Restoring a car engine is a tough task, but smart planning for engine restoration will save you from costly mistakes, saving you time, effort and emotion. Learn how to disassemble and install your engine block, as well as how to disassemble and inspect components to restore your car's engine to like new, or to modify it for maximum performance. See step 1 for more details.
Step
Part 1 of 5: Remove the Machine
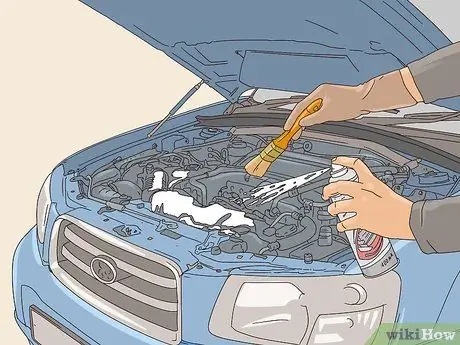
Step 1. Clean the machine thoroughly before starting work if possible
Accumulation of dirt, soil, oil will make the process of unscrewing bolts and removing components more difficult and messy.
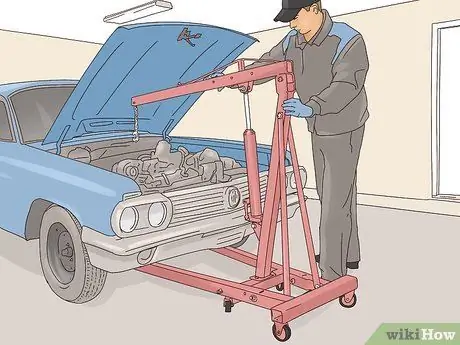
Step 2. Position the car near your pulley
You need to work on a flat, well-lit surface, with enough room to place your pulleys as you move around them. If you have a large enough garage, even better.
It is best if you take close ups of the various components of the machine as much as possible from different angles. The next time you work, this will be very useful. You can even print it out and bookmark it for later reference
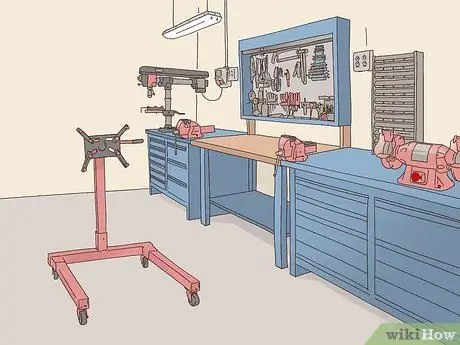
Step 3. Set up your workplace before you start
Containers for storing bolt nuts, clamps, a workbench for placing tools, buckets for watering and cleaning components will make your job easier.
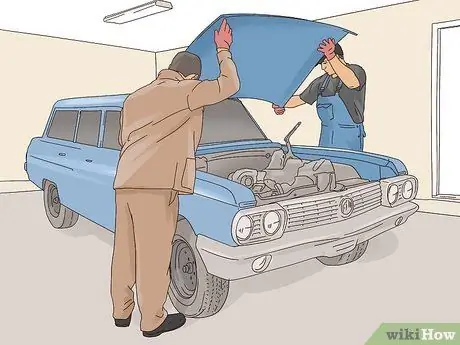
Step 4. Remove the hood
Mark the hinge bolts so you can easily reattach them later. Release it slowly, ask your assistant to help release it and keep it until the job is done. Note that some hoods have electrical connections for lighting or headlights, turn signals and fog lights built into them. They too must be released.
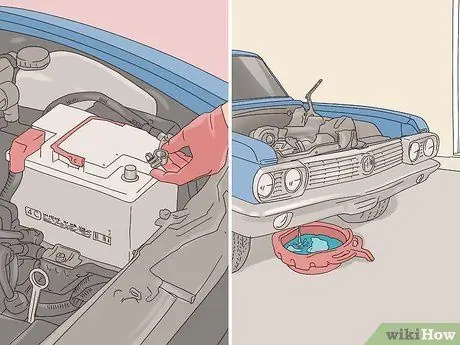
Step 5. Start by removing the external components from the machine
Disconnect the ground connection on the battery before doing anything else, drain the radiator fluid and hoses to ensure your safety. Be careful not to damage the metal clamps, which are hard to replace compared to rubber hoses which may break when removed.
- Remove the radiator fan and cover, if any, be careful, because the aluminum fins on the radiator are easily damaged.
- Next, remove the alternator, fasteners, cooling fans and belts. Remove the air inlet and fuel hose. Some cars use a pressurized fuel system even when the engine is off. So prepare to dump that fuel and release the pressure before opening it. When you unscrew the power steering pump and AC compressor, do so without removing the hoses so you save time putting them back together.
