Printing plastics is a fun and inexpensive activity to create masterpieces or replicas of your favorite objects. Plastic molds can be purchased or made yourself from recycled plastic, silicone, or plaster. Fill the mold with plastic resin, wait for it to dry, then take it out to see your creation.
Step
Method 1 of 4: Making a Mold from Recycled Material
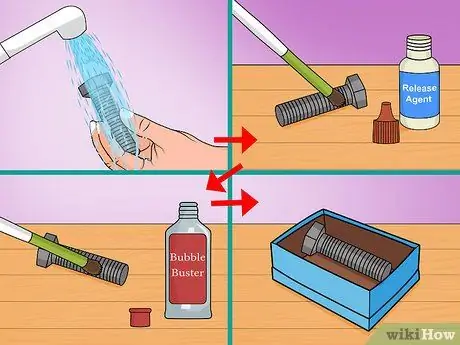
Step 1. Prepare the main material
The main material is the object used to make the mold.
- Before using the main material, wipe or wash the object first.
- Once clean and dry, apply a lubricant to the object to be printed - this will ensure that the main material can be removed from the mold.
- Cover the item with a bubble buster - this product can prevent air bubbles from forming around the main material.
- Place the main material in a heatproof container. This container should be slightly larger than the object.

Step 2. Melt the recycled molded material in the microwave
Recycled molded materials are very easy to use and fail-safe; You can melt, print, and reuse the material up to 35 times. Place a container of recycled material in the microwave. Follow the product instructions carefully to melt the material well.
- Heat the material in short intervals, about 15 to 20 seconds, until you understand the effect microwave heat has on the material.
- If you don't have a microwave, you can use a double boiler.
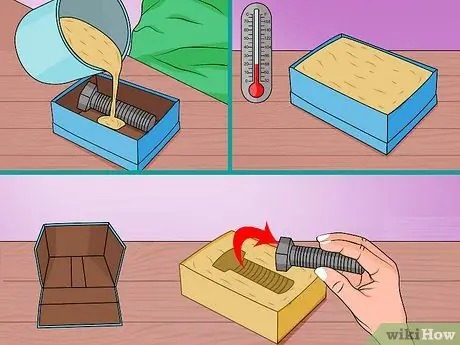
Step 3. Pour the melted material over the main material
Carefully pour the melted mold material over the main material. Let the liquid cool and harden. Gently remove the mold from the heat-resistant container and remove the main material from the mold.
Method 2 of 4: Making Silicone Molds
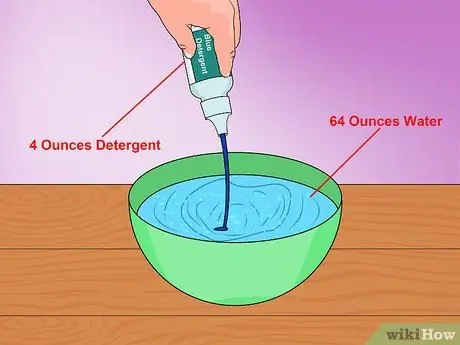
Step 1. Make a liquid catalyst with soap and water
When a high concentration of dish soap is mixed with water, it forms a liquid catalyst for the silicone - this liquid will allow the silicone to dry faster. Take a large bowl and mix about 2 liters of water with 120 ml of dish soap. Stir the water and soap by hand.
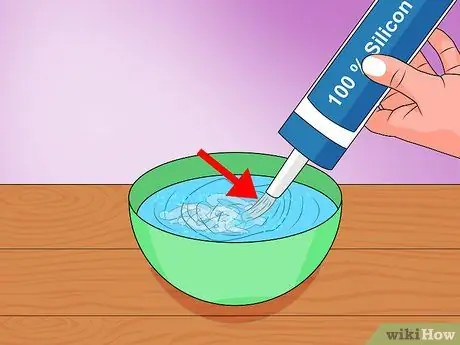
Step 2. Perform silicon catalysis
Use scissors to cut off the 100% silicone tip. Put the bottle in a caulk gun. Put enough 100% silicone into the catalyst liquid to soak the main material.
