Screen printing is a printing technique used to create identical images on various objects (generally on clothing). You make screens and stencils, then push the ink through the gauze onto a t-shirt, paper, or other object. The ability to screen print at home will allow you to create unique clothes and other items, and replicate as many designs as possible using the same screen.
Step
Method 1 of 3: Creating Screens and Frames
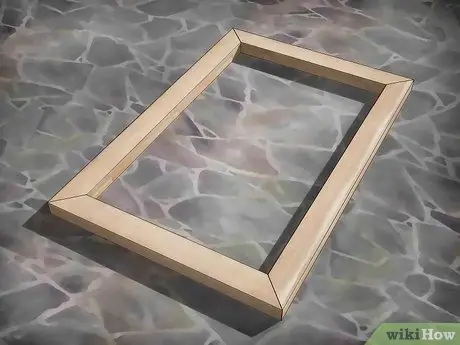
Step 1. Purchase a canvas stretcher frame at a book or craft store
You can use a simple and inexpensive frame made of wood to attach to the canvas. If you want to dig deeper, you can buy an aluminum frame which is more durable, as the wood frame will wear out if you keep washing it.
- Many craft shops now also sell half-finished silk screens, so you can buy a standard sheet if you don't want to make your own.
- Make sure the frame is large enough for your design. If you don't know which design to print, or you want to get a versatile frame for various designs, try to have a frame that is at least 25x40 cm.
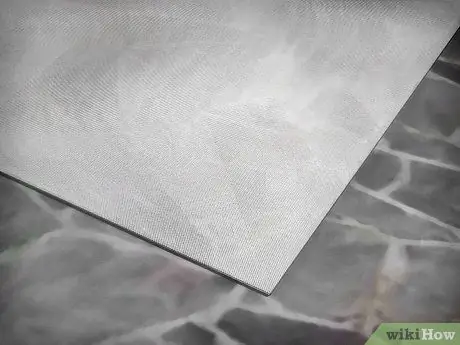
Step 2. Buy gauze
It's a good idea to get good gauze so the ink can penetrate into the shirt, paper, or design. The size of the mesh-count determines the looseness and tightness of the gauze. A high number indicates a tighter screen. The tighter the gauze, the more intricate the details. Mesh-count indicates the number of threads in 2.5 cm square.
- For a classic or college-looking “athletic” print that looks worn and grainy, look for a gauze with 85 mesh-count.
- For versatile gauze, look for 110-130 mesh-count.
- For printing on paper or plastic, look for gauze with a 200-250 mesh-count.
- In general, brightly colored objects work best with high mesh-counts. Therefore, if you are using white paper, look for gauze with a 230-250 mesh-count.
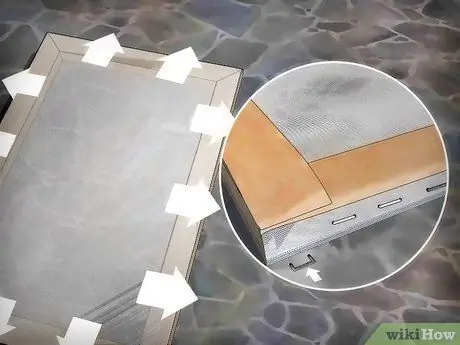
Step 3. Stapler the gauze to the frame
Make sure you pull the gauze tight before you start stapling. The gauze should be stretched, but not torn. Stretch the gauze around the frame and stapler every 2.5-5 cm.
- You may need an electric staple gun to hold the gauze firmly together.
- You can also use tacks.
Method 2 of 3: Creating a Design
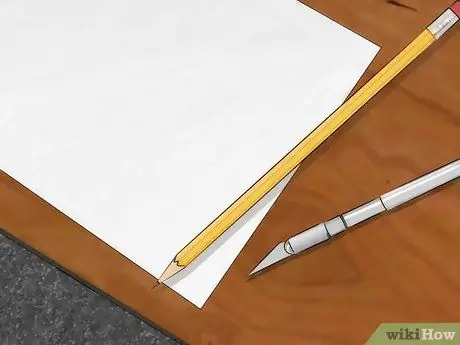
Step 1. Stencil your design
The silk screen can only screen print one color at a time. Therefore, create simple shapes or outlines to study. Whatever is drawn will eventually become the inked part of the print. To create your mold, you will need the following:
- Poster board, thin cardboard, or other thick, sturdy paper.
- Pencil
- X-acto knife or other precision knife.
