Batik is a typical process from the island of Java to make designs on cloth using wax. After the fabric is painted with the wax design, it is dipped in the dye so that only the areas where there is no wax are dipped. Batik makers can create intricate designs by layering colors and using wax to create fine line details. While you may not be able to fully master it, you will get amazing effects using just a few materials and creativity at your disposal.
Step
Method 1 of 3: Batik Basics
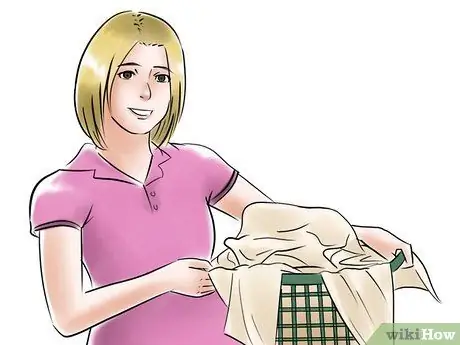
Step 1. Wash the cloth
Use hot water to wash the fabric and use a detergent (such as “Synthrapol”) to remove chemicals and dirt that can affect the dye.
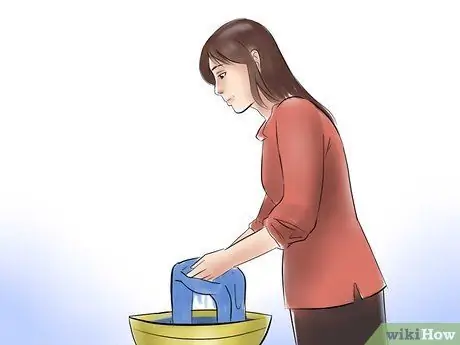
Step 2. Dip your fabric in the base color
The base color is the color that will appear under the candle.
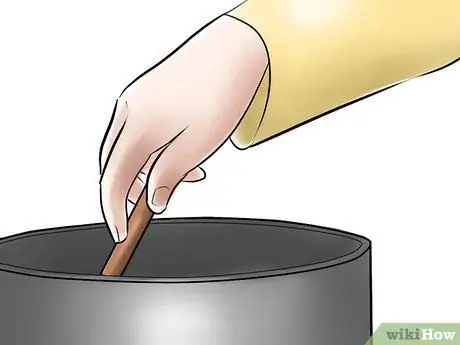
Step 3. Melt the wax
Batik wax is a stone that needs to be melted with an electric pot for candles or a double boiler.
- Be careful with hot candles. Do not heat the candle above 115°C as it may emit smoke or even burn.
- It is not recommended to heat candles on the stove. The wax pan and double boiler heat the wax slowly and at a lower temperature.
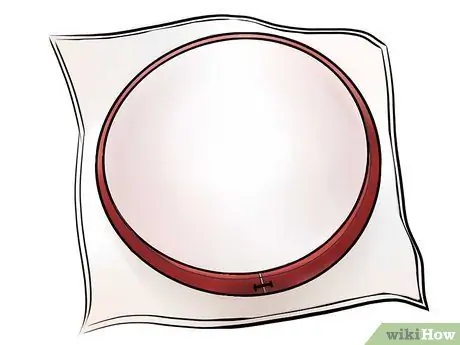
Step 4. Spread the fabric on the embroidery hoop
The hoop will keep the fabric stable and firm, so you can use the wax with greater precision.
If you're designing on a wide piece of fabric, you can lay newsprint or cardboard on top of the fabric without spreading it on the hoop. The wax will soak into the fabric, so the surface under the fabric needs to be protected
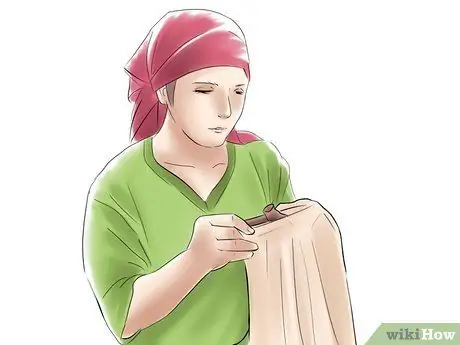
Step 5. Start using the wax with the tool
Different tools will produce different line qualities. Therefore, it is advisable to experiment first.
- Use a single-hole canting to draw thin lines and designs. Canting is a multifunctional tool and has a variety of hole sizes.
- Canting with double holes is used to draw parallel lines and draw larger areas.
- Brushes can be used to draw larger areas. Brushes can usually be used to make broad strokes or as a tool to create a dotted pattern.
