Marginal cost is the cost that you (or the business) would incur if it produced an additional unit of a good or service. Marginal cost is also sometimes called “last unit cost”. You need to know the amount of marginal cost to maximize profit. To calculate marginal cost, divide the change in cost by the change in the quantity of a particular product or service.
Step
Part 1 of 3: Determining Quantity Change
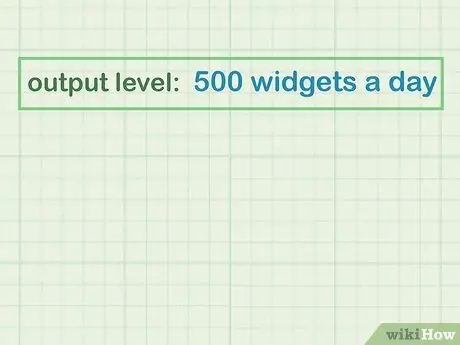
Step 1. Find the level of output that changes fixed costs
To calculate marginal cost, you need to know the total cost of producing one unit of the product or service sold. Fixed costs should remain the same throughout the cost analysis so you need to know the level of output that will increase these fixed costs.
For example, if you have a cup cake bakery, the oven is a fixed cost. If the oven is capable of producing 1,000 cakes per day, this means that the maximum quantity of cupcakes considered for the marginal cost analysis is 1,000. If you produce more than 1,000 cakes, the fixed costs will change because you will need to purchase an additional oven
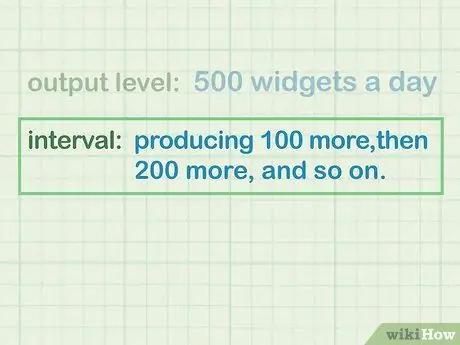
Step 2. Specify the interval you want to evaluate
Perhaps you want to calculate the margin cost of each individual unit of product or service sold. However, this usually only helps if you produce only a few products or services in a day. Otherwise, you should watch the quantity change in multiples of 10, 50, or even 100.
- For example, say you operate a spa service that offers 3-5 massages per day. You want to know the marginal cost of adding one more massage session. In this case, it is natural that the interval is one.
- If you're producing a product, it's best to look for large quantity changes. For example, if the company produces 500 pairs of shoes a day, it would be wise to consider the marginal costs of producing an additional 100 pairs of shoes, 200 pairs, and so on.
Tip:
If you're having trouble finding the interval you want to evaluate, start small. If the marginal cost becomes very small, you can recalculate it using a larger interval.
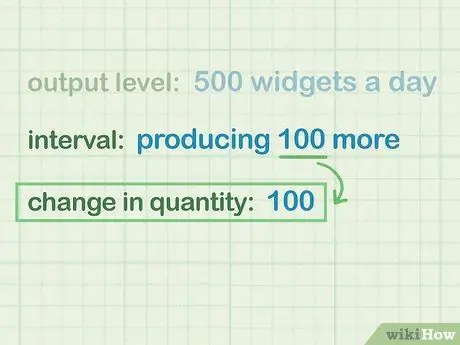
Step 3. Subtract the quantity of the second production unit by the quantity of the first production unit
Each interval will show an increase in production. To find the change in quantity, simply subtract the new quantity from the old quantity.
For example, if a company produces 500 pairs of shoes a day and you want to find the marginal cost of producing 600 pairs of shoes a day, the “change in quantity” is 100
Part 2 of 3: Determining the Point of Change in Cost
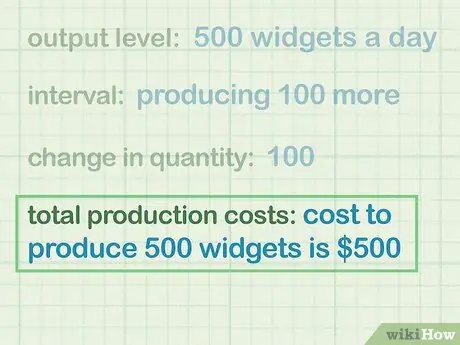
Step 1. Calculate the total production cost
Total costs consist of fixed costs and variable costs for the number of units of a particular product or service. Fixed costs are costs that do not change during the period being evaluated. On the other hand, variable costs are costs that can be changed and increased or decreased depending on the circumstances.
- Capital expenditures such as equipment are usually fixed costs. The building rental fee that is paid every month is also usually a fixed cost.
- Variable costs include utility expenses, employee salaries, and supplies used to produce products. These costs are variable because they increase as the quantity produced is increased.
- Calculate variable costs for each level of output and production interval. Add variable costs to fixed costs to get fixed costs.
Tip:
You only need a total cost figure for each level of output or production interval to calculate marginal cost. You don't need to know the share of fixed costs over variable costs in total costs, although in other contexts this information can be useful.
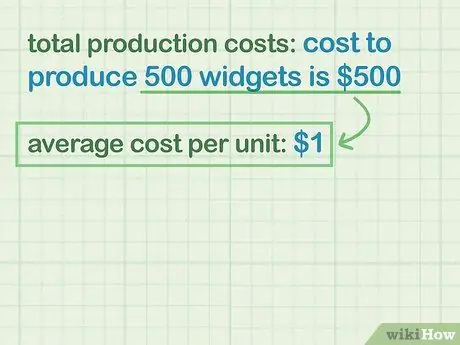
Step 2. Find the average cost for each unit
Once you have the total cost, you can find the average cost per unit of the product or service sold. At each output level or production interval, simply divide the total cost by the number of units.
- For example, if the total cost to produce 500 pairs of shoes is $500, the average total cost per unit is $100. But if the total cost to produce 600 pairs of shoes is $550,000, the average total cost per unit of that quantity is $92,000.
- You can also calculate average fixed costs and average variable costs.
Tip:
Although not used to calculate marginal cost, average cost figures can help you find the best production level for the product or service being sold.
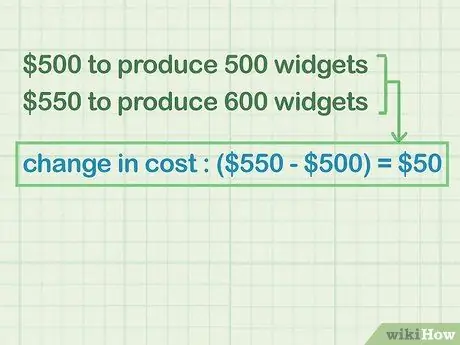
Step 3. Subtract the new cost from the old cost to find the cost change
Changes in costs are measured in the same way as changes in quantity. Reduce the cost of producing in bulk by producing in small quantities. The sum is the cost change for the corresponding interval.
On the other hand, if the cost of producing 500 pairs of shoes is Rp. 500,000 and Rp. 550,000 to produce 600 pairs of shoes, the “change in cost” is Rp. 50,000
Part 3 of 3: Finding Marginal Cost
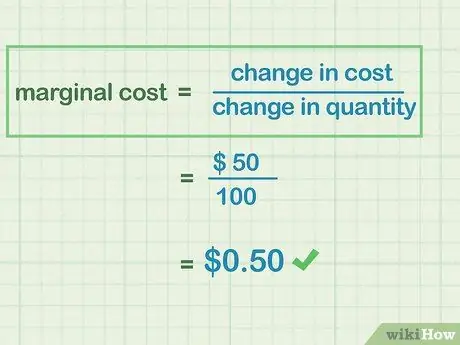
Step 1. Divide the change in cost by the change in quantity
The formula for calculating marginal cost is the change in cost divided by the change in quantity. So, once you find the change in total cost and quantity, use them to easily calculate marginal cost.
For example, say you want to calculate the marginal cost of producing 600 pairs of shoes a day and 500 pairs a day. The change in total cost is IDR 50,000 and the change in quantity is 100 pairs. Thus, the marginal cost is $500
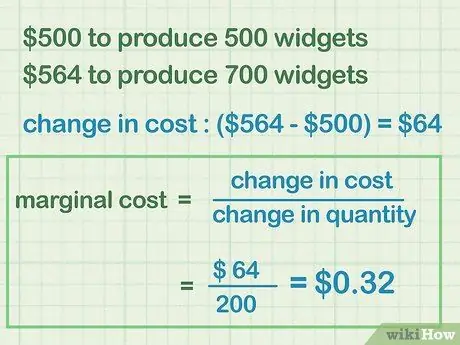
Step 2. Repeat the calculation for additional intervals
Your marginal cost may increase or decrease as you continue to add extra units of production. In particular, the production of a good or service should be at the lowest possible marginal cost.
- For example, say the marginal cost of producing 600 pairs of shoes instead of 500 pairs is $500. However, the marginal cost of producing an additional 100 pairs of shoes (700 pairs) is only Rp320. Producing 700 pairs of shoes will be more effective than producing only 600 pairs of shoes.
- Your marginal cost doesn't always decrease. In the end, the marginal cost will increase. For example, if you hire an additional team to produce 800 pairs of shoes, the marginal cost will increase to $520.
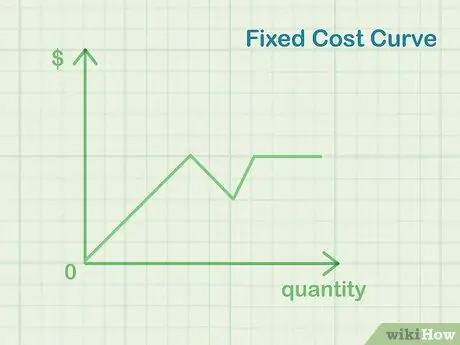
Step 3. Enter the data into a spreadsheet to create a cost curve
By entering data into a spreadsheet, you can create a graph that visually displays the marginal cost of each production interval or level of output. The marginal cost curve is usually U-shaped, with the "trough" at the beginning of the curve, with an increase in costs resulting in an increase in the quantity produced.
Turning the data into a curve graph also allows you to determine the best and most effective level of production for your business
Tip:
If you are calculating average total cost and average variable cost, you can also graph both curves, which are also U-shaped, even though the trough is near the end of the curve, and is different from the marginal cost curve.