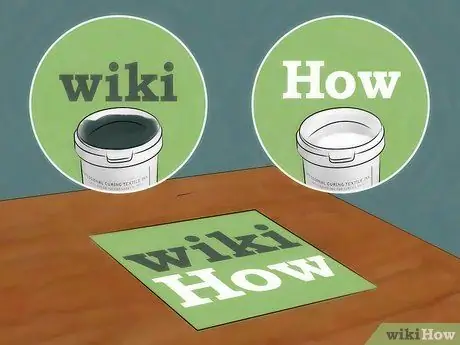
Step 2. Know the artistic limitations and challenges of screen printing design
Screen printing is not difficult to do because the end result is exactly what is drawn. However, there are some principles and limitations of screen printing to be aware of when designing your prints:
- You can only screen print one color at a time.
- High contrast images (eg black and white) give the best results because screen printing cannot create shading.
- For complex designs, you will need to make several prints, one for each color, and each one after the previous paint has dried.
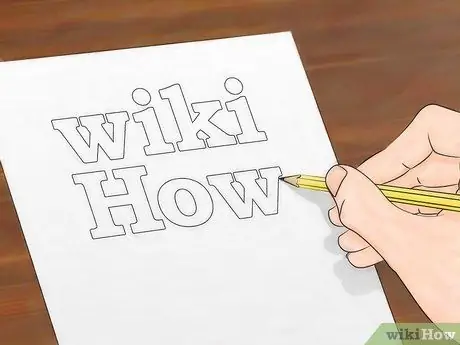
Step 3. Sketch the design onto the poster board
Draw the blocks of your design. You can use images from photos or other images uploaded to a photo editing program. To make it, make the image into a basic two-color outline, then print.
For example, to create a stencil in Photoshop you need a black and white image and click Image → Adjustments → Threshold, then adjust it until it is near the peak of the maximum height
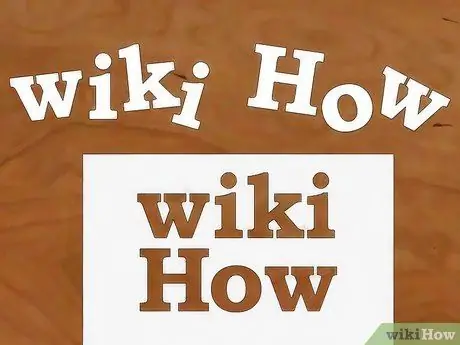
Step 4. Cut the design to be a stencil
All of the cut parts will be blank in the finished product, and anything covered by the stencil will be colored in ink. For example, you want to print a red bull's-eye (target) logo on a white t-shirt. When cutting the stencil, all the cut rings will be white, and all the rings that the stencil is covering will be red.
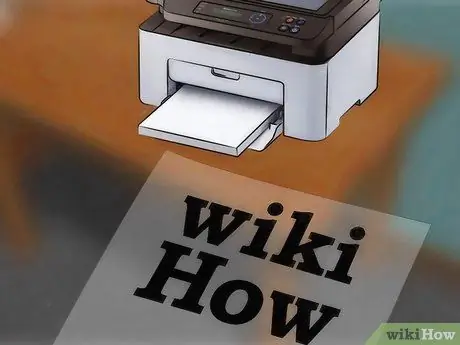
Step 5. Alternatively, draw the design on transparent paper
For complex drawings, the entire outline will be difficult to cut. Therefore, use black ink or transparent paper to make stencils.
Your stencils and drawings must block light, as this is what copies the design onto the screen and prints on the clothing or object. Anything covered by a stencil or black ink will not be exposed to light so it is left "open" and allows the ink to pass onto the shirt or object
Method 3 of 3: Printing with Your Screen
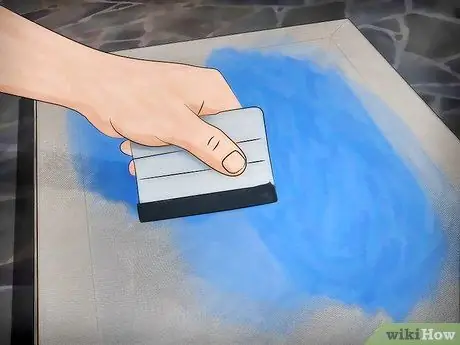
Step 1. Coat the silk screen with a thin layer of photo emulsion
Pour a layer of emulsion along one side of the screen and use a squeegee to spread the emulsion so that it becomes a thin, even layer across the screen. Photo emulsions react to light and harden upon exposure. Therefore, anything that is not covered by the stencil will turn into a barrier that prevents the ink from passing through.
