A torque wrench (also known as a torque wrench) is a specialized tool for repairing vehicles and some construction buildings. Once calibrated, this tool provides "torque" or rotational force to tighten bolts or nuts more easily and accurately than using a regular wrench.
Step
Part 1 of 3: Preparing the Project
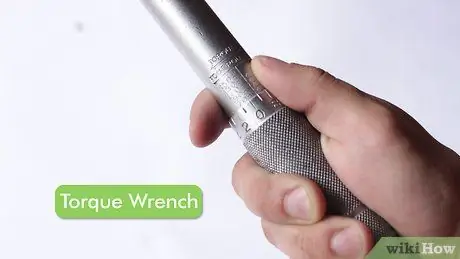
Step 1. Purchase a torque wrench that is ensured to be calibrated
Buy it at a repair shop or dealer. If you buy a used torque wrench, take it to a repair shop for calibration.
- There are four types of torque wrenches: directional, click, dial, and electronic digital. The main difference between the four is the way they are read and the level of ease of adjustment.
- If you want a cheap and easy-to-use torque wrench, choose the needle type.
- If you prioritize accuracy and repeatability, choose the click type.
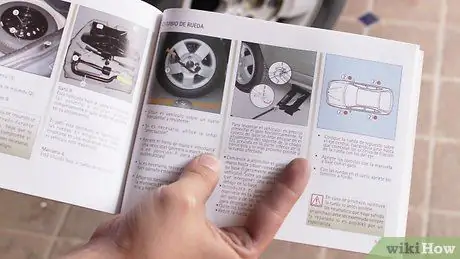
Step 2. Research torque specifications for the project to be worked on
Usually recommended sizes are listed in Nm units. For example, a wrench may state whether a 5 or 25 Nm size is recommended for a specific bolt or nut.
- If you don't find the specifications in the instructions, look for this information online.
- Pay attention to the pattern the guide suggests for tightening the lock. For example, a star pattern or starting from the middle and alternating between the two sides.
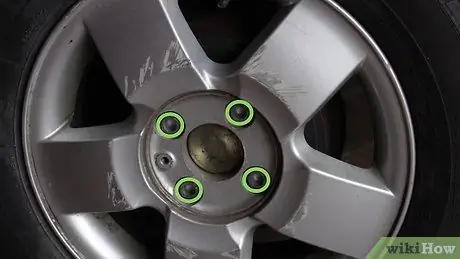
Step 3. Make sure you use clean, dry and undamaged bolts and nuts
Torque will not work properly on a broken groove. Opening fasteners can cause problems later on.
Do not lubricate the grooves beforehand as this will reduce friction and increase bolt load
Part 2 of 3: Using the Torque Dial Lock
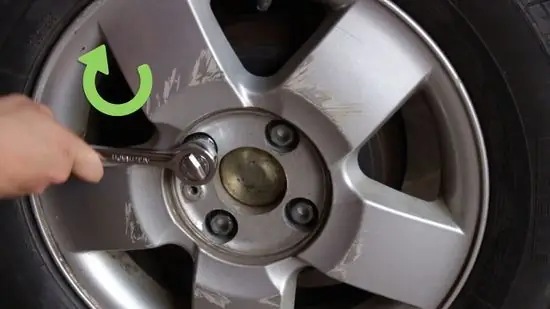
Step 1. Tighten the bolts in the grooves with a wrench or socket until they are firmly in place
Then, you can continue with the torque wrench.
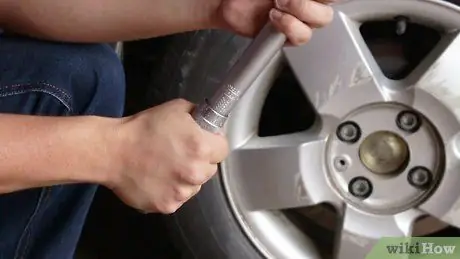
Step 2. Grasp the plastic handle of the torque wrench
Hold the handle so that it is centered on the pivot. To be accurate, both ends of the blades should touch the blade.
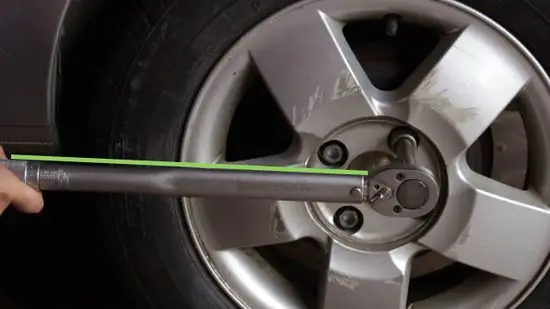
Step 3. Place the end of the torque wrench and position yourself comfortably so that you can read the needle directly
Don't look at it slightly tilted.