If you don't know how much you need, use the entire contents of a 100% silicone bottle
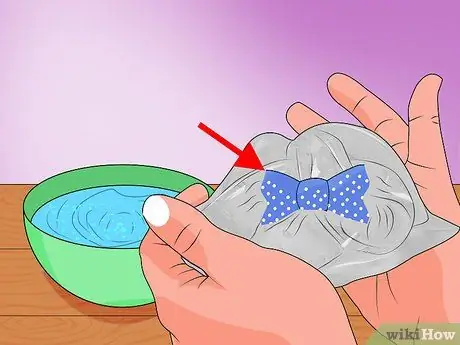
Step 3. Knead the 100% silicone in the catalyst liquid by hand
Dip your hand into the catalyst liquid and knead the silicone inside into a ball. Massage the ball with your fingers. Pull, stretch, and fold the silicone while squeezing it. Continue this process until the silicone becomes stiff and hard to form.
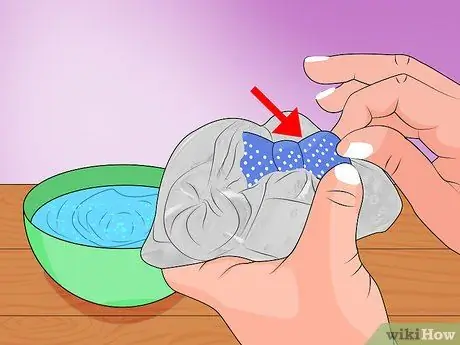
Step 4. Make the mold
Take the main material. Smooth out a layer of 100% silicone to achieve a thickness of about 1 cm. Cover the main material with silicone - press the silicone all over the surface of the main material, including the grooves and edges. Once the mold is formed, try to shake the main material and remove it from the mold. If you can do this easily, the mold is ready to dry. If you can't, change the shape or remove some parts of the mold.
Apply lubricant to the main material to make it easier to remove from the mold
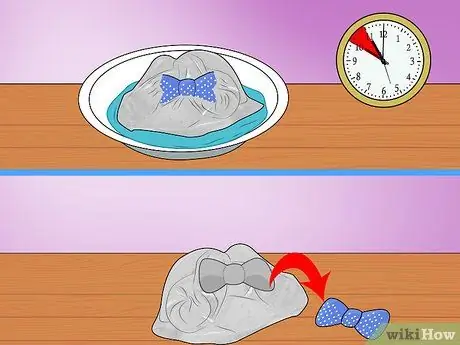
Step 5. Allow the mold to dry
Pour soapy water over the paper plate until it covers the surface - this will prevent the silicone from sticking to the plate. Prepare the mold and place the main material on a plate and let it dry for 1 hour. When the mold no longer feels sticky to the touch, remove the main material inside.
When the mold is drying, it is very important to allow the main material to remain in the mold
Method 3 of 4: Making Double-Sided Prints
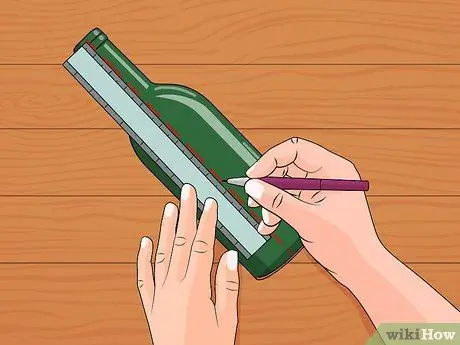
Step 1. Mark the center line on the main material
The two sides of the print will be connected exactly at the center line of the main object used. Prepare the main material, permanent marker, and ruler. Draw a straight line around the main material.
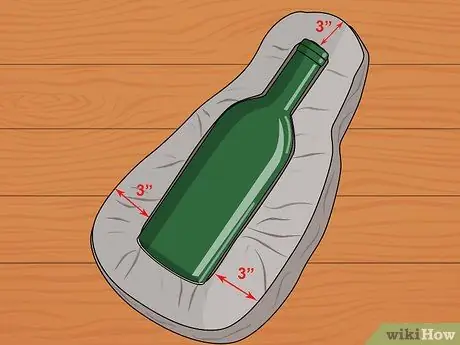
Step 2. Immerse half of the main material in the clay
Set up a block of wet molded clay on top of the work area. Dip the main material into the clay to the center line. The top of the material should be parallel to the surface of the clay. There should be a gap of about 3 cm between the main material and the clay edges on all three sides.