- Emulsify the flat side of the stretcher, not the side surrounded by wood.
- It's best to do it in a dark room to prevent the photo emulsion from hardening before you're ready.
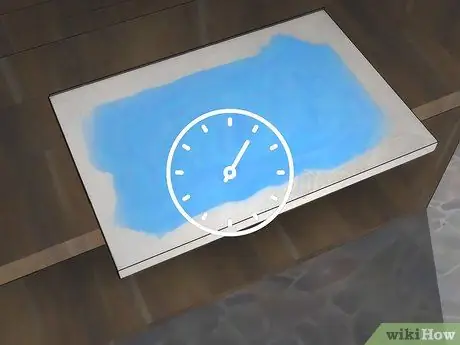
Step 2. Let the emulsion dry in a dark room
Try not to be exposed to a lot of light. A closet or bathroom is an ideal location, as long as it has curtains that can be closed.
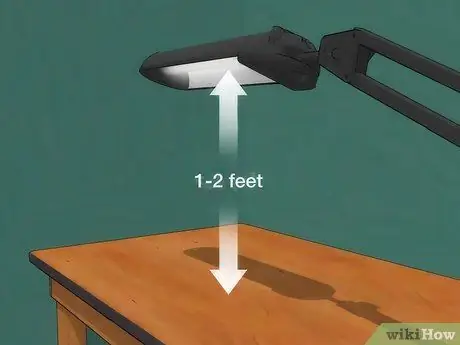
Step 3. Set the “light exposure area” while waiting for the emulsion to dry
You will be required to dry the emulsion in strong, direct light. Follow the specifications on the photo emulsion packaging, and adjust the light exposure on your flat black surface. Each emulsion has a different time, wattage, and distance to harden properly. Therefore, be sure to read the packaging before starting. The lamp should always be 30-60 cm above the emulsion.
If the instructions say 30 minutes at 200 watts, install the 200W lamp 30-61 cm on the table. Your screen hangs in the sun
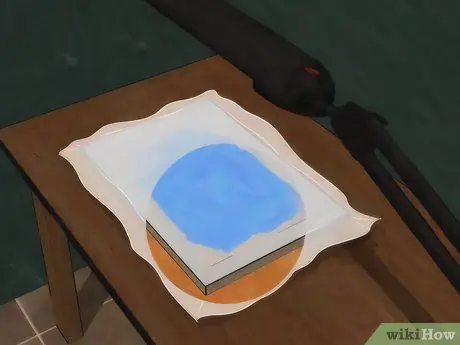
Step 4. Place the screen under the light exposure area
Cover the screen with a towel before moving to avoid accidental exposure to light. Place it under the drying area and don't lift the towel just yet.
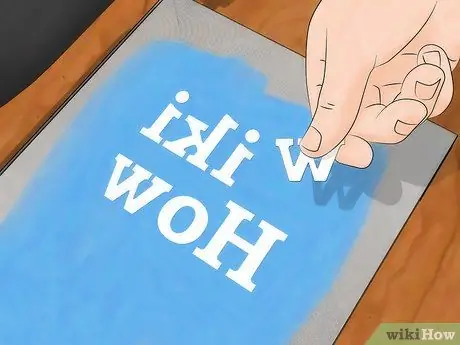
Step 5. Place the stencil upside down in the center of the screen
The side of the emulsion must face on. The gauze will be lifted a few inches from the table and against the frame. Place the stencil in the center of the screen with a distance of 10-12.5 cm between the design and the edge of the frame.
- You should place the stencil in the “upside down: position to get the correct image. Position the image on the stencil according to the desired finished result, then flip it over before placing it. Otherwise, you will get a “mirror” image of the desired print
- If there is a gust of wind, or the stencil is very light, place a piece of glass on top of the stencil so it doesn't move.
- Do not press, push, or move your screen, light, or stencil while it is drying.
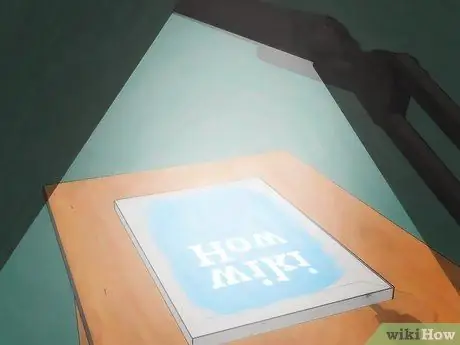
Step 6. Turn on the light for the recommended time
Just follow the instructions on the emulsion bottle and remove the screen when you're done. When finished, remove the stencil and set it aside for later. If you smell burning during this process, turn off the lights immediately.