- It's a good idea if you're drawing or photographing, as well as labeling hoses and cables with insulation and markers. Don't just rely on your memory. Some cables and hoses can only be installed in one direction, but some are not very clear. You may need to make diagrams, drawings to make reassembly easier.
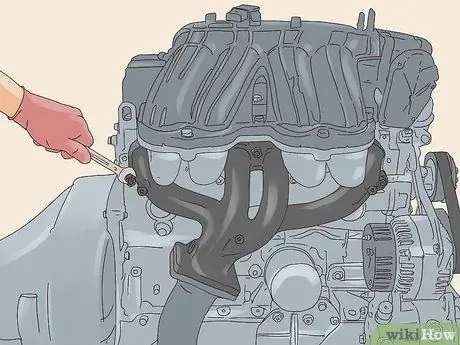
Step 6. Disconnect all electrical connections on the machine
You can keep the spark plugs in position, but first remove the exhaust and disconnect all electrical connections to the transmission before removing the transmission.
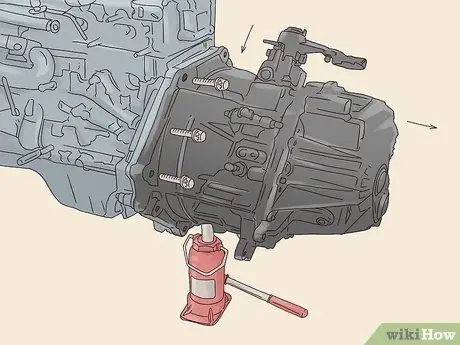
Step 7. Remove the bolt that holds the transmission hump on the engine
Jack up the car and place it on the jackstand, then hold the transmission with the other jackstand on the bottom. It is very important to use a jackstand or other support under the transmission before you remove the bolts. Once you remove the bolts, there may not be anything else to hold the transmission so it can fall if you don't hold it in. For cars with more sophisticated crossmembers, this is not a problem.
In general, the transmission does not need to be removed from the car, as long as the transmission can be properly supported when the engine is removed
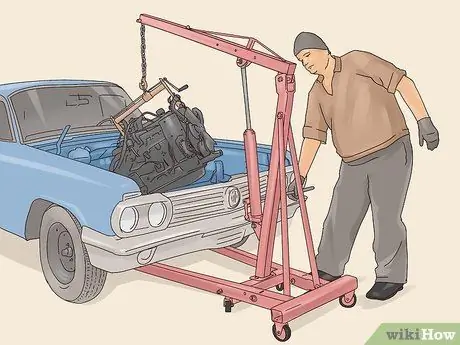
Step 8. Use the pulley to lift the machine
Connect the pulley to the engine at the lift point on the cylinder head, or to the largest bolt near the top of the engine, and adjust the height to start lifting the front.
Be careful. Lift and slide the engine away from the car, avoiding hitting the car body, and lower it on a flat surface to begin disassembly and inspection
Part 2 of 5: Inspecting and Disassembling the Engine Block
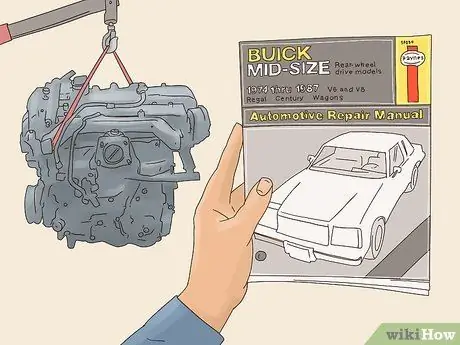
Step 1. Get the manual for your car
No explanation can give you all the specifics needed to restore each type of machine, so it's important that you always stick to the manufacturer's manual.
Even if your car is quite old, manuals are usually available on eBay for a fairly low price, and are often available at public libraries that you can borrow for free. If you want to invest in this work, it is very important that you have this manual so that you can learn the correct specifications and essentials of your machine
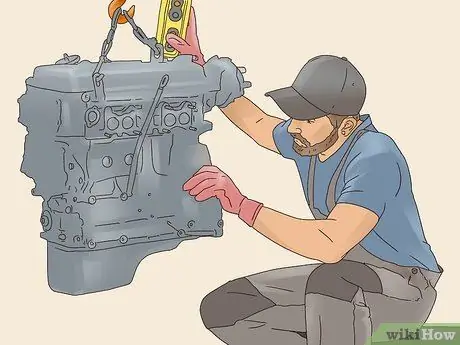
Step 2. Perform a visual inspection of the machine
Check the fluid that appears on the spark plugs, gas pump connections, connections between components. Inspect the vibration balancing pulley for signs of cracking, indicating it is time for replacement. Check for signs of overheating, cracks in the engine block. Also check for any residual gasket seals left over from previous work.