- Use stamps to create a uniform design. Stamps can be made of any object that absorbs the heat from the wax. Carve the potatoes into specific shapes or use the ends of the celery stalks to make semicircular stamps.
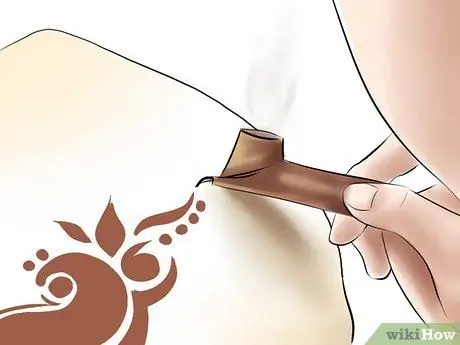
Step 6. Set the temperature of the wax
The wax should be hot enough to absorb through the fabric, but not too hot as it will spread as you use it. The wax will appear bright once the wax has absorbed into other parts of the fabric.
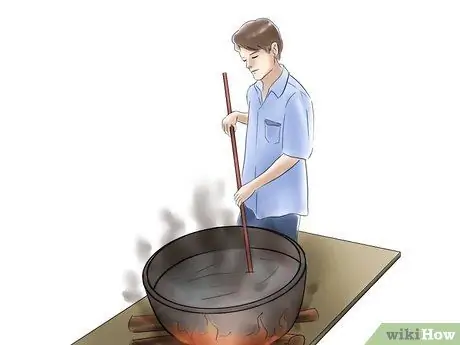
Step 7. Get ready to dye the fabric
When you choose the dye color to use, it is recommended to start with the lightest color (such as yellow) and then work with the darker color.
- Wash the fabric with “Synthrapol”.
- Dip your cloth following the directions on the package. Some dyes (such as red) are more difficult to dissolve than others.
- Add non-iodized salt to taste. For 1/4 kg dry cloth, add 1 1/2 cups salt. Use 3 cups of salt for one kg of fabric.
- Put it in the soaking cloth. Stir gently but often for 20 minutes.
- Mix with soda ash. Soda ash or sodium carbonate is used to bind the dye to the cellulose found in the fabric fibers. Dissolve the soda ash in the warm water and slowly add it to the dip (about 15 minutes). Do not dissolve directly on the surface of the fabric (because it will spoil the color). Use 1/6 cup of salt for every 1/4 kg of dry cloth. Use 1/3 cup salt for every 1/2 kg of fabric. Stir slowly but frequently for 30 minutes.
- Rinse the cloth and remove any remaining dye. Rinse with cold water until clean. Then, clean the cloth using hot water and “Synthrapol”. A second wash may be required for darker colors such as red or brown to remove any remaining dye. Dry the cloth.
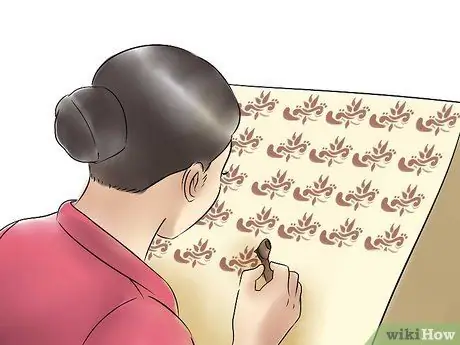
Step 8. Repeat using the wax to add additional layers of color and design
Follow the dyeing steps after you add each layer to the fabric. Dip the darkest color last.
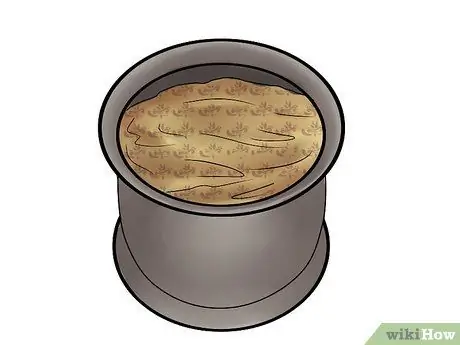
Step 9. Remove the wax
When you are finished dyeing the fabric, you can remove the wax in two ways:
- Bring the candle to a boil. Add enough water and a few drops of “Synthrapol” to the pot to soak the cloth. When the water starts to boil, put the cloth in and place a stone as a ballast to keep the wax (which will float on top) from sticking to the cloth again. After a few minutes, the wax will come off the cloth, allow the pan to cool and remove the wax coating from the top of the pan.
