As part of the Occupational Safety and Health Management System (SMK3), you must control the risks that exist in the workplace. It is your responsibility to consider what may harm workers and decide on the appropriate course of action to avoid accidents. This process is called risk assessment and is a legal obligation for the business owner. The risk assessment is not aimed at compiling thick documents and reports. On the other hand, a risk assessment will help you estimate all possible risks in the workplace and how to keep workers away from them. To make a complete risk assessment, you have to go through a series of steps, and then build an assessment.
Step
Part 1 of 4: Identifying Hazards
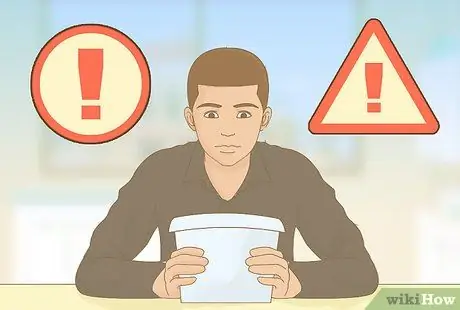
Step 1. Understand the definitions of “hazard” and “risk” in the workplace
These two terms are important to distinguish and use appropriately in assessment.
- Danger is anything that can cause harm. For example, chemicals, electricity, working from a height such as a ladder, or even an open drawer.
- Risk is the possibility of harm to people. For example, a chemical burn or electric shock, a fall from a height, or an injury from hitting an open drawer.
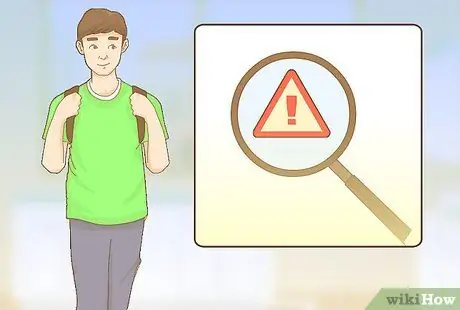
Step 2. Learn about your workplace by walking around
Consider all the dangers you notice while traveling around. Think about any activity, process or substance that could harm workers or endanger their health.
- Pay attention to any objects, office furniture, or machine parts that may pose a hazard. Check all substances in the workplace, from chemicals to hot coffee. Think about the potential for the substance to harm workers.
- If you work in an office, look for long cords on the floor or under desks, as well as damaged drawers, cabinets, or desks. Check employee seats, windows, and doors. Look for potential hazards in common places, such as a broken microwave or uncovered parts of the coffee machine.
- If you work in a large grocery store or warehouse, look for machines that may be dangerous. Watch for items such as hooks or safety clips that could fall or hit workers. Look for hazards in store aisles, such as narrow shelves or broken floors.
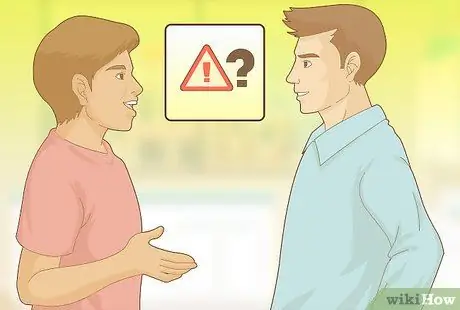
Step 3. Ask your workers about potential hazards
Workers will be able to help identify all the hazards they encounter on the job. Send an email or have a live discussion asking for feedback on possible hazards in the workplace.
Ask specifically about the hazards that your workers think could result in significant accidents, such as slipping and tripping, fire hazards, and falls from heights
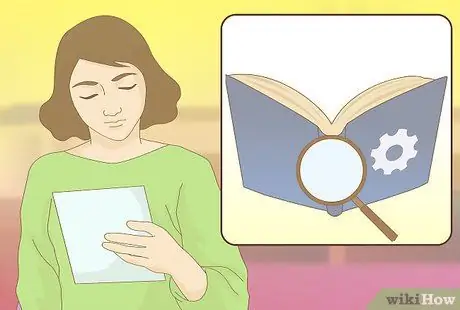
Step 4. Check the manufacturer's instructions or manuals on equipment and substances
Such information can help explain potential hazards and provide an understanding of how the equipment is used and that misuse can be dangerous.