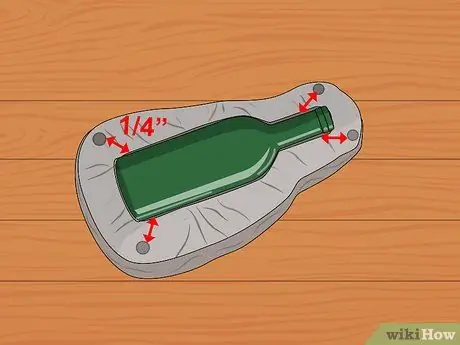
Step 3. Install the 4 alignment keys on the top of the clay
This key will hold the two sides of the mold together perfectly. Prepare 4 alignment keys measuring 1.5 cm and 1 bottle of temporary adhesive. Apply a thin layer of temporary adhesive to the flat surface of the lock. Position the key about 1 cm from the top left corner, then glue it directly to the surface of the clay. Place 1 lock on the other three corners.
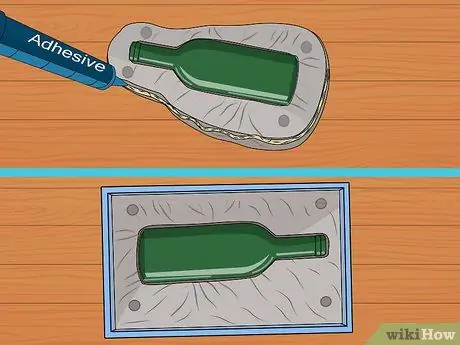
Step 4. Create a wall to secure the main material
To fill the mold, you must provide an opening. For this mold, the opening will appear above the clay surface. Apply a thin layer of temporary adhesive to the top of the main material - the side that is not covered with clay - and the sides of the clay (the side that is under the main material). Press the sides into the wood or metal retaining wall. Leave it on until it dries.
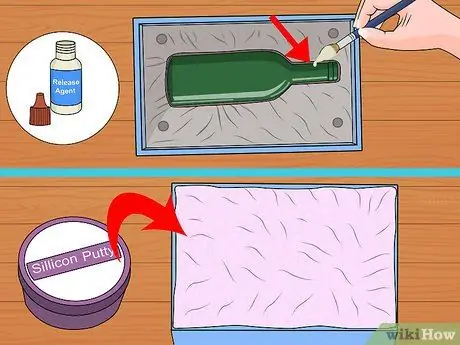
Step 5. Cover the exposed half of the main material with molded silicone putty
One layer of molded silicone putty will form one inner retaining wall. Coat the main material with lubricant. Apply a layer of print putty to the exposed half of the main material. Apply molding putty to the clay surface, and gently apply it to cover the alignment lock. Allow the print putty to cover the area up to 1.5 cm above the retaining wall.
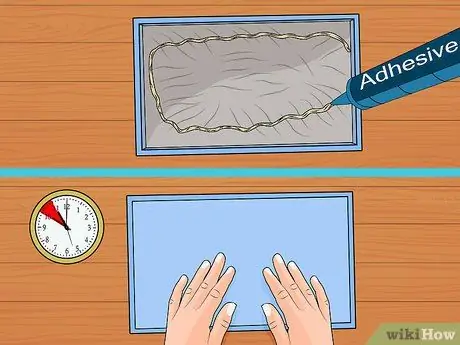
Step 6. Install the second retaining wall
Apply a thin layer of temporary adhesive to the base of the clay surface (the side parallel to the top of the main material). Press the side until it is firmly against the wooden or metal wall. Allow the adhesive and molding putty to dry for 1 hour.
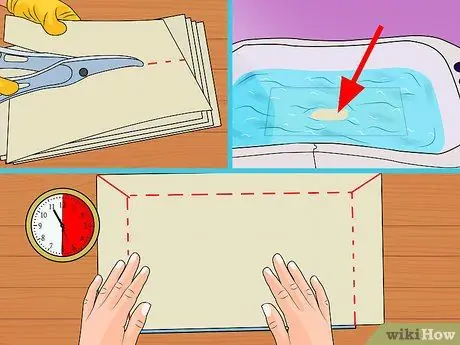
Step 7. Make a durable mother shell
Because the dried mold putty has high flexibility, it is very important to make a stronger second shell or parent shell. You will make the master shell with a sheet of plaster.