Also, check the identity and machine number, make sure the machine you are disassembling is yours. Engine swapping is not uncommon, and each engine has different specifications
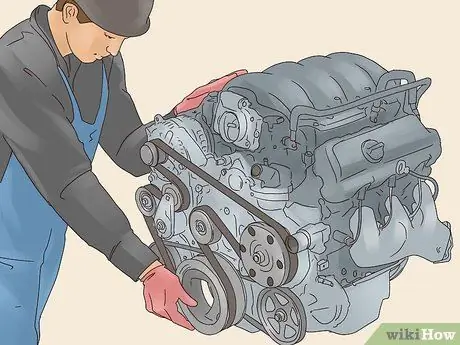
Step 3. Check the external components on the machine
Check for signs of loose distributor, by pressing it. Check the alternator belt for wear by turning the pulley and listening for any strange noises. Also check the clutch for wear.
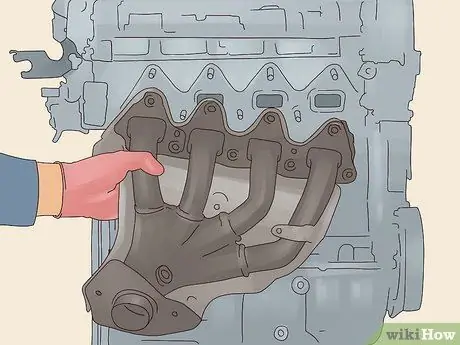
Step 4. Open the exhaust duct if it has not been opened previously, to make it easier for you to remove the engine compartment
The bolts in the exhaust can be very rusty. Be careful when removing it, don't damage it. Spraying with lubricating fluid will help. And bolts that are very hard to unscrew may require heating to remove them.
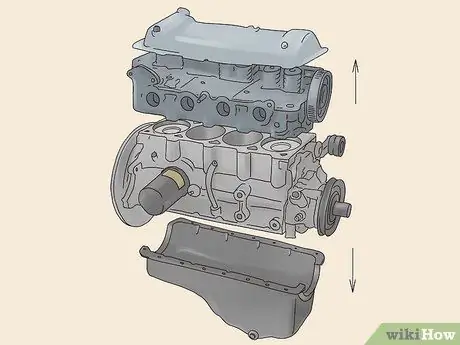
Step 5. Begin to disassemble all parts of the machine
Start by opening the oil sump and valve cover, then the cylinder head. Be sure to protect the lifting guide rod portion when removing the cylinder head. If they get bent or damaged, they need to be replaced.
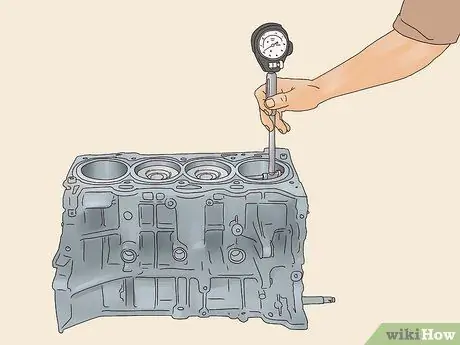
Step 6. Check the cylinder diameter
Maybe you need a micrometer to measure it. Highly worn cylinders may hinder you from maximizing restoration. If you know that your engine has not been restored before, you can estimate cylinder wall wear by looking at the top edge of the cylinder. This is the recess where the piston reaches its highest point, just below the recess. If the recess feels deep, then the wear is quite high, but if you don't feel a recess, then the cylinder is still good. In general, if the wear is below 20/1000 inches, the original piston can still be used, but if it is more than that, then you need to oversize the cylinder and use an oversized piston size.
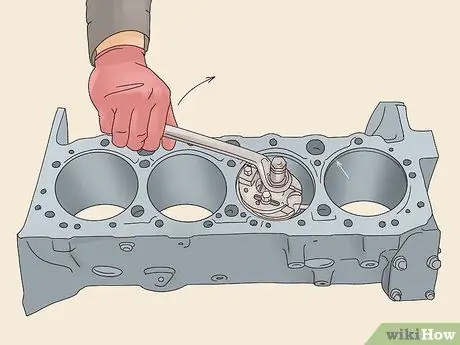
Step 7. Remove the recess at the top of the cylinder using a file
The recess is the point where the cylinder does not wear out because the piston does not reach that place. The recess needs to be removed before removing the piston to prevent piston damage, and to make it easier to reassemble with a new piston ring.