The manufacturer's instructions are usually on the equipment or substance label. You can check the manual for information on the potential hazards associated with the equipment or substance
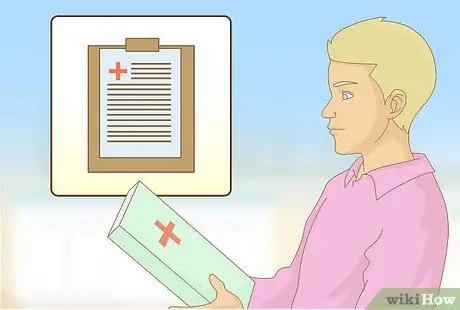
Step 5. Check your workplace accident or illness history
The document will help identify hazards that cannot be clearly identified and all hazards that have occurred in the workplace.
If you are in a management position, you may be able to access these records from the company's website or files
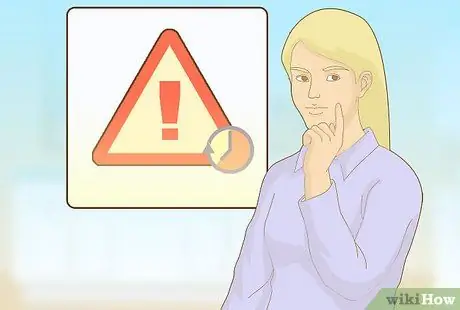
Step 6. Think about possible long-term harm
Long-term hazards are hazards that will affect workers if they are exposed to them for a long period of time.
Long-term hazards can be exposure to high levels of noise or continued exposure to hazardous substances. This hazard can also be a safety hazard from repeated use of tools, from levers on construction sites to keyboards on desks
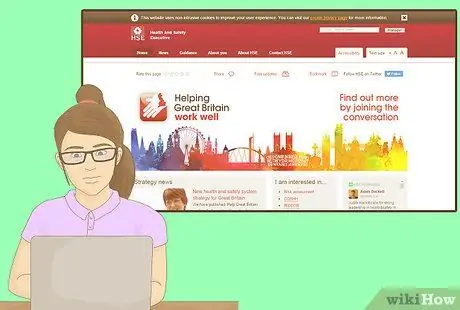
Step 7. Visit the Indonesian Ministry of Manpower website
You can access guidelines for managing occupational health and safety via the Indonesian Ministry of Manpower website. This site has news and information for controlling workplace accidents, including recognizing hazards such as working at heights, with chemicals, and with machines.
- You can access the Indonesian Ministry of Manpower website here.
- You can access the Regulation of the Minister of Manpower of the Republic of Indonesia regarding the Implementation of the Assessment of the Implementation of the Occupational Health and Safety Management System (SMK3) here.
Part 2 of 4: Determining Who May Have A Work Accident
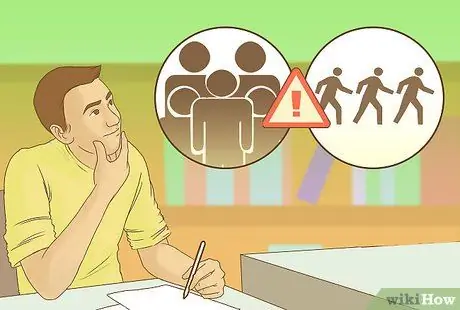
Step 1. Identify groups at risk for accidents at work
You can create a description of all the individuals who are potentially at risk, so don't make notes by worker name. Instead, list groups of people based on their scope of work.