- Cut 4 to 6 sheets of plaster. Each piece of plaster should be about 15 cm longer than the mold.
- Stack the plaster sheets.
- Dip the plaster sheet in a bowl of water for 1 second.
- Remove excess water by squeezing a wet plaster sheet over a bowl. The sheet should be wet, but not soaked to the point of dripping water.
- Lay the plaster sheet over the molding and retaining wall.
- Press the tape into the mold so that it matches the shape of the mold. Make marks along the retaining wall at a 90° angle -- the plaster sheet parallel to the retaining wall will serve as the legs.
- Let the plaster dry for 30 minutes.
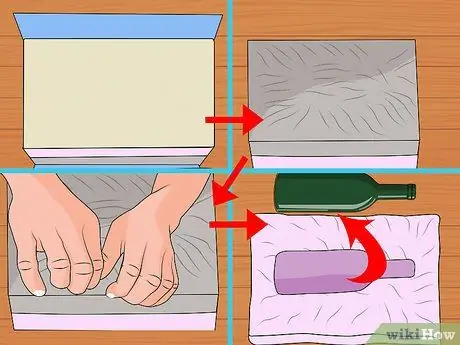
Step 8. Remove the retaining wall and clay surface
Once the plaster has hardened, remove the two retaining walls. Turn the entire mold over so that it is held in place with two legs of tape. Gently remove the clay mold along with the remaining soil adhering to the main material.
If the alignment lock does not come off with the clay, remove the object as well
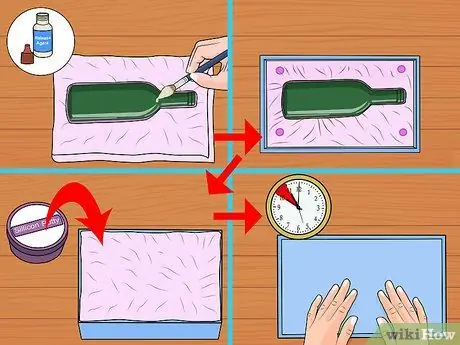
Step 9. Make the remaining half of the 2-sided mold
When making the second part of a 2-sided mold, you just need to repeat the above process:
- Apply lubricant to the main material.
- Glue the top of the mold to the retaining wall.
- Coat the main material with molding putty.
- Glue the base of the mold to the retaining wall.
- Make the master shell from the plaster sheet.
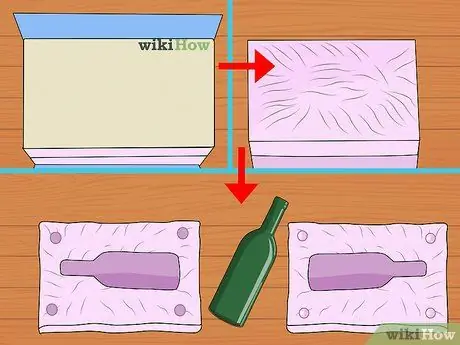
Step 10. Remove the main material from the mould
After the plaster has dried for 30 minutes, you can start assembling the mold. Remove the two retaining walls from the mould. Position the mold best over the work area. Remove the mother shell and gently peel off the silicone mold. Remove the main material and reassemble the mold.
Method 4 of 4: Pouring the Mold Contents
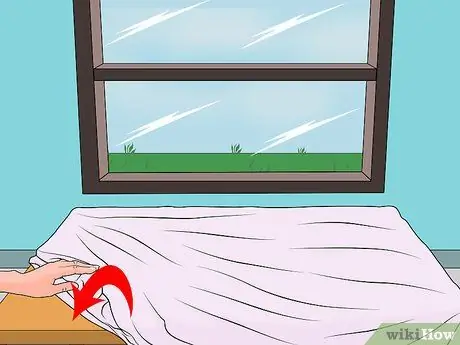
Step 1. Prepare the work area
Look for a flat work area that is light and well ventilated. Line the area with clean kitchen tissue or used paper.
- Newspaper is not recommended for use as a base because the ink may smudge and stain prints or plastic printouts.