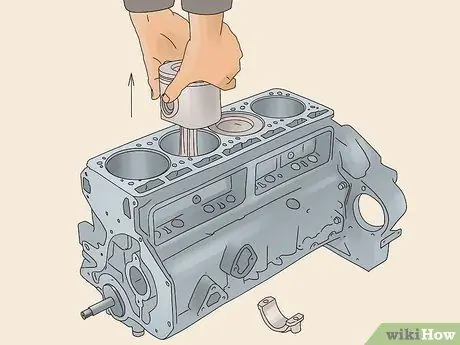
Step 8. Remove the piston and handlebars
After removing the piston head, place the piston handle guard on the end of the handlebar, so that the tip of the handlebar does not hit or scratch the cylinder wall on the engine block during removal. You can use a cut rubber hose for this, slipping it over the end of the piston. Once it is removed, re-install the handlebar heads according to their respective pairs, giving a mark to make it clear, from which cylinder each piston handlebar comes from. It is important to maintain the existing balance.
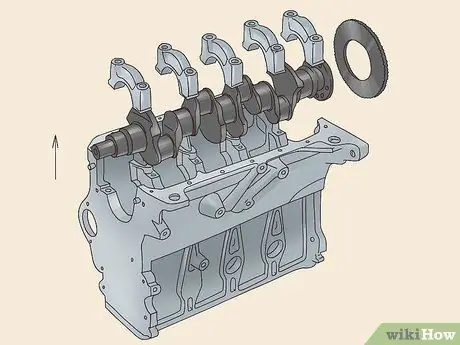
Step 9. Remove and open the crankshaft
Once removed, place it in a safe place, even better if you place it on the crankshaft holder so you can inspect it more closely. Keep the bearings in their original order, checking for wear and excess dirt. With the crankshaft removed and placed in the correct position, reassemble it on the engine and tighten to specification.
Remove the existing camshaft, balance shaft, spacer rings, make sure they stay in order because you will have to put them back in the correct order. Open the valve bearings, pay attention to their position
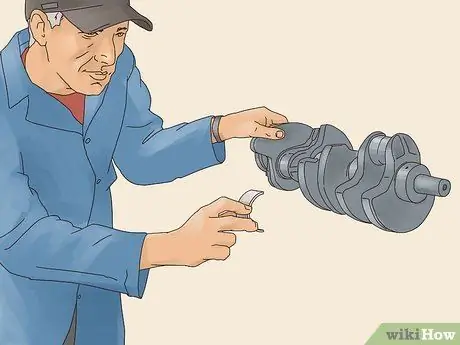
Step 10. Visually check the crankshaft
Look for cracks or signs of overheating. Measure the dimensions. Ukudan can include the axle, outer circle, taper and run out. Compare this size with the specifications in the manual.
- If the crankshaft is out of specification, mark it for identification, and send it to a lathe repair shop to resurface it and reshape it into a "circle". If the shaft is rotated, note on the parts that all must be prepared according to the new size of the axle.
- Once the lathe has reshaped the shaft, you can use a long brush to clean it of any remaining oil flow. Then measure the crankshaft again so that you can slide the bearing to get the distance from the shaft to the bearing according to specifications.
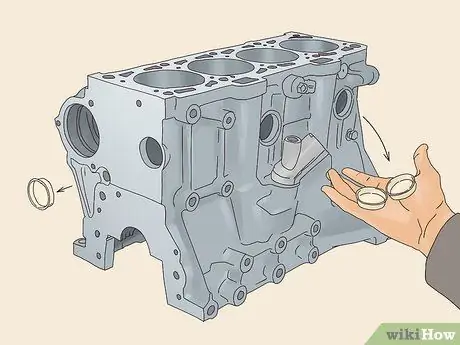
Step 11. Complete the disassembly
Remove the core cover, brackets, guide pins and anything that is still attached to the outside of the engine block. Visually check the engine block for cracks.
If you want, you can use magnaflux on the engine block to look for leaks. Magnaflux is only used to look for leaks in cast iron. Use colored penetrant to look for cracks in the aluminum engine block. Usually the repair shop will do this check, and may also check with pressure on the engine block and cylinder head. You can ask them to "boil" the engine block and cylinder head to clean it
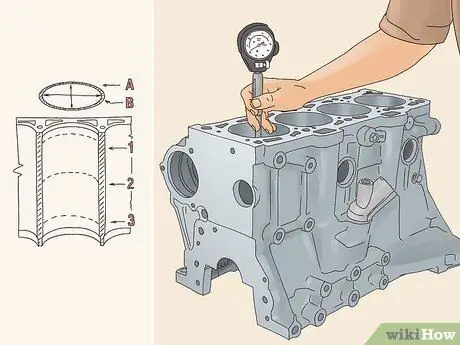
Step 12. Measure to specifications
It's best to do this in a workshop, but if you have the tools, you can use a straight edge and a set of slit gauges to check the level of the surface. measure diagonally and horizontally, If the surface exceeds the specification for flatness, it needs to be smoothed again. Be careful when removing it, not too much because there is a risk that the piston head will hit the valve.