For example, “employees working in warehouses” or “people passing by on the street”
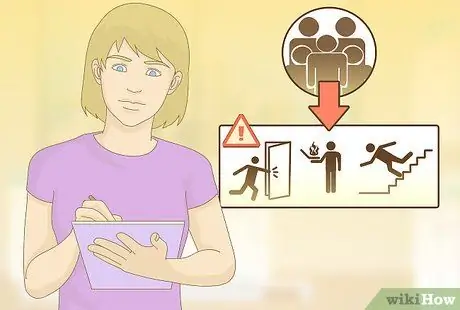
Step 2. Determine how harm could befall each of these groups
You must identify the type of accident or illness that may occur in each group.
- For example, “stack stackers can suffer back injuries from lifting boxes all the time”. Or, “machine operators may experience joint pain from repeated use of the lever.”
- This note can also be made more specific, for example “worker could get burned by printer” or “janitor could trip over cable under desk”.
- Please note that some workers may have special needs, such as new and young workers, pregnant or nursing mothers, and employees with physical limitations.
- You should also consider janitors, visitors, contractors, and maintenance personnel who are not always on site. You should also identify any possible danger to the general public or “passers-by”.
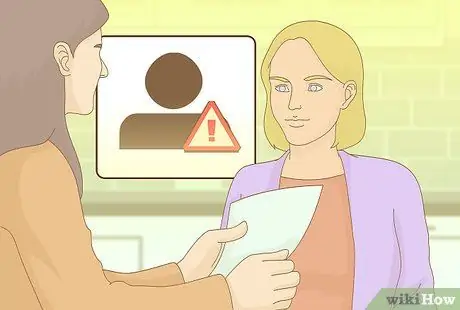
Step 3. Discuss with employees about groups at risk of harm
If the workplace in your company is an open space shared by several or hundreds of workers, you should discuss with them and ask who they think is at risk of an accident. Think about how your work affects the other people there and how their work affects your staff.
Ask your staff if they've noticed anyone who may have had a particular accident that you didn't think of. For example, you may not notice that the cleaners also have to lift boxes on employees' desks or you may not notice that some parts of the machine make noise harmful to pedestrians outside
Part 3 of 4: Evaluating Risk
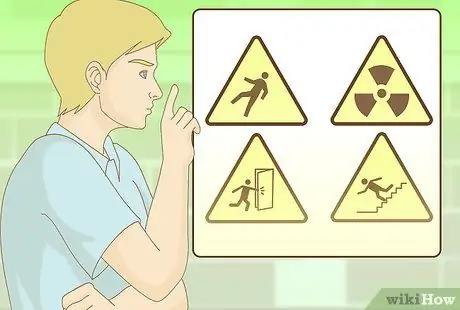
Step 1. Determine how likely the hazard will be in the workplace
Risk is part of everyday life and even if you are the boss or in charge, you are not expected to eliminate all of them. However, you must be aware of the main risks and know how to recognize and manage them. So you must do all you can to protect people from harm. This means you have to balance the level of risk and the actions required to control the real risk in terms of money, time or difficulty.
- Keep in mind that you should not take any action that is deemed inappropriate for the level of risk. Don't overstep your judgment. You just need to include what you need to know within reasonable limits. You are not expected to anticipate unforeseen risks.
- For example, the risk of a chemical spill must be taken seriously and recorded as a major hazard. However, smaller risks such as a stapler hurting the person using it or a jar lid flying over someone are not considered natural hazards. Do your best to identify major and minor hazards, but do not need to consider all possible minor hazards.