- You can also line your work area with a trash bag or an old vinyl tablecloth.
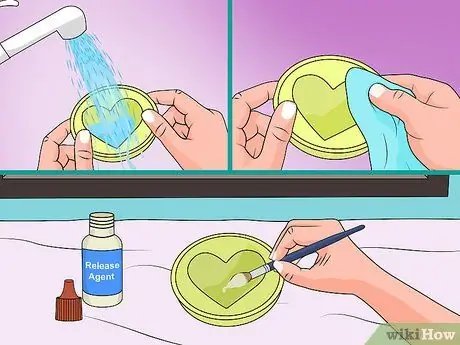
Step 2. Prepare the mold
Good handling of the mold is critical to the success of your project.
- If you are using a ready made mold, first wash the item thoroughly with hot water to remove the starch coating, then dry with a clean cloth.
- Coat the mold with lubricant.
- If you are using a double-sided mold, coat both sides and reassemble.
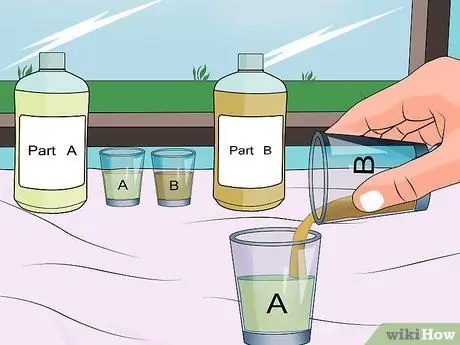
Step 3. Mix the plastic resin
The plastic resin consists of 2 parts which are labeled as “part A” and “part B”. The resin is formed by mixing parts A and B in equal ratios.
- Prepare 2 disposable plastic cups.
- Determine how much resin is needed to complete your project.
- Pour equal amounts of parts A and B into 2 different cups in a row.
- Pour the contents of cup number 2 into cup number 1.
- Toss with ice cream sticks.
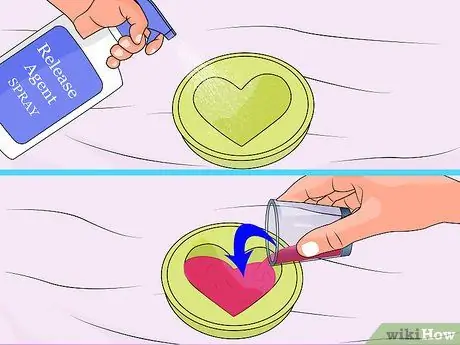
Step 4. Fill the mold
Pour the resin into the mold. To prevent air bubbles from rising to the surface, spray the top of the resin with a lubricant. Smooth and scrape off excess resin with a metal putty knife. Allow the resin to dry for the duration stated in the product instructions.
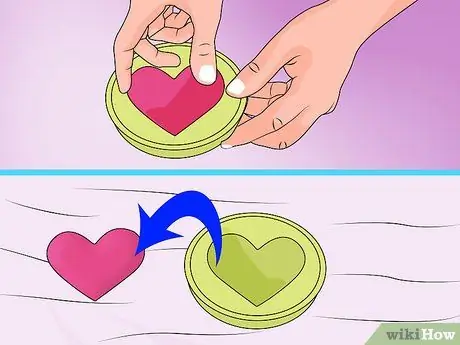
Step 5. Remove the main material from the mould
Once the resin has dried, you can slowly remove the main material from the mold. If you are using a ready made mold, a silicone mold, or a mold made from recycled materials, press the back of the mold with your fingers to remove it. If you are using a double-sided mold, remove the mold to remove the material inside.
Tips
- New molds are usually sold with a thin flour coating on the inside to prevent the material from sticking. In general, you will need to sprinkle with starch before storing the mold long term to protect it.
- Check with a liquid resin dealer to find out how much the material will shrink once it hardens. It's important to take this into account when you want to create an object of a specific size.
- You can speed up the drying process by using a hairdryer on a low setting. Do not position the tool in one spot - instead, move it back and forth in front of the plastic mold surface in a sweeping motion.
Warning
- Work in a well-ventilated area when mixing and pouring plastic resin.
- When creating prints, do not use copyrighted objects as the basis for prints. Some of the most common copyright infringements are usually related to cartoon characters. So, be careful.