If you prepared the emulsion properly, you will see a faint outline of the stencil inside the emulsion when the design is removed
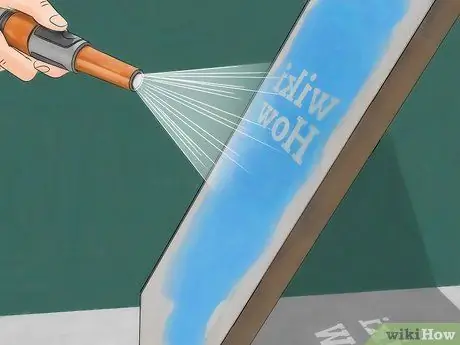
Step 7. Flush the emulsion with cold water
Use a powerful water source (shower, faucet, or hose) and wash your screen by focusing on the image. The water will rinse away the non-hardening emulsion around the design. You will see the outline of the stencil appear. Keep flushing until you can see the image well.
Allow the screen to dry before moving on to the next step
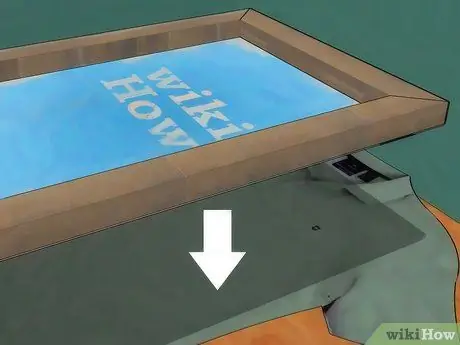
Step 8. Layer the screen over the object to be printed
The gauze should touch the object to be printed, such as paper or a t-shirt.
If you're using a t-shirt, tuck the cardboard inside the t-shirt to prevent the ink from penetrating the inside of the t-shirt
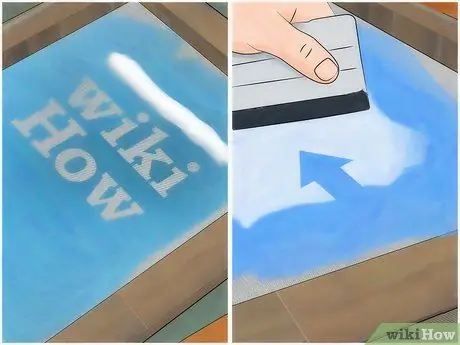
Step 9. Apply some ink over your design to create a thin layer of ink just above the design
Then, slide the squeegee firmly over the design so that the ink coats the entire stencil.
The harder you press, the darker the image will be
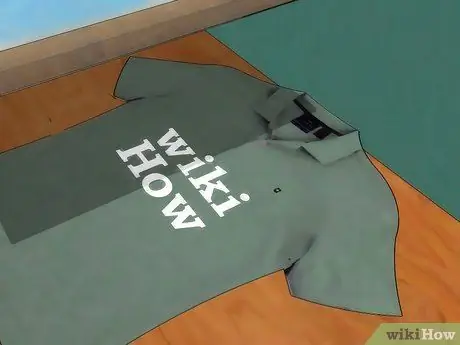
Step 10. Pull the silk screen slowly
Pull the screen off the shirt/paper evenly, then hang the shirt to dry. Your design will be printed.
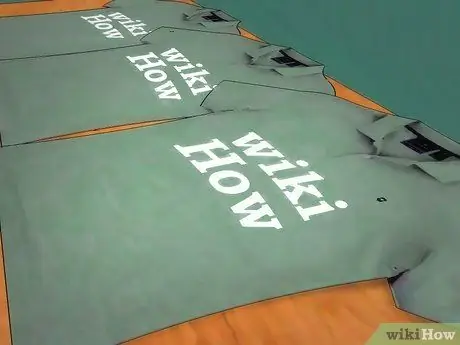
Step 11. Repeat on as many shirts as you want, and wipe the screen occasionally
You can use the silk screen again with another shirt, if you want. Simply wipe the back of the screen after use on a single shirt, and add the ink again. If you use the same mold several days in a row, rinse and dry at the end of each day.
Tips
You can use semi-finished screens at a craft store, but they vary in price and can be quite expensive
Warning
- Always wear gloves and cover your work surface with newspaper or plastic when using permanent ink.
- Do not allow the ink on the screen to dry because later the screen cannot be reused.
- Do not choose a design that is too detailed. The results may not be as good as you expect.