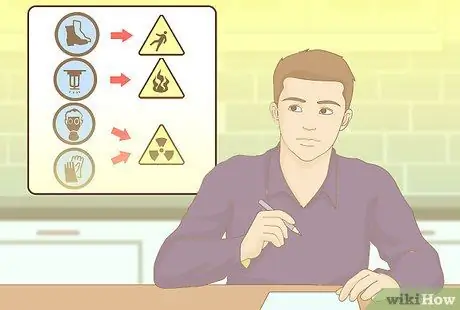
Step 2. Specify the control measures that can be applied for each hazard
For example, you can provide back protection and safety for workers stacking items on shelves (or personal protective equipment). However, ask yourself: Can the danger be completely eliminated? Is there a way to reorganize the warehouse so that the workers stacking the goods don't have to lift the boxes off the floor? If not, how to control the risk so that accidents do not occur? Practical solutions to these problems include:
- Try less risky options. For example, placing the box on a high platform or ledge to reduce the lifting distance of the box.
- Avoid access to hazards or arrange workplaces to reduce exposure to hazards. For example, rearranging the warehouse so that the boxes are placed at a height that workers no longer have to lift.
- Provide protective equipment or safety alloys for workers. For example, back protectors, personal protective equipment, and guides for getting the job done safely. You can teach the builders how to lift boxes off the floor by bending your knees and making sure your back is flat.
- Provide health facilities, such as first aid kits and washing facilities. For example, if workers have to deal with chemicals, you should provide washing facilities and a first aid kit near their work stations.
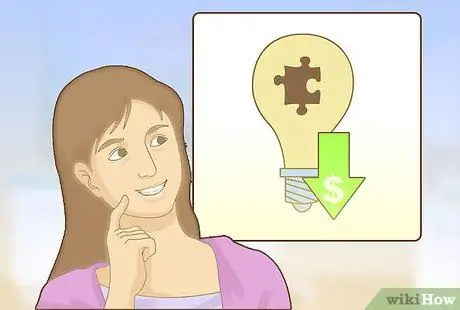
Step 3. Find an effective and inexpensive solution
Efforts to improve health and safety do not mean spending a lot of company money. Minor adjustments such as placing the mirror at a broken angle to avoid collisions or holding a brief training session on how to properly lift things are preventative measures that don't require a large amount of money.
In fact, not taking simple precautions will cost you a lot more if an accident occurs. Worker safety should be considered more than anything else. So, if possible, opt for a more expensive solution if that is the only option. Spending money on preventive measures is a better option than spending on caring for injured workers
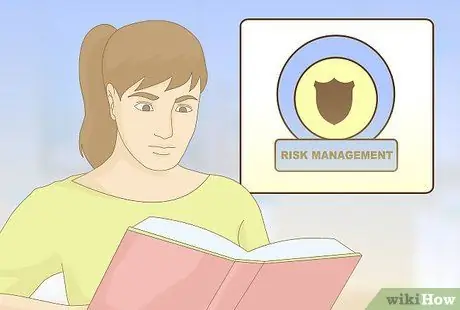
Step 4. Read risk assessments made by leading companies, trade associations and workers' organizations
The organization's guidelines usually include risk assessments for various activities, such as working at heights or with chemicals, as well as work in specific sectors, such as mining or administration.
Try applying the organizational assessment model to your workplace and adapt it to your needs. For example, their assessment examples might suggest ways to prevent falls from stairs or how to organize cables in the office to make it safer for employees. Then, you can apply those suggestions in a risk assessment that is being developed based on your own workplace specifications
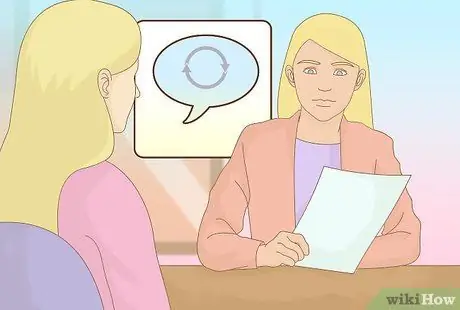
Step 5. Ask for feedback from workers
You need to involve workers in the process of evaluating risks and creating prevention guidelines. This ensures that what you propose will be implemented and will not pose any new dangers.