Using a dial bore gauge, check the level of evenness of the circles of each cylinder. Check for any discoloration of the cylinder. Use a rigid stone hone to check for wrinkles on the inner surface of the cylinder
Part 3 of 5: Disassembling and Inspecting the Cylinder Head
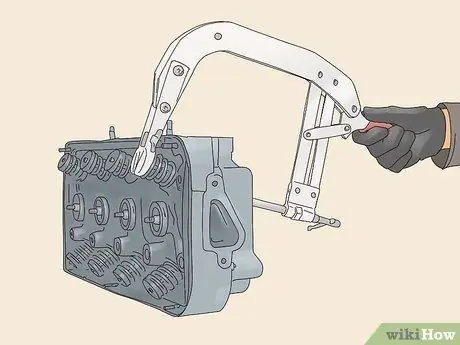
Step 1. Use a valve spring press to tighten the spring
While the spring is pressed, release the valve handle and slowly release the pressure on the spring. Once you have removed the press, remove the springs and spacers. Store neatly.
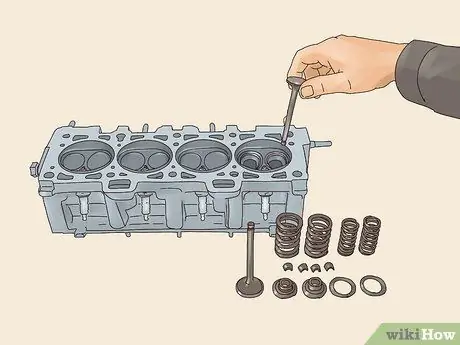
Step 2. Remove the valve from the head
Do not force it because it can scratch the guide. You will need to remove any residual carbon and debris from each valve, if possible, do a valve skid at a repair shop, or use magnaflux or colored penetrant to look for cracks.
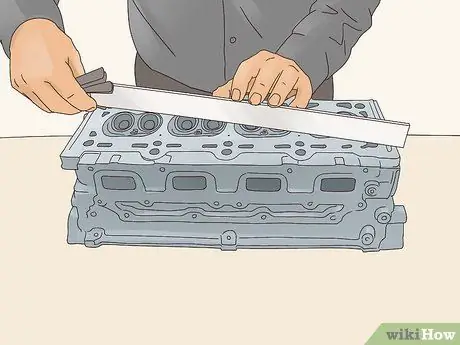
Step 3. Check the flatness of each valve head
Mark any uneven valves and smooth them out at the workshop, after inspection. Check for wear on the guides using the rotary indicator and check for wear on the valve seat. It is also important to check: Check each valve head for flatness. Note any flatness which is out of specification so that it can be corrected at the machine shop after inspection. Inspect the guides for excess wear using a dial indicator and check for recession of the valve seats. It's also essential to check for:
- Worn valve valve.. Use a micrometer and replace valve valves that are worn beyond specifications.
- Worn keeper groove. Replace worn keeper.
- Wide playing distance. The clearance should be narrow at the intake valve compared to the exhaust valve. Replace the valve that has a large clearance.
- Length, spring power and neatness. Replace a spring that has worn beyond specifications.
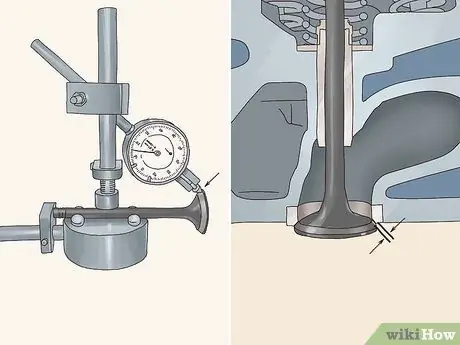
Step 4. Repair worn valve guides
Replace the valve seat, and re-smooth the valve surface that will not be replaced. Lubricate the valve with engine oil. install valve seal.