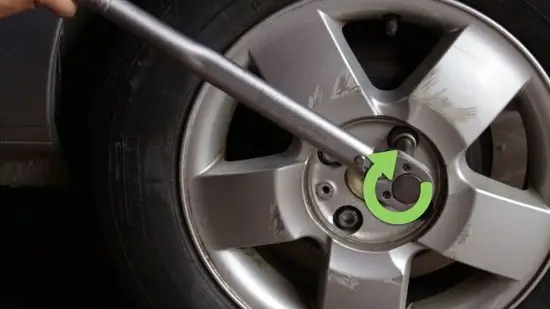
Step 4. Tighten clockwise until it reaches the recommended torque
Tighten any other fasteners recommended by the guide using the same technique.
Part 3 of 3: Using the Click Torque Lock
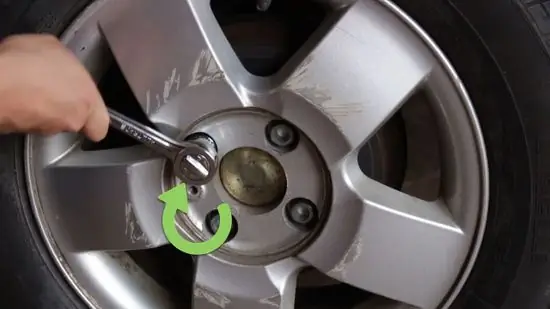
Step 1. Tighten the bolt into the groove using a wrench or socket until it is tight
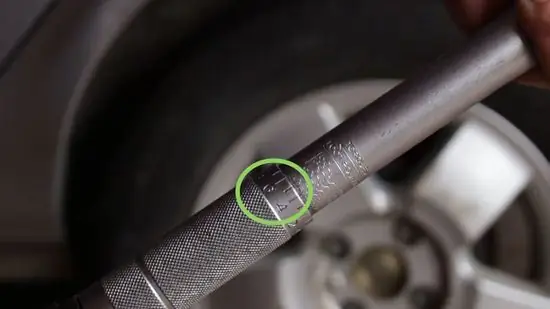
Step 2. Adjust the torque wrench until it fits
Loosen the dial by turning the handle until it reaches the recommended torque specification. After that, tighten the dial.
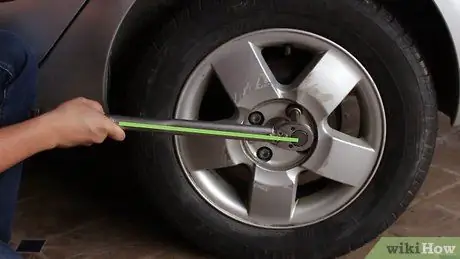
Step 3. Hold the handle
Place the end of the fastener with the handle on the left side.
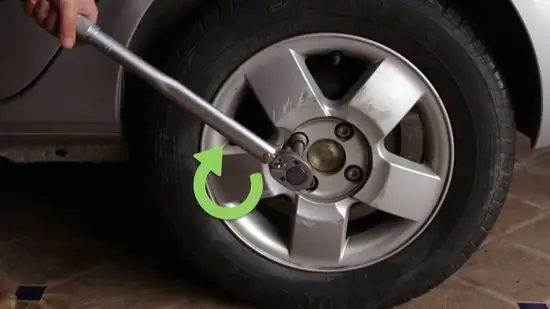
Step 4. Rotate clockwise you hear a click
Repeat on that handle until you hear a click to make sure the suggested force is reached.
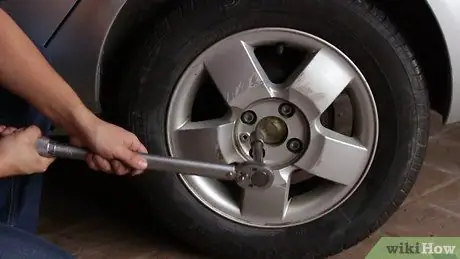
Step 5. Continue to tighten all the fasteners according to the suggested pattern
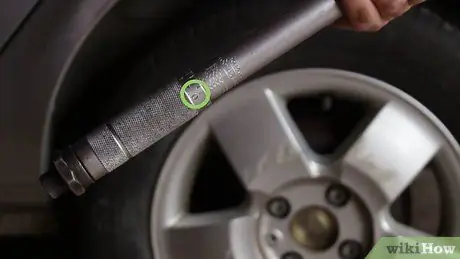
Step 6. Reset the torque wrench to zero when it's finished
This will reduce the internal spring pressure and help it calibrate.
Tips
- Digital electric and dial torque wrenches are the most accurate types, but they are both quite expensive. If your livelihood does not rely on this tool, you should not waste a lot of money buying it.
- Do not drop the torque wrench. This wrench is a special tool and if it is not properly cared for it will not calibrate properly. If so, the lock will need to be adjusted at the workshop.
- Pay special attention when tightening wheel bolts on tires. The rod can break if the bolt is too tight. On the other hand, if the bolts are not tight, they can loosen. If they are not tightened evenly, the grooves on the bolts will be uneven.