Part 4 of 4: Recording Findings in Assessment
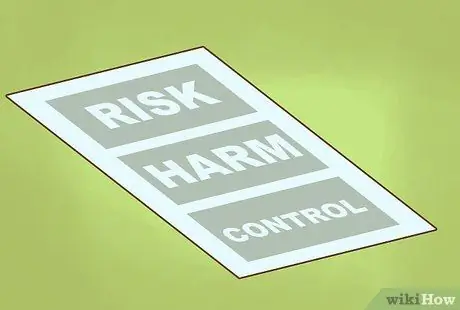
Step 1. Make the assessment simple and easy to follow
The assessment should cover the hazard, how the hazard may affect workers, and what must be prepared to control the risk.
- If you have fewer than a hundred employees or your workplace does not have a high level of potential, you are not required to prepare a risk assessment. However, a risk assessment would be useful to review and update it.
- If you have at least a hundred employees or your workplace has a high level of potential for harm, you are required by law to make a risk assessment.
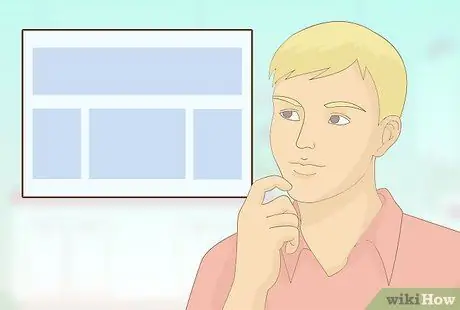
Step 2. Use the sample risk assessment format
There are several examples of formats available on the internet based on the workplace and can be applied as needed. The baseline risk assessment must demonstrate that:
- The hazard check has been carried out as well as possible.
- You've asked who might be in danger.
- You have dealt with the major and obvious hazards and have considered the number of people who may be involved in the harm.
- The precautions taken are reasonable and practical.
- The other risks are low and/or manageable.
- You involve employees in the appraisal process.
- If the nature of your work changes frequently or the workplace changes and evolves, such as a construction site, the risk assessment should concentrate on the set of risks that can be anticipated. This means that you must include the conditions of the construction site workers will build on or the possible physical hazards in the area, such as fallen trees or falling rocks.
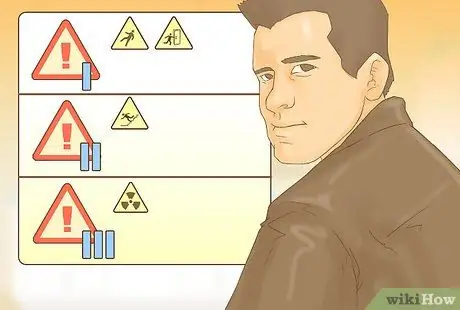
Step 3. Rank the hazards from most serious to least serious
If your risk assessment identifies several types of hazards, you should rank them by urgency. For example, a chemical spill in a chemical plant is the highest risk, and back injury from lifting barrels in a chemical plant may be a less serious risk.
Ratings are usually based on fair judgment. Consider the hazards that could result in serious accidents such as death, amputation, or burns and serious injury. Then, rank the hazards from the most serious to the least serious
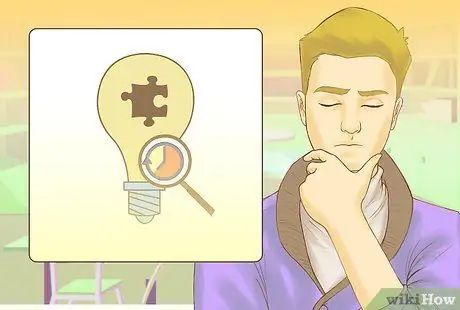
Step 4. Identify long-term solutions to risks with greater consequences, such as illness and death
This means that you may need better chemical spill prevention measures or clear evacuation procedures in the event of a chemical spill. You can also provide workers with high-quality personal protective equipment to prevent exposure to chemicals.
- See if these fixes or workarounds can be implemented quickly, or even temporarily until more reliable controls can be implemented.