There are 3 kinds of valve seals, band, umbrella or PC. Pay attention to the order of installation. Install the valve head. Check for leaks using a liquid or vacuum, or do this at a lathe shop
Part 4 of 5: Replacing the Engine Block
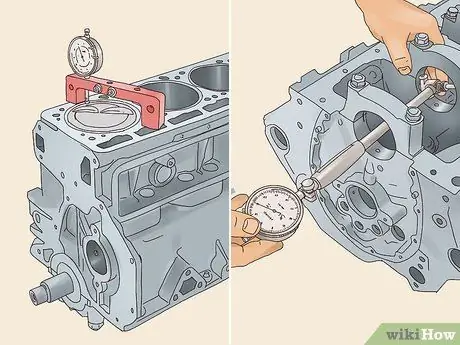
Step 1. If the engine block has been removed, check the size again
Lathes may make mistakes, but it's your job to check them out. Check that the oil lines and lubrication openings in the engine block are clean and free of scrap metal.
Clean the engine block with hot soapy water, then blow it completely dry to remove moisture. Blow all bolt holes with a compressor to remove dirt before installing bolts
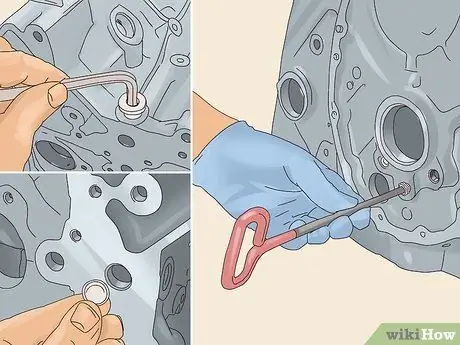
Step 2. Oil all components
Install the oil line cover and core cover using the hardening seal. Do not use silicone seals in these areas as this will melt and cause rubber deposits in the lubrication system.
Prepare to lubricate the main bearings, wash and dry them. Lubricate the inside of the bearing and the lip of the seal using the manufacturer's recommended grease. Then install the main bearing and the main rear seal, making sure they are positioned correctly
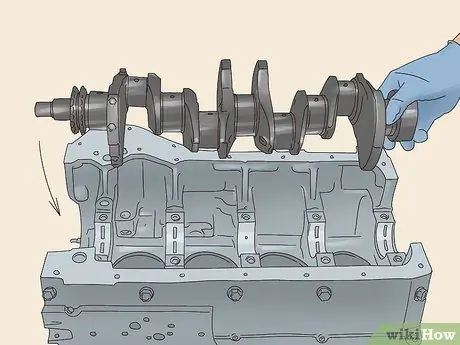
Step 3. Install the crankshaft and main cover
Oil the crankshaft with high pressure grease, then install. Since the cam cap is sensitive to its position and direction, insert the cap and tighten it from the inside first and then the outside.
Turn the shaft to see the rotation If the shaft rotates smoothly, then check the final rotation
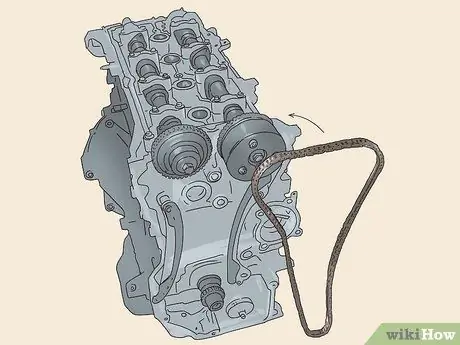
Step 4. Install the timing chain or timing belt according to specifications
Be sure to adjust the timing marks correctly during installation and adjust the cam angle.
To adjust the cam angle and timing, align the timing mark at the top dead center and adjust the angle correctly, with the crankshaft/timing poison and the correct timing sequence for the intake, compression, power and exhaust stroke sections of the engine
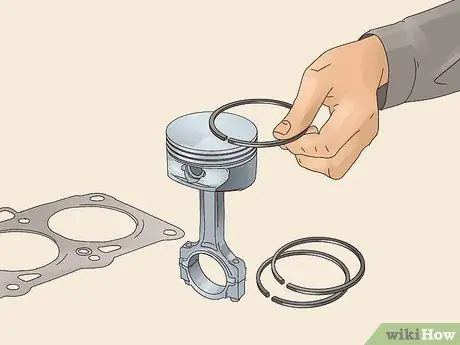
Step 5. Install new pistons, rings, gaskets and seals
Check piston rings and clearance according to manufacturer's instructions. Maybe you need to use a larger/oversized ring. If the ring diameter is too small, then the piston will have a wide playing distance, but if it is too large then the distance will be too tight, and it can fold and even break when the engine is hot.