- Iron the cloth. Place the cloth between the blotting paper and iron over the cloth layer. The wax can remain as a residue, so make sure the wax is gone. Changing the paper periodically can help remove the wax.
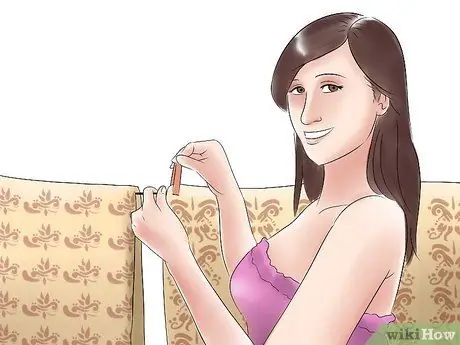
Step 10. Wash and dry the cloth
Put the cloth in the washing machine using “Synthrapol” to make sure all the wax is gone. Dry your fabric either by drying it in the sun or by machine drying. All fabrics have been batik!
Method 2 of 3: Batik Without Wax
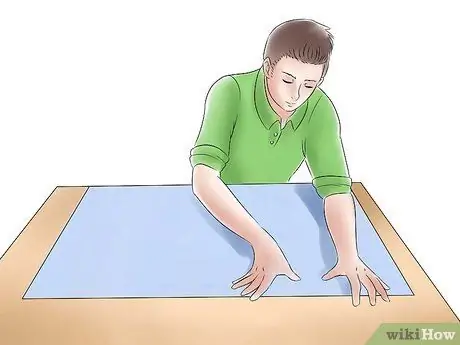
Step 1. Spread the plastic on the fabric to be made batik
Spread the cleaned and dipped cloth over the sheets of plastic wrap.
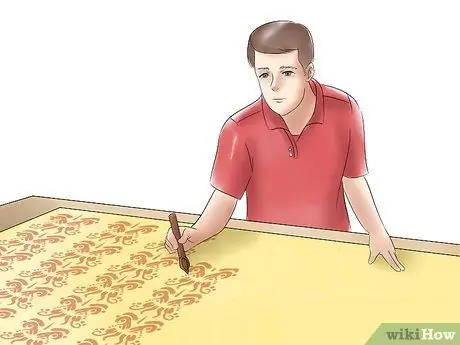
Step 2. Create a design using washable media
As is the case with traditional batik, you can use single or double perforated cantings to create thin lines. Use a brush to decorate larger areas. Allow the cloth to dry for 30 minutes, although the time it takes depends on the thickness of the cloth used.
Use the stamp on the fabric to create a repeating pattern. You can use a stencil by placing it on a cloth and drawing with a brush around the stencil
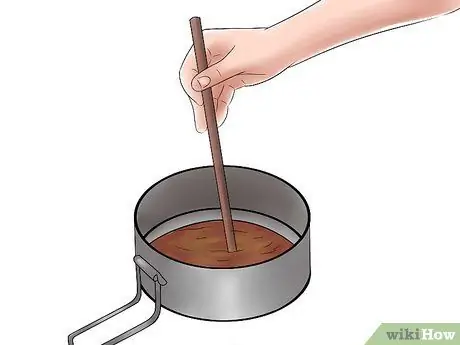
Step 3. Mix the liquid dyes
Follow the package directions for mixing the dye. If you're using liquid dyes, add more water for a softer color and mix more dye for a more vibrant color.
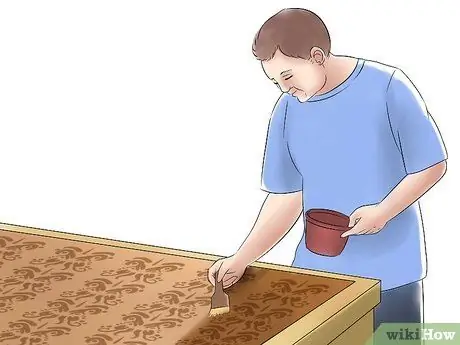
Step 4. Use the dye
Dyes can be dripped, painted, sprayed or applied. Mix two or more colors to create color variations.
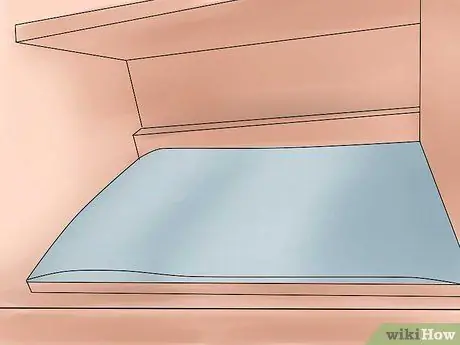
Step 5. Wrap the cloth with plastic wrap
When you're done using the dye, wrap the fabric in plastic wrap and seal the ends.
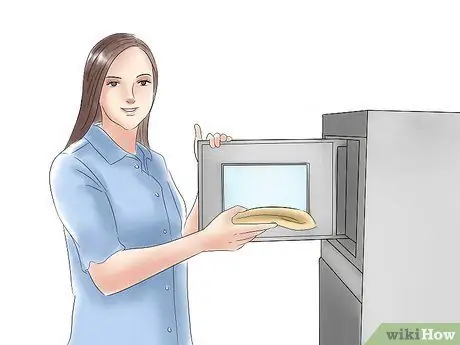
Step 6. Heat your fabric
Place tissue paper under the oven to prevent spills. Place the plastic-wrapped cloth in the oven (you may need to fold the cloth) and heat it on high for about 2 minutes.
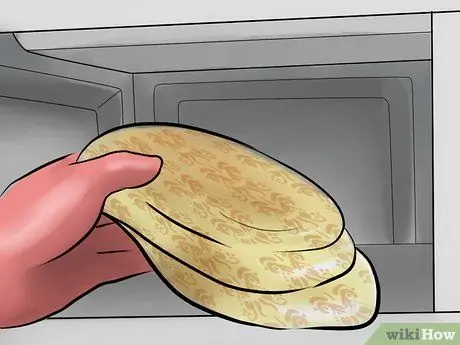
Step 7. Remove the cloth from the oven
Use thick rubber gloves and carefully remove the cloth from the oven. Be careful, the cloth is hot! Let the cloth cool for a few minutes before removing the plastic.
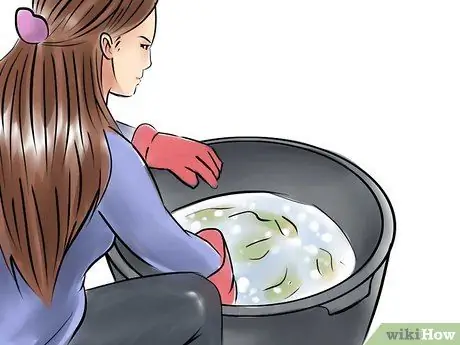
Step 8. Wash and dry the cloth
Rinse the cloth with cold water until clean. After you've removed the initial dye, wash the fabric in warm water with a mild detergent, then rinse. Dry your cloth.
Method 3 of 3: Silk Batik (Substitute Method)
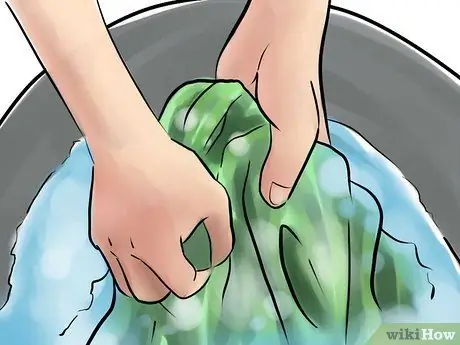
Step 1. Wash your silk
Add a drop or two of dish soap to a bucket of water. Rinse and dry the cloth. While the fabric is still slightly wet, iron the fabric on a silk or silk setting.
If you want to sketch a design instead of painting it with your free hand, then do it after ironing
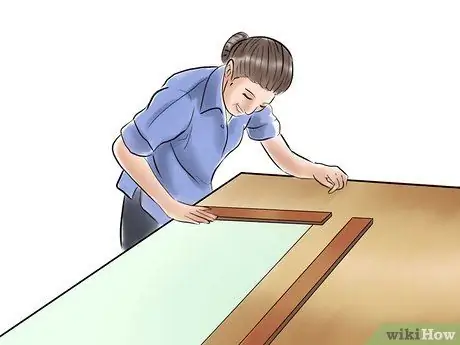
Step 2. Spread the silk
Use safety pins connected to rubber bands around the ends --every 10, 2-15, 2 cm. Spread the silk over the skeleton and then start using the pins on the skeleton. The rubber band will attach to the frame to create a tense trampoline.
- The rubber band should be small enough to maintain good pressure, but long enough to avoid tearing the fabric.
- You can connect two rubber bands together to make a longer band if your frame is larger than silk.
- The goal is to make the surface to be painted tense. The surface should be tense enough, but not too tight as this will tear the fabric.
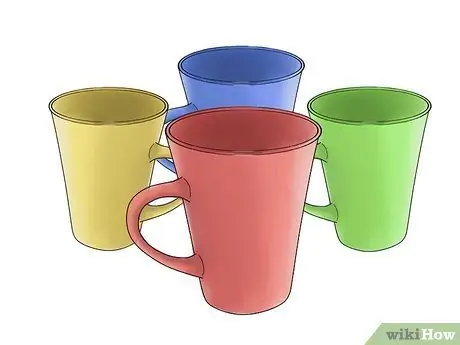
Step 3. Raise the frame
Place 4 cups or plastic containers under the frame to raise the surface of the fabric.
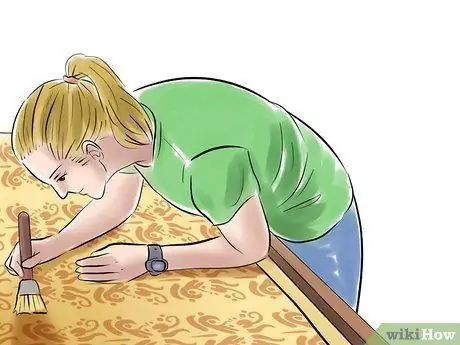
Step 4. Decorate the fabric
Decorate with a paint brush or a brush bottle with a narrow hole. Let it dry completely before you dye the fabric. There are two types of adhesives that work well for painting silk:
- Rubber adhesives, or guttae, are similar to rubber adhesives and can be used to draw smooth lines. Once the color is complete, dry the finished fabric to remove it. The disadvantage of this type of adhesive is the smoke it produces. It is recommended that you use a respirator and do so in an area that has a good ventilation system when using rubber-based gutta.
- Water-soluble adhesives are non-toxic, odorless and can be dissolved in warm water. This adhesive can work on silk paints (as opposed to dyes), which need to be heated. Disadvantages of this type are less natural results compared to other types of guttae, and fine details are difficult to make.
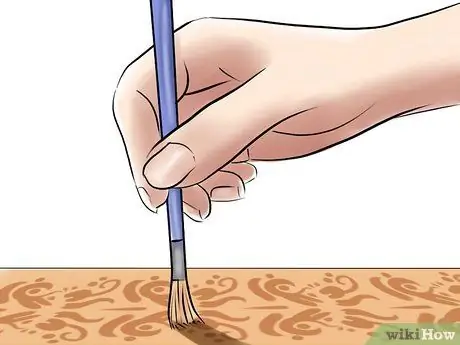
Step 5. Color the fabric
Use dyes or paint with a brush carefully. Let the color flow towards the adhesive area. Painting the adhesive directly can cause it to dissolve. There are two options for coloring, namely:
- Silk paint is a pigment-based product that imparts color to the surface of the fabric, but does not absorb into the fibers of the fabric. This color can be used for various types of fabrics (including synthetics) and is installed by ironing
- Dip the color of the silk fabric pattern by tying the fibers to the fabric. This is a good way to go if you don't want to lose the natural shine of silk. The pattern is lightweight and washable.
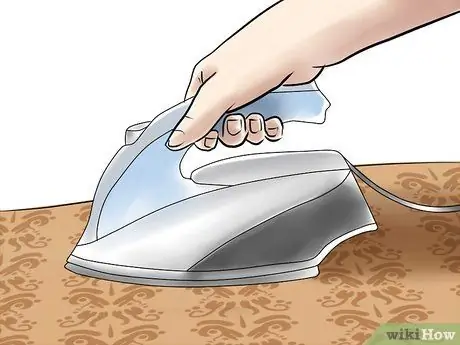
Step 6. Leave it for 24 hours
If you have chosen to dye silk, set the color by ironing the back of the fabric for 2-3 minutes. After that, rinse the silk in warm water, dry it and then iron it again while it's still slightly wet.
If you are using a silk dye, then rinse the fabric thoroughly after allowing the color to dry for 24 hours. Add a few drops of a mild detergent or dish soap to the bucket and wipe the silk off. Rinse again with cold water, then dry. When the silk is almost dry, iron on a silk or silk setting
Tips
If you put the dip in the applicator bottle (with the tip), then you can use multiple dips in one use
Warning
- If the batik wax burns, DO NOT try to douse it with water! Water can make fire spread. Use a fire extinguisher or baking soda.
- Use a respirator when using dyes that produce smoke. It is recommended to do it in a place that has a good ventilation system.
- Wear gloves to keep your hands from getting dyed. Some dyes can hurt your skin and all dyes can stain your hands.