A carport is a self contained structure used to protect your car, boat or other motor vehicle from the weather. There are carports that are built on a strong foundation, but there are also those without a foundation. If you park your vehicle outside, investing in building a protective structure will extend the life of your vehicle and will even increase the value of your property if you build it according to regulations. If you learn how to do it well, preparing the land, planning the right type of structure and building a carport from the ground up is not as difficult as you might think.
Step
Part 1 of 4: Preparing the Land
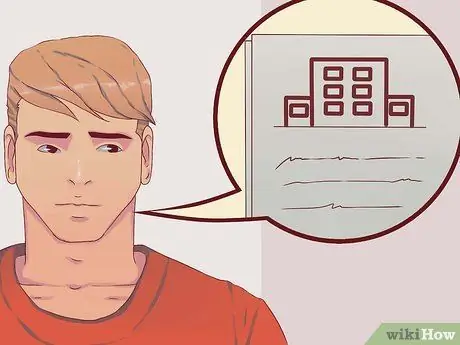
Step 1. Get the necessary build permits
Check with your local city planning office to ensure your building is built according to regulations. Since adding and building to a home building can affect the value of your home, you will need to get approval from the city government. In some areas, you will need to show a well-structured building drawing that includes the signature of a licensed builder. To get the required permissions, you need to show:
- Proof of property ownership.
- Permit application form provided by the city government.
- Building picture
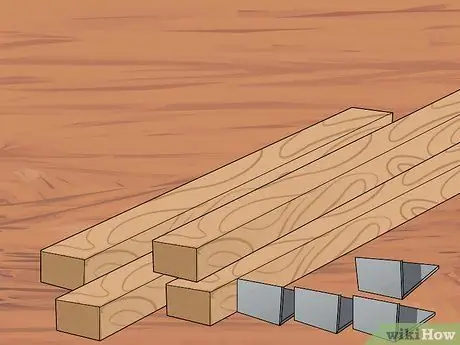
Step 2. Purchase the necessary building materials
To protect your vehicle, the carport can be built of wood or iron depending on the type and type of weather that is where you live. Different materials and designs can also be adapted to your country's climate. You can also modify the basic design and use whatever materials are available or inexpensively available depending on the type of carport you want to build. Now is a good time to experiment.
- Prestressed wood may be better suited to drier climates, but for any climate it is more durable and easy to modify for long term use. A properly constructed wooden structure will be stronger than other structures. If you want a more permanent place to park your vehicle, wood is the right choice for you.
- Galvanized iron for carport materials may be cheaper and easier to install, but is less suitable for the long term. If you need a quick and inexpensive place to house your daily vehicle, this material is for you. Prefabricated carports made of galvanized iron are often the best choice for people who need small projects that can be done on their own.
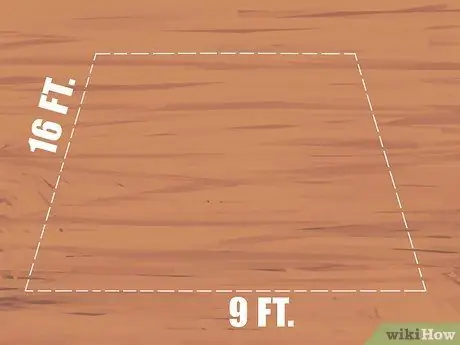
Step 3. Measure the soil
To be able to accommodate a medium-sized car, make a rectangular shape at least 5 meters long and 3 meters wide. Mark this rectangular shape on the ground. A basic carport requires six posts: one for each corner and two for centering the long sides of the square.
If you have a larger vehicle or truck or you want to build a carport for multiple vehicles, adjust the size to accommodate the structure you want to build
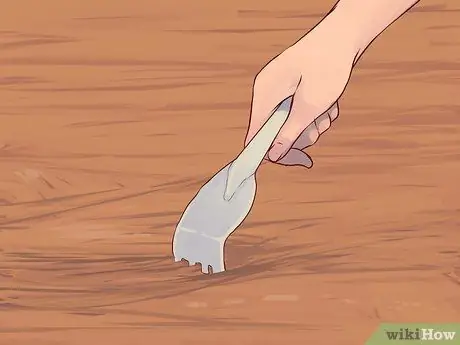
Step 4. Level the soil, if necessary
Remove the grass layer and scratch the bottom layer with an iron rake. Trample the ground with your feet and rake. While it doesn't need to be perfect, you may need to use a level gauge to make sure your ground is level.
You can build a carport on an existing concrete floor or at the end of your car park. Measure the dimensions of your concrete floor and adapt your structure to the concrete floor. Don't change the concrete floor to suit your structure. You can build a structure with posts on the sides of the concrete floor and these posts must be anchored to the ground
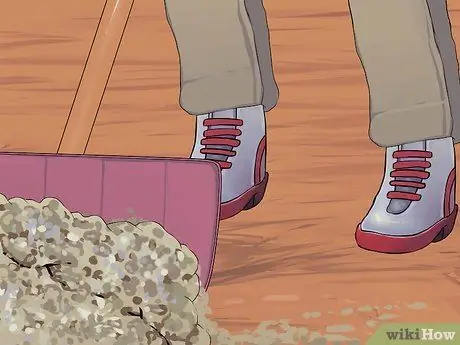
Step 5. Cover the soil, if necessary
Soil without layers is not a problem. However, coating the soil with gravel can prevent soil from entering the house and gradually wear out the soil around the carport. If you don't want to use gravel, use a plastic weed matting to prevent grass or weeds from growing back.
The best option is to pour concrete or build on an existing concrete floor as it will extend the life and durability of your carport
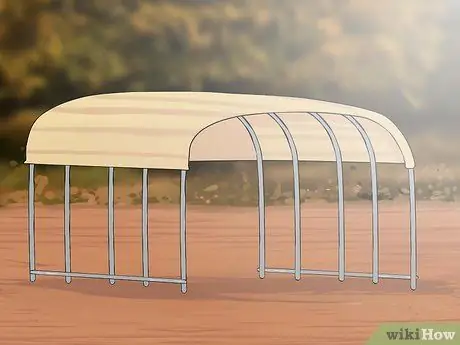
Step 6. Consider using a ready-to-buy carport kit
Since the materials and time required can make building a carport an intensive project, using a prefabricated carport may be a good fit if you are willing and able to do it.
Building materials made of iron that are equipped with installation instructions are usually available cheaper than carport devices made of wood. You can install in a day or two
Part 2 of 4: Installing the Beams
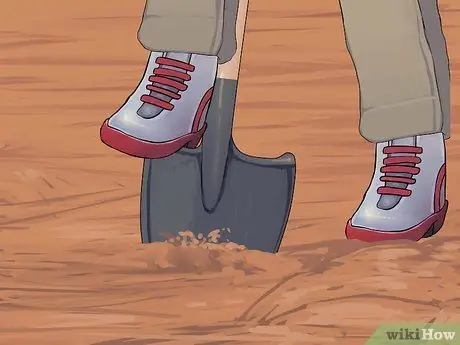
Step 1. Dig holes for the posts
Make the post holes equally spaced in the line you have made for your carport. Use a digger to make a hole. The hole should be at least half a meter deep and for a sturdier structure for those who live in areas with strong winds or areas with moderately heavy snowfall, make a deeper hole.
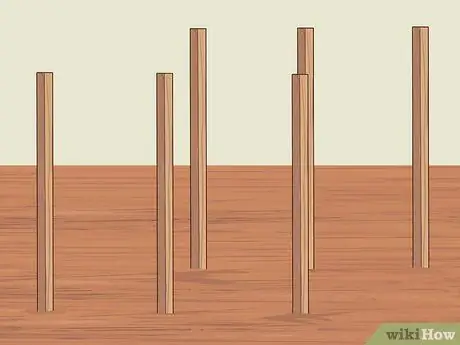
Step 2. Install the six posts
For a simple structure, you will need high-quality posts that are at least 2.7 meters high on one side of the carport and 3.5 meters on the other to form a roof slope that can help drain rainwater down. Three taller posts should be on the side of the carport closest to the house to keep water away from the foundation of the house.
To install the posts, pour 15 cm of concrete into a half meter hole. Plant the pole into the hole until the pole touches the ground. Pour more concrete until the hole is completely filled. Use a level gauge and before the concrete hardens, adjust the posts so that the posts stand vertically upright. Allow the concrete to harden for at least one full day before nailing the posts to the joists
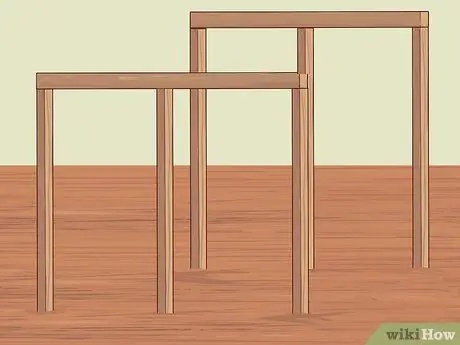
Step 3. Nail the front and back beams first
If you want to build a walled carport, carport walls can be made of rectangular boards measuring approximately 5 x 2.7 meters and about 2.1 meters high nailed to posts.
Nail the load-bearing joist over the lower corner of the post and extend it to the higher corner about 50 cm from the top end. Then, nail these blocks to higher posts using T-shaped hangers that can be purchased at any hardware store. Before nailing the hangers, make sure the beams are the same height
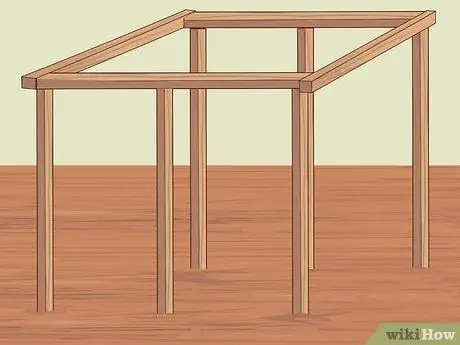
Step 4. Nail the side beams
Nail the joists to the posts to secure the posts according to regulatory specifications. The beams on the lower side must be nailed over the front and back beams whose beams have been nailed to the corners of the posts. If necessary, you can add fasteners by nailing the top of the center post to the lower side to make the joists even across all three posts.
You should make your structure as strong as possible, especially if you live in an area that has snow, wind or other extreme climates. For load bearing specifications, you will need to find out the requirements in your area. There is no single or universal way to do this. For that, always follow your local guidelines
Part 3 of 4: Making the Roof

Step 1. Nail the easel to the side beams
The six 5 cm x 10 cm x 3 meter trusses that will support the roof can be nailed to the core box shape in two ways: the notch method or the hanging method. For either method, the front and rear stances must be nailed to the front and back beams. The remaining four easels must be spaced equidistant from each other (approximately 1 - 1.2 meters) along the side beams measuring 5 meters.
- Notching the easel is a way of placing the easel on the edge of the side beam. To make the notch, place the front stance in place and mark its place on the side beam with a pencil. At that point, make a notch with a circular saw so that the easel goes about a third into the side beam. When you are satisfied with the notch of the first easel, lower the stance and use it as a reference to make notches on the other five stances. When nailing the easel, hammer the nail on the side of the easel at an angle into the beam underneath.
- To hang an easel, buy a metal hanger at a hardware store. Metal hangers come in different shapes and designs which can attach 5 x 10 cm beams to other structural elements in various orientations. The angle of inclination used for this structure or the angle of the truss to the beam is 25 degrees. This metal hanger can be bent to accommodate minor variations. So don't worry if you can't find the perfect hanger. Unlike the notch method, in the hanging method, the easel is placed on a beam. Your nail will go into the hanger, then into the easel and finally into the beam.
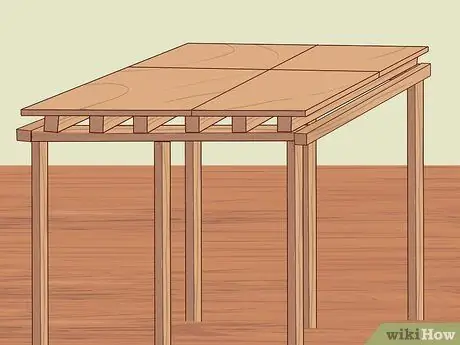
Step 2. Nail the roofing plywood to the truss
Arrange the plywood sheets in such a way that there are 15 cm indentations on the front and back of the carport to get a uniform look on the carport.
- Buy as many plywood sheets as possible. The plywood is usually 1.2 X 2.4 meters in size, but the size can vary. The entire roof surface measures 3 X 5. 2 meters. Cut the plywood with a saw to minimize the number of joints. The fewer the joints, the less chance of leakage.
- The width of the core box of your carport is 2.7 meters and the easel is 3 meters long. This means that when the roof is installed, you need a plywood that can cover the roof area as well as a 15 cm beam on both sides of the carport. If you want a longer one, you will need more plywood.
- Triplex has various thicknesses. For this project, you can use plywood with a thickness of 1.2 cm. If you are worried about deflection, use plywood with a thickness of 2 cm.
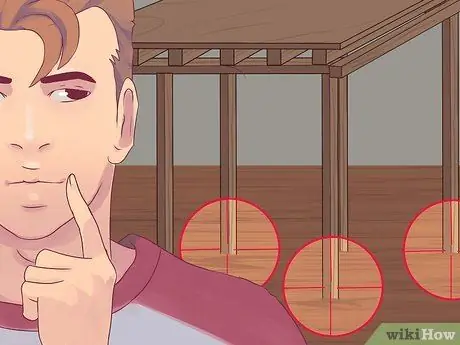
Step 3. Check the stability of your structure
Once the roof is in place, your structure should be solid. At this point, there is nothing you can do to improve the overall stability of your carport. Therefore, when movement occurs in your structure, you must add stiffeners outside the structure to enhance stability.
Part 4 of 4: Finishing the Job
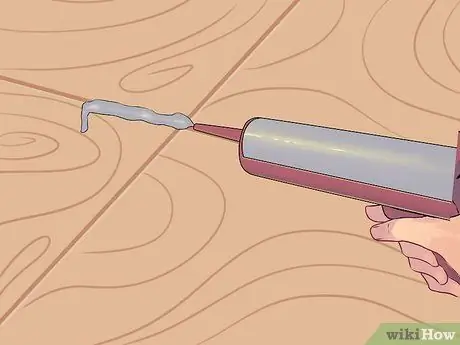
Step 1. Coat the plywood joints with a leak-proof layer
To prevent leakage, you must fill the gaps with a leak-proof layer and coat the surface with a leak-proof layer before installing the tile or shingles. There is no point in you making a carport to protect your vehicle if the carport leaks.
Is it necessary to insulate the structure? That's fine, but it may not be economical. Keep in mind that you are not building additions to your home. You just build a simple structure to protect your car from the weather
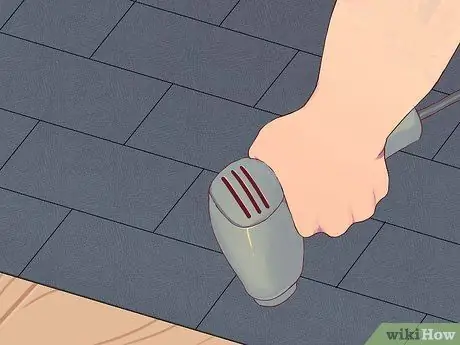
Step 2. Install the tile or shingles on the roofing plywood
Go to a hardware store and buy enough tile or shingles to cover the plywood and give the carport a finishing touch. You may need to purchase a weatherproof coating for the plywood before the plywood is covered with tile or shingles for extra protection.
Alternatively, if you don't want to use tile or shingles, you don't need to install plywood and directly install the iron roof on the truss. Sloping aluminum roofs are commonly used for outbuildings. When you use a roof like this, your structure will be completed faster. If you like how it looks and can withstand the noise of metal roofing when it rains, this roofing material is the best choice
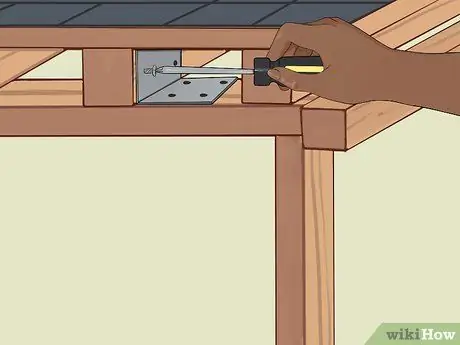
Step 3. Reinforce the connection with an iron plate
The joint members of the structure may need to be reinforced with steel stiffeners for extra stability. The hardware store in your area may sell a variety of metal plates that can be nailed to various structural joints, particularly where posts meet beams, beams and trusses and other places.
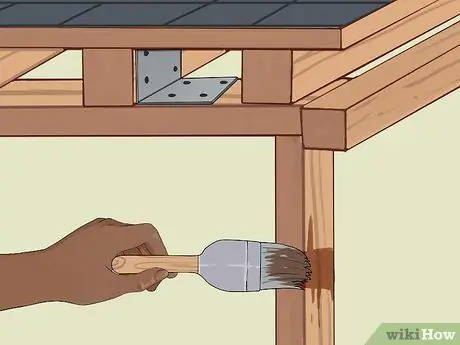
Step 4. Paint the wood
Because building a carport is not an easy thing, don't forget to coat your wood with a layer of protective paint. This paint will extend the life of your wood and prevent you from building a new carport for years to come.