When you install, you must arrange the ring on the top of the piston. The narrow slit in each ring is rotated 180 degrees around the piston against the next ring to reduce the possibility of leakage. Make sure the oil spreader ring is installed properly
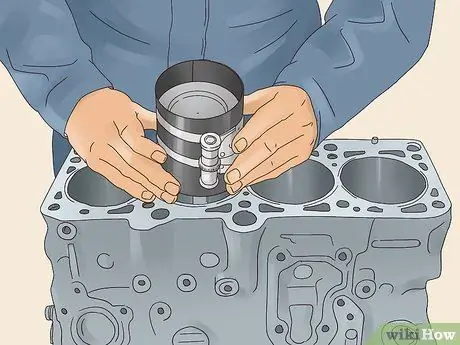
Step 6. Install the piston and handlebar
Use a handlebar guard and lubricate the handlebar section, first slowly insert it and then tighten it gradually in 3 stages to make sure everything fits properly.
Continue turning the crankshaft again after installing and tightening the pistons and tightening the handlebar caps as necessary to ensure smooth rotation. If it's hard to turn, you'll notice that the last piston in the cylinder or the piston handlebar entry has collided-- the halves must be inserted flush with each other. Test the shaft by turning after all bearings are installed
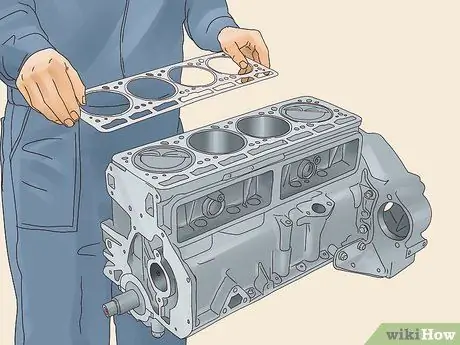
Step 7. Install the cylinder head gasket
Gaskets can only be installed in one direction, so make sure they are installed correctly. Remember to put the cylinder head on the engine block bolt or the OHC belt won't turn and then tear. Only use "cement gaskets" if the manufacturer recommends it.
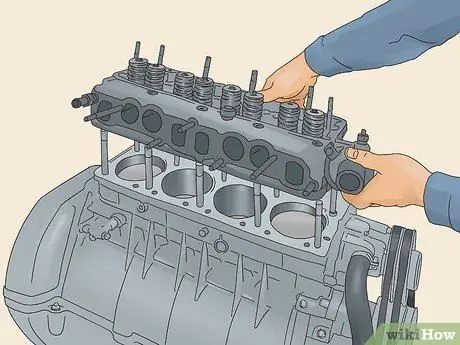
Step 8. Install the new valve head
Lubricate the bolt threads with the manufacturer's recommended oil or sealer, then tighten them gradually in 3 stages according to the manufacturer's recommended pattern. Pay attention to the size and position of the bolts.
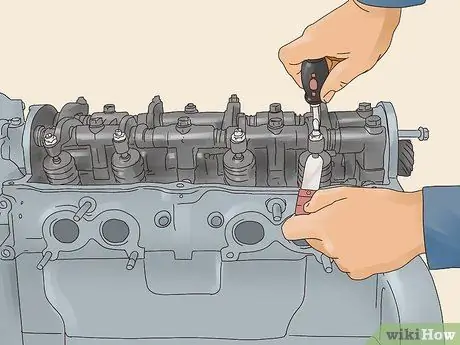
Step 9. Install the new valve controller
Be sure to lubricate this part when installing it, and adjust it as necessary. Use minimal up and down motion, and tighten in 3/4 turn.
Part 5 of 5: Reassembling the Machine
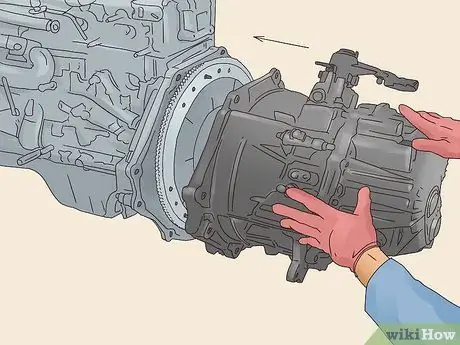
Step 1. Complete all the necessary work in the restoration
If you're doing a complete overhaul, it's likely that you need to do something else while you have the chance. Maybe you don't want to combine your new engine with a transmission that has traveled 200,000 miles. Maybe you need to do:
- Transmission installation
- Replacing the air conditioner
- Replace the radiator.
- Replace the starter motor
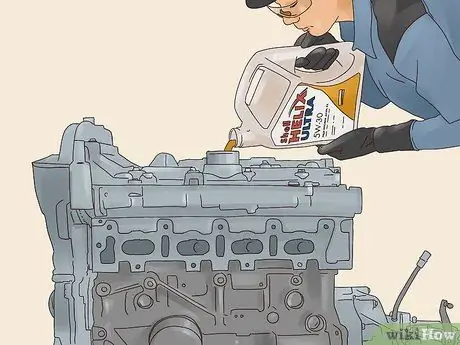
Step 2. Set up the machine
Fill the oil filter with engine oil before installation and with the oil recommended by the manufacturer. Let the oil flow by turning the pli pump manually. Fill the radiator with a mixture of antifreeze coolant and distilled water in a 50:50 ratio. You may also need to install:
- New spark plug according to manufacturer's instructions
- Distributor cap, rotor and spark plug wire
- New air filter, PCV. valve
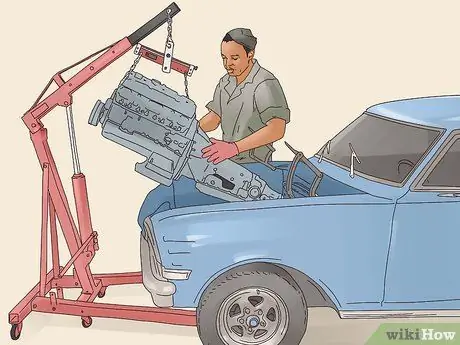
Step 3. Lower the machine with the pulley
It is important to keep the machine flat during installation. Be careful and ask for help. fasten on the engine mount bracket and reinstall all pipes, hoses and cables, making sure they are compatible with the newly installed components. Replace the radiator and hood, making sure there are no objects that can melt in the exhaust.
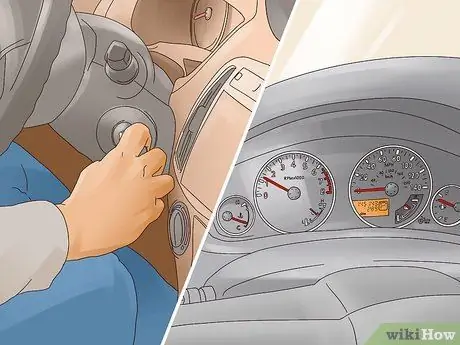
Step 4. Start the initial startup process carefully
Install the handbrake and block the wheels before starting the engine. Try starting the engine. If the engine won't start, check the fuel line.
Always check the engine oil pressure and temperature instructions. If you see full oil pressure, stop the engine immediately check for leaks. If you notice anything unusual, turn off the engine immediately
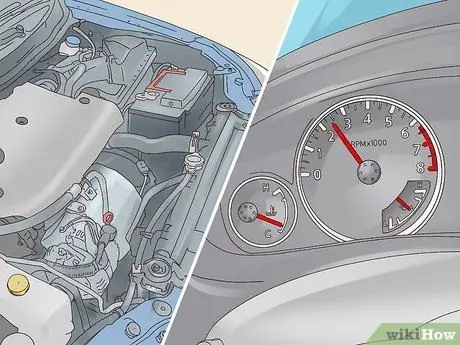
Step 5. Leave it on for a while
After the engine is running steadily, increase the speed to 2000 RPM to distribute the oil on the crankshaft. Run the car at a speed varying between 1800-2000 RPM for at least 20 minutes.
Open the radiator cap to check the water flow before it gets too hot. Check if the battery charging is running normally
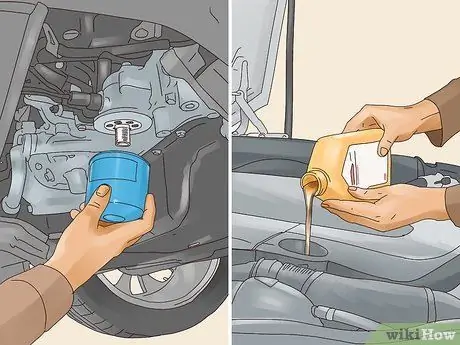
Step 6. Change oil and filter after 100 miles
It's important to keep the engine in good shape early on, and it's normal for you to change the oil every 100 or 200 miles at first, and then every 1000 miles for the first 3 months.
Warning
- Do not try to restore the machine without complete tools and sufficient knowledge. There is no specification number listed here because each car manufacturer makes the engine differently. It is very important that you have your car's engine manual if you want to restore it.
- Real professionals use micrometers and dial bore tools and calculate playing distances with precision. Don't skip this item.
- Don't use cheap bearings. Each engine is color coded for bearings and pistons, and each bearing and piston is a different size. Read the instruction manual for more details.
- If buying a new bearing, do not use the original size, as you could damage the crankshaft. If one of the axles is bad, it is better to turn the shaft and use a 0.25 mm bearing, from end to end.