- Keep in mind that the greater the hazard, the stronger and more reliable the control measures required.
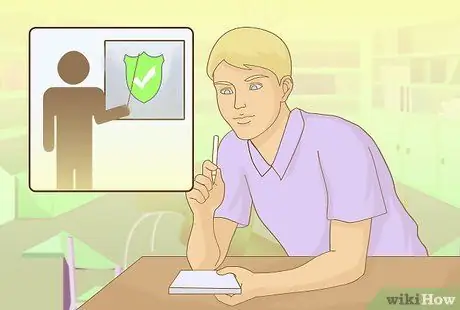
Step 5. Record the required employee training
The risk assessment you develop may include the need for employee training on safety practices, such as lifting boxes off the floor the right way or how to handle chemical spills.
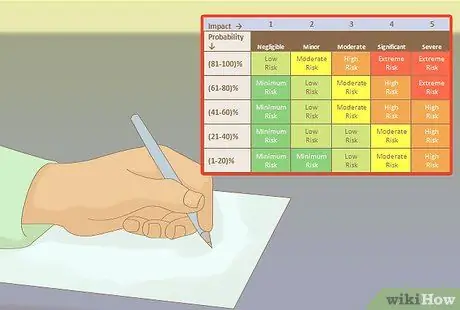
Step 6. Create a risk assessment matrix
Another approach that can be taken is to use a risk assessment matrix that helps determine how likely an accident is to occur in the workplace. The matrix has a “Consequences and Trends” column which is divided into:
- Rarely: Can occur at any given time.
- Chances: Can happen at any time.
- Possibly: It may happen at any time.
- Likely: Will occur in most situations.
- Almost Certain: Expected to occur in most situations.
- The top column will then be divided into the following sections:
- Insignificant: Low financial loss, does not interfere with capabilities, has no impact on the community.
- Minor: Moderate financial loss, slightly impaired ability, little impact on community.
- Serious: High financial loss, impairs continued capacity, moderate impact on community.
- Disaster: Huge financial loss, disrupting sustainable capabilities, having a major impact on the community.
- Catastrophe: Critical financial loss, permanently impairing capacity, and devastating impact on the community.
- An example of a risk matrix can be seen here.
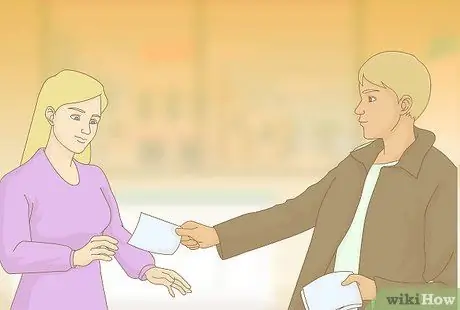
Step 7. Share the prepared risk assessment with employees
You are not required by law to share risk assessments with workers, but it would be great if you are willing to share the full paperwork with them.
Keep a printed version of the risk assessment file and provide an electronic version in the company's shared archives. You need to have easy access to the document so that it can be updated or modified as needed
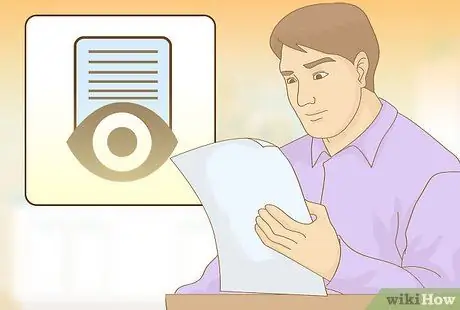
Step 8. Review the risk assessment regularly
Very few workplaces remain unchanged, and sooner or later you will have new equipment, substances, and procedures that can pose new hazards. Review employee work practices daily and update your risk assessment. Ask yourself the following questions:
- Are there any changes?
- Did you learn anything from an accident or near miss?
- Set a review date each year. If there are significant changes in the workplace during the year, update the risk assessment as soon as possible.