the grease cap
Install one hexagon nut for each post to secure the stator to the turbine frame. Then, using two wrenches, adjust the position of the nuts that flank the stator so that they fit between the two rotor magnets.
After the stator position is correct, you just need to add the oil cap at the top of the hub. The turbine has been completed
Part 5 of 5: Installing Electrical Components in the Turbine
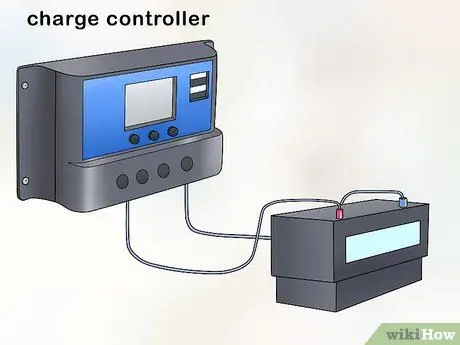
Step 1. Connect the current controller to the battery or circuit
Connecting the current controller to the battery before connecting it to the turbine will prevent a short circuit. That way, your equipment won't be damaged either.
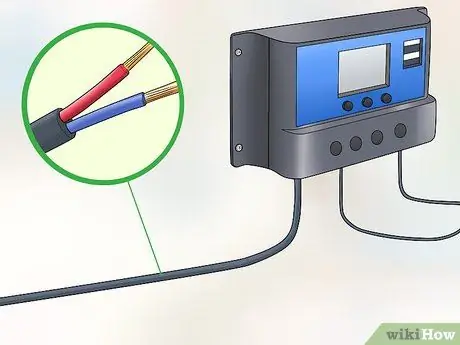
Step 2. Connect the coated wire to the current controller
The wire will transfer power from the generator to the current controller. From here, electricity then enters the battery or circuit.
This wire should be like the wire inside the power cord, with the two bonded together in similar insulation. You can use an old extension cord with the plug part removed
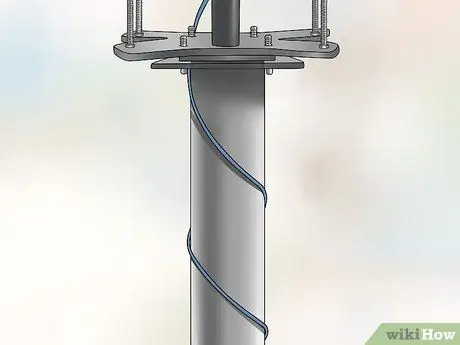
Step 3. Pass the ply wire through the tower pylons and bottom
Insert it into the tower until it reaches the turbine frame above. You may need to use heavy thread or tape to help position the wire in the tower. Then, connect this wire to the generator.
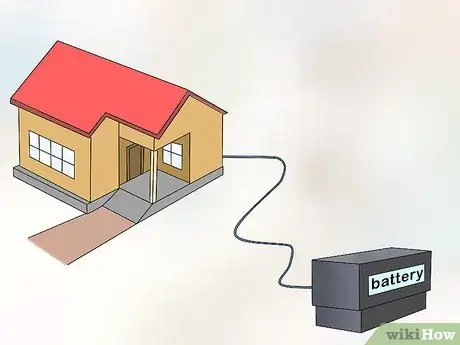
Step 4. Connect the battery or circuit
Once the generator is connected to the power controller and past the base of the tower, you are ready to complete the turbine. Always consult a professional electrician whenever you connect an external power source to the main house circuit. Many areas require the services of a licensed professional to handle this type of cable arrangement.
Tips
- You must cover the power controller to protect it from moisture. You may also be able to wire up the voltage meter to monitor the power the turbine is producing.
- Do some research on bird migration in your area. If any species fly past the area, avoid building turbines.