Artists and engravers have carved metal or wood for centuries, and produced many works from this branch of art. Today, new laser engraving tools and other engraving machines can be used to engrave plastic, gemstones, and other materials that are difficult to engrave. While you can use a variety of these tools, you can start carving your own using just a few tools.
Step
Method 1 of 3: Engraving Metal
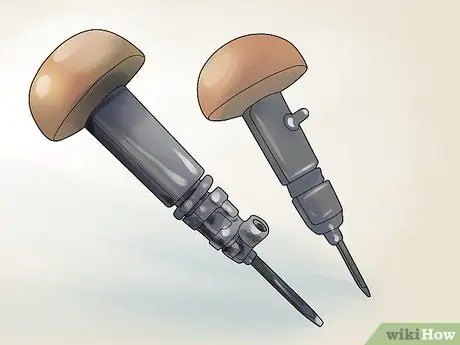
Step 1. Choose your equipment
You can use a hammer and a chisel, but you can also opt for less expensive tools such as a hand-driven or air-filled “engraver” or “burin”, which provide more stability and control. If you already have a dremel with a tungsten carbide drill bit, you are better off using that tool.
- The tip of the engraving tool has many different shapes. The "V" box is one of the most versatile.
- Smooth metal can rarely be engraved with a compass or engraving knife, and a precise 3D finish can be difficult to achieve.
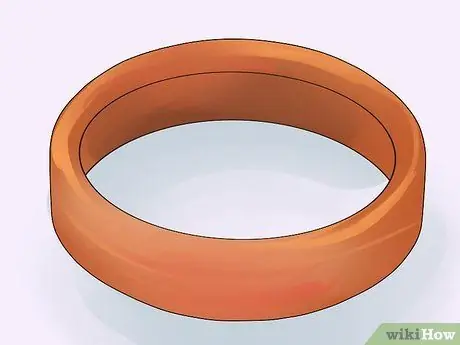
Step 2. Choose a metal object for you to practice
If this is your first engraving project, don't engrave your precious heritage watch first. Practice with other items that are ready to break. Finer metals such as copper or brass are quicker and easier to carve than iron or other hard metals.
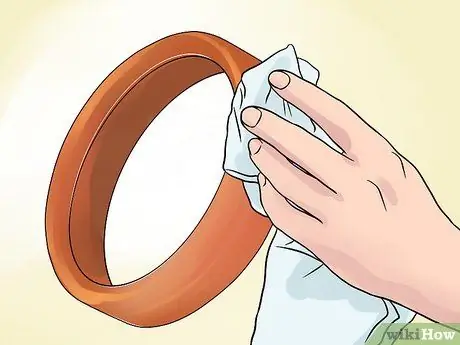
Step 3. Clean the metal
Use a damp cloth to clean the metal surface, then dry with a dry cloth. If the metal is still dirty, brush it with soapy water and dry it.
If the metal has a protective coating on its surface, which is usually the case with brass, you don't need to remove the polish. The engraving process will penetrate this polish, so you will need a fresh protective coat after engraving if you want the metal color to remain consistent
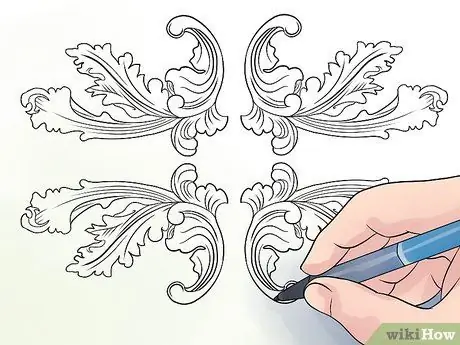
Step 4. Draw or print a design
If you are engraving on a small object or you are engraving for the first time, draw or print a simple design with sufficient line spacing. Detailed engraving can be difficult to do without some practice and may end up looking messy or blurry when it's engraved. You can draw designs directly on the metal. If not, draw or print it at the correct size, then follow the next steps to transfer it onto the metal.
If you are engraving letters, make them as even as possible by drawing them between two straight parallel lines drawn with a ruler
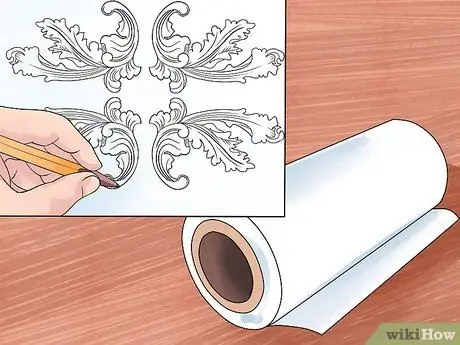
Step 5. Transfer the draft onto the metal (if needed)
Follow these steps if you want to transfer the design onto the metal; if your design is already on metal, move on to the next step. If you can't find the specific material you need, search online for one of the many ways to move an image. Keep in mind most of these tools also require a special type of equipment.
- Add varnish or lacquer on the part you want to carve, wait for it to dry and slightly stick.
- Draw the design on the polyester layer ("Mylar") using a soft pencil.
- Cover your image using masking tape. Apply the tape thoroughly using your fingernail or using a polishing tool, then gently lift the tape off. Now, your design is on the tape.
- Attach the tape to the lacquered metal. Apply with your fingernail in the same direction, then remove the tape.
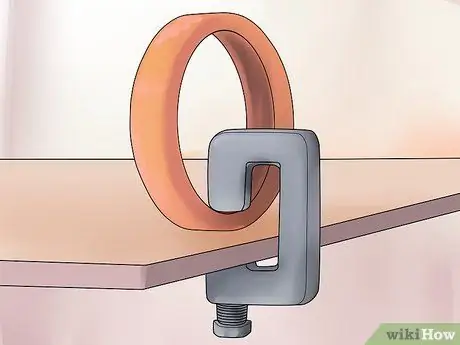
Step 6. Clamp your metal in place
Engraving will be much easier if you use tweezers or a vise to keep the metal from falling off. You can use a grip vise that allows you to hold it in one hand with a firm grip, but be aware that this increases the chances of scratching or scraping. If you are using a powered tool or a hammer and engraving tool that requires two hands, it is highly recommended that you use tongs that hold the metal on a table or other stable surface.
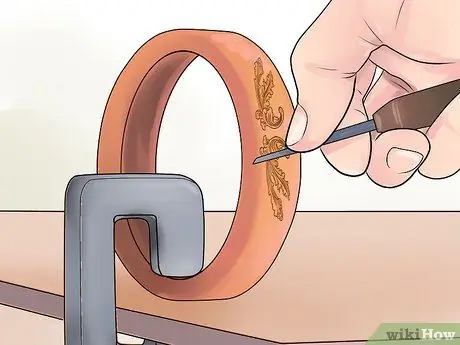
Step 7. Carve out your design
Use the tool of your choice to turn your image into an engraving, applying pressure to the part from an angle to cut the parts out of metal. For your first try, try to keep the tip of your tool at the same angle throughout the carving process. Start by working straight lines on both sides until the cut is deep. Use this as a starting point to move the rest of the line. To carve a line with a complicated shape, like the letter J, finish the straight line first. When the straight line is complete, start working on the more difficult parts.
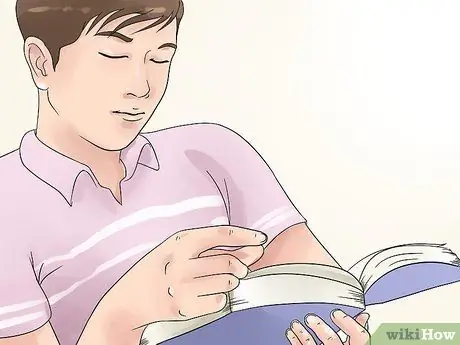
Step 8. Learn more
Carving is an art form that takes a lifetime to practice and develop. If you are interested in a new technique, machine engraving, or practical advice on improving your equipment, there are many resources available:
- Search online “engraving forums” to find an engraver community. If you are interested in a special type, you may be able to find a forum or sub-forum dedicated to precious metals, iron, or carving other types of metal.
- Find a book on carving. Books on carving will probably be more detailed than what you can find online about carving. If you're not sure what book to look for, ask the people on the carving forums.
- Study with a local carver. This means you will need to enroll in a community college or find a local carving studio that holds occasional workshops. If you're serious about engraving, consider volunteering for a free job to work with an engraver or enrolling in a one-year engraving program.
Method 2 of 3: Carving Wood with an Electric Power Tool
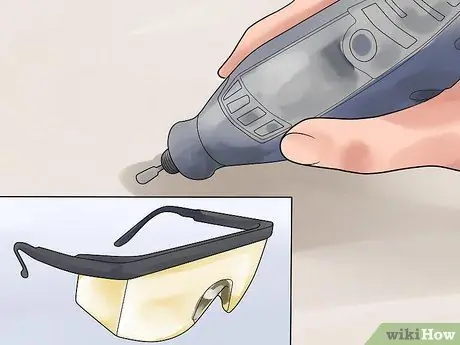
Step 1. Select a rotating tool
Most of the ends of the “dremel” or “router” can penetrate the wood. The table router can be set to a fixed depth, and it is recommended to make simple emblems and wood carvings. Alternatively, a hand tool will make it easier to change angles, allowing you to experiment with different cut styles.
- '"You are recommended to use eye protection'" when using a rotating device, to protect yourself from flying particles.
- If you plan to create a difficult design with an extreme level of detail, use a Computer Numerical Control machine or CNC.
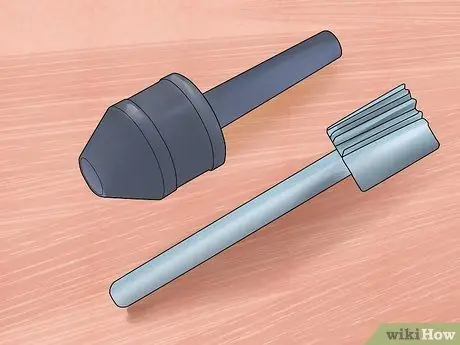
Step 2. Choose the tip to engrave
There are different ends that you can attach to the ends of the tool so you can make different types of cuts. The bull nose type is especially useful for hollow surfaces and cylinder bits for flat surfaces, while the flame bit's teardrop shape can give you fine control of the type of cut you want by changing the angle. Many other types of ends are dedicated to specific purposes, if you decide to take the art of carving more seriously.
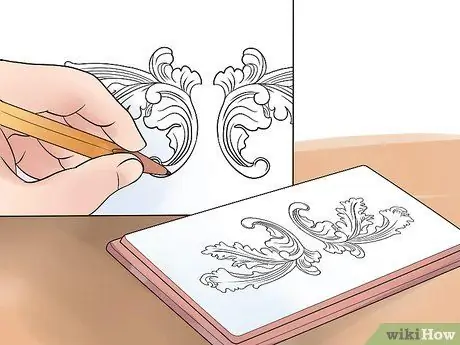
Step 3. Draw or transfer the design to the wood
When you engrave wood, the level of detail is limited to the width of the engraving tool and the precision of your hand. If you're not comfortable drawing on wood, print your design on a polyester lining such as "Mylar," and stick it onto the wood.
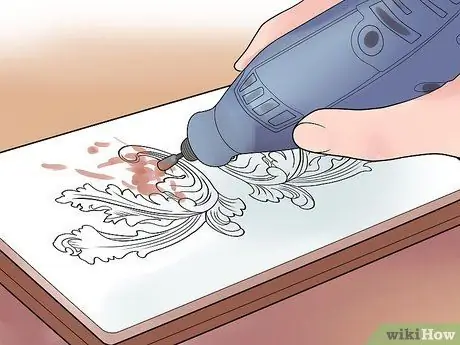
Step 4. Engrave the design with your tool
Turn on the power tool and slowly lower it into the wood. Move slowly and quietly throughout the design. It takes a slightly deep cut to achieve a three-dimensional look, so start with a shallow cut, then cut again a second time if you're not satisfied.
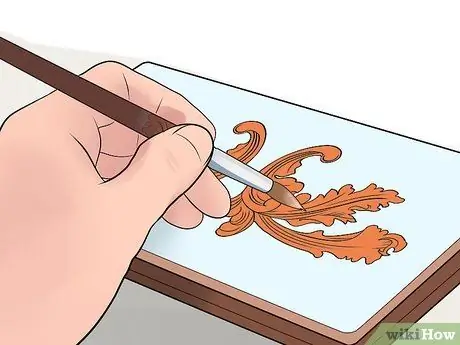
Step 5. Paint the wood (optional)
If you want your engraving to stand out more, try using paint on the cut. Use paint on the original surface with a different color to make it look more interesting. Transparent wood paint or polish can also help keep your wood from becoming worn and torn.
Method 3 of 3: Hand Carving Wood to Create a Mold Pattern
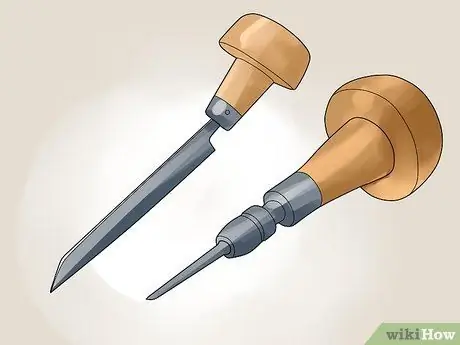
Step 1. Choose a tool to engrave
There are a variety of handheld engraving tools you can use. To create detailed drawings, as you can see in 19th-century books, choose two or three tools to produce different effects. Here are three of the most common handheld engraving tools:
- '"Spitsticker'" is used to carve flowing lines.
- The '"Graver'" produces a line that swells or shrinks when you cut, depending on the changing angle of your tool.
- A ‘scroper’”, with rounded or square ends, carves large sections of wood to create white space in the printed image. This tool may not be needed if you don't print your design.
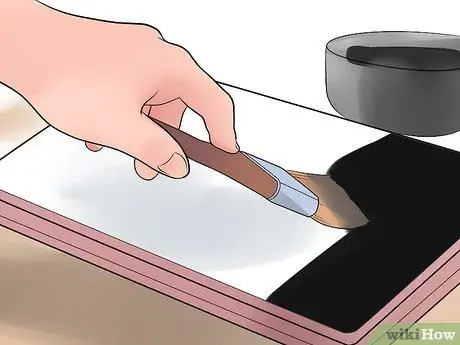
Step 2. Apply a small layer of ink to the wood
Take a bottle of black ink for the pen and use a brush or cloth to cover the flat wood. This will allow the part you've cut to stand out, so it's important not to apply a lot of ink to the surface.
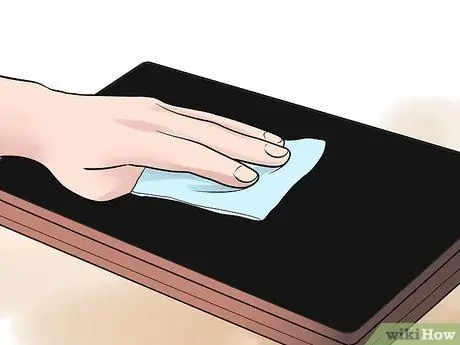
Step 3. Check that the wood surface is ready
Let the ink dry completely. When it's dry, check for rough patches of ink on the wood. If so, get rid of it by rubbing it vigorously with a tissue.
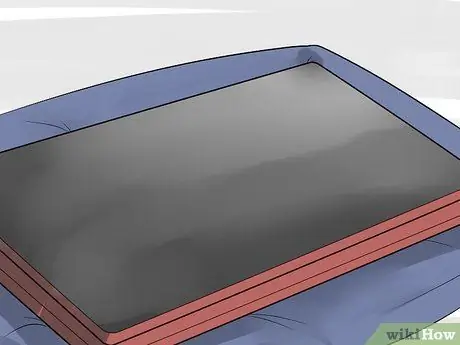
Step 4. Wooden supports (optional)
Small leather sandbags make a solid support for the wood, whichever direction you push. Clamping the wood on the table is not possible, as you will need to move the wood as you carve.
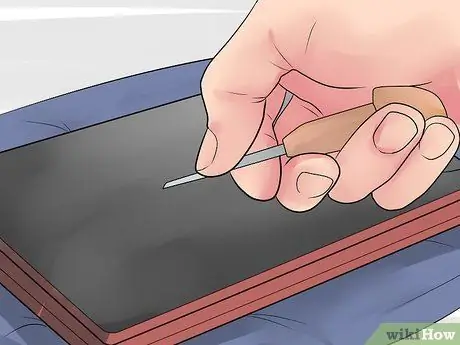
Step 5. Hold the tool to engrave
Hold the tool as you would a mouse, with your hand resting on the handle without applying too much pressure. Press on one part of the metal rod with your index finger, and press on the other side with your thumb. Let the back of the handle rest in the palm of your hand; when engraving, you will push the back of the handle to press.
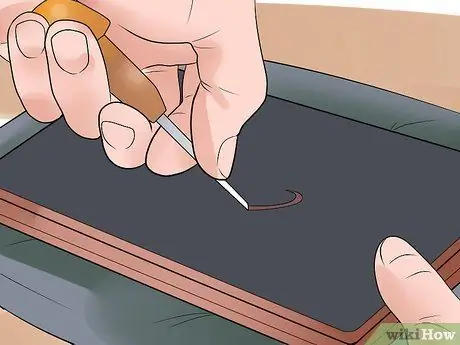
Step 6. Carve the wood
Press your tool into the wood at a shallow angle to carve. Use your other hand to move the wood slowly as you press with your tool. Cut no more than 1 cm at a time before you adjust the position of your hands. You will need to practice a few times before you can cut finely.
- If your tool quickly dips and sinks into the wood, your carving angle may be too steep.
- The graver tool can be moved gradually to a steeper or shallower angle to widen or narrow the drawn line. This will take practice to use properly, but it is a good skill to develop in wood carving.
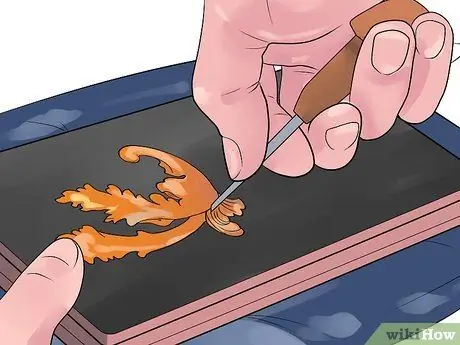
Step 7. Experiment with your way
One way to carve wood is to cut the lines from the design first, making them a little too big so you can smooth out the details with a smaller tool. There are many stylish shapes of shading, but the series of small parallel lines in the “rain fall pattern” “crossing the line sometimes produces the most natural effects
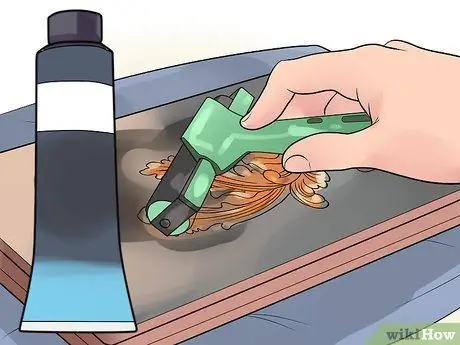
Step 8. Add ink to the engraving
Once the wood is engraved, you can transfer the result to paper as often as you like. Purchase a black print cartridge for this. Apply small amounts of ink to flat and curved wood, and use a hand roller or brayer to spread an even layer of ink over the entire surface. Add ink if necessary, and continue to coat the wood surface with even pressure until the wood surface becomes smooth.
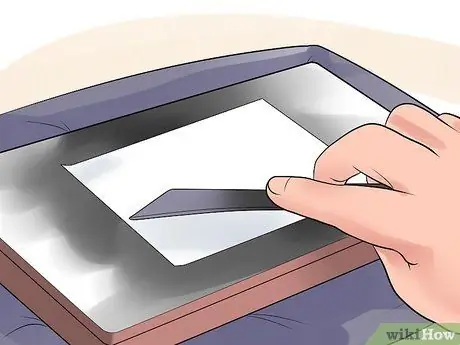
Step 9. Transfer your design drawing to paper
Place a piece of paper on the wet wood, do not move it when it comes into contact with the ink. Lift your paper when the ink is applied to the paper, and your paper will have a print of your design. Repeat this process as many times as you want, re-coating with additional ink whenever the wood starts to dry.
- If the burnisher doesn't roll up easily, rubbing it against your hair will probably make it slick, without staining the paper
- Look for a burnisher specialized for creating printed patterns, as there are tools called burnishers in other professions as well.
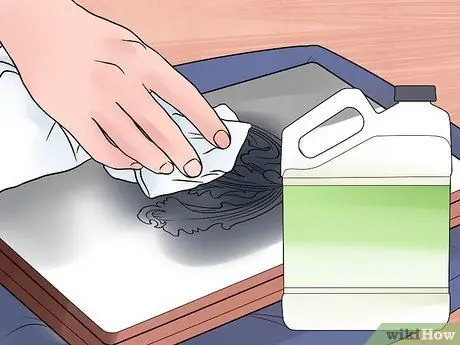
Step 10. Clean your equipment
After the printing session, clean the ink from the engraving and other equipment using mineral water or vegetable oil and a clean cloth. Save your engraving for later use, if you